Value Stream Mapping (VSM) strives to uncover the areas where production can improve. It's a practice aimed at identifying every single aspect of a business - processes and, from there, pinpointing where waste occurs. While you can limit/define the process at your discretion, it's best to map the process from supplier to the customer. It is only after this discovery that managers can then work to improve production to eliminate the waste.
Without any tools, sniffing out waste is a daunting, overwhelming proposition. Where do you start? How does one implement change on a process that's been in place for so long? Some employees may have been stuck on the floor so long that they can't think of any other way to manufacture your product - the current process feels set in stone, unchangeable. It's precisely for this reason that Kaizen master Shigeo Shingo, forefather of Lean Methodologies and for whom the prestigious Shingo Prize was named after, pioneered this practice, which later became part of Toyota's production system.
The VSM has a disrupting effect (it details and assesses each activity involved in producing a business) product. VSM represents flow of materials from supplier, through the entire production line. In many ways, a VSM is an extension of a process map, but the big difference is this: VSMs provides a unique level of detail that allows for easy identification of waste within the process. When the process is drilled down to such minute detail, it's easy to see where lagging wait times between steps have a huge effect on overall production.
If an OEE calculation identifies that waste exists, then a VSM shines a light directly on the areas where waste occurs. From here, your team can work toward solutions. Without a VSM, you simply know that your company has waste, but not where it's coming from. Without that information, it's impossible to prevent it from happening in the future.
After you've created your VSM, you'll have a clear understanding of where waste is occurring, and you'll have a vision for what your future VSM will look like.
Getting Started
it's important to have a specific idea of what to map. If you're a company that solely manufactures one product or family of products, you can focus on the entire process, but if you're a larger operation with many different products, it might be best to narrow the scope of the VSM and take smaller bites.
There are a few different methods to narrowing the scope for your VSM:
- Map specific product or family of products
- Map the most popular/highest value product
- Map those product ranges that are predicted to increase in value or demand
Create Value Stream Mapping (VSM) Key
Since production processes are complex, multi-layered beasts, it's important to create an easy-to-follow key minimizes the need for text. This will make your map less cluttered and easier to follow. A VSM with tons of text gets busy, overwhelming, and hard to read; symbols make it possible to convey the full scope of a production process while keeping the map accessible.
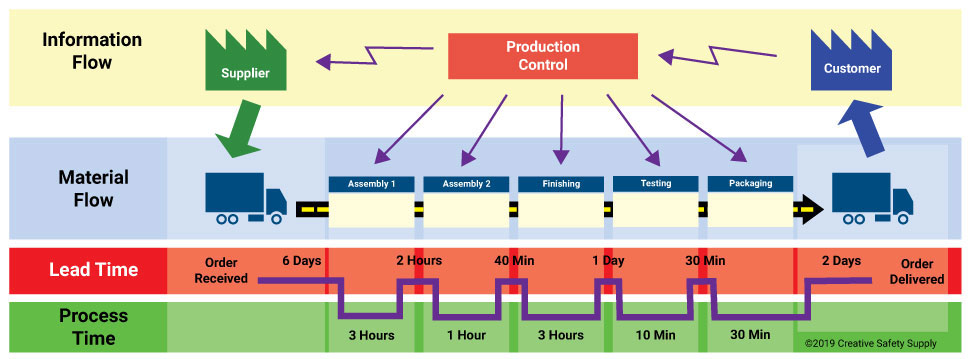
VSM Process Steps
Now that we've defined the parameters for our process map, we're ready to outline our production process. It's crucial to list all the stages of production. it's important to be exhaustively thorough here. It helps to trace the final product back from the customer's hands to the supplier of raw materials.
Since we've run through the process a thousand times, it can feel too close to break down; therefore, thinking of it in this new way may make it easier to list each stage.
Important distinction: each task doesn't have to be broken down; we just want to see the various places the product goes, and how much wait time occurs before product moves to next location.
How to Find Waste in Production
Once we've created our VSM, we'll be able to see in one place where the problem areas within the production system lie.
Here are the common issues revealed through VSM:
- Excessive Inventory
- Long wait times
- Low uptime
- Excessive Setup Times
- Poor QA
To see how to identify waste in VSMs, let's look at an example. Let's say we own a furniture manufacturing business. Our production process is as follows:
Raw materials are received. Then they go through these steps:
- Cutting
- Drilling
- Sanding
Product is then sent out to customers.
Now that we know the steps, let's calculate the cycle time versus wait time. It is in this equation where we can identify our bitter foe: waste. To get an accurate portrait of our production times, go to the line and see exactly how long it takes. Don't rely on old data or reports - go to the place itself and witness the production get executed step by step. This is called a gemba walk, and it is often during these that we identify the things that need to be changed.
Our cycle time for each stage of production is thirty minutes. Let's say that between cutting and drilling there's a 180-minute delay, and there's an additional 15-minute wait time between drilling and sanding.
Create an Ideal/Future State VSM
We've identified that we have quite a lot of waste in the form of wait time to deal with, but how do we do that? What we really need here is a vision of what we want our production process to look like - an ideal state.
This future VSM is your immediate goal. It's the plan you'll be working toward to see new results within the next quarter. It can sometimes help to bring in an outside expert to help build this new map, and it's very important to communicate with senior management to make sure the future vision is agreed upon.
Other considerations when construction future state:
- Kanban systems might remove the need for unnecessary planning and scheduling
- On your ideal/future state VSM, use the Kaizen burst symbol to illustrate where improvements can be made
- Look into other Lean methods to help improve production