Simply put, OEE (Overall Equipment Effectiveness) is a manufacturing best practice for assessing how productive a facility is on a day-to-day basis. When production lines are pumping out thousands of units a shift, it can be difficult to gauge just how efficient equipment and operators are performing, but analyzing production rates and figuring out how to improve production processes is a key component to a successful, sustainable business.
Don’t know your OEE Score?
The OEE calculator helps you determine Availability, Productivity, and Quality.
History of Overall Equipment Effectiveness
Seeking to find a better, more accurate way to calculate efficiency in manufacturing and see where and why loss is occurring, Seiichi Nakajima invented OEE by figuring the maximum rate a machine could theoretically produce and weighing it against the number of units it produces. OEE is an essential part of TPM (Total productive maintenance), the system that changed the way the world maintains and operates manufacturing facilities.
An industry pioneer and father of TPM, Nakajima was unsatisfied with older, traditional efficiency calculation models that were easy to manipulate. Nakajima's OEE factors in all of the possibilities for loss in production. To reveal the true rate of production in a facility, all losses must be defined and visualized. From here, a business can make adjustments to prevent loss.
Nakajima introduced OEE in 1982 in his book TPM tenkai, which was published in Japanese by the Japan Institute of Plant Maintenance. By the late eighties, thanks to the English translation of Nakajima's book, OEE and TPM became popular throughout the Western world.
How It Works
OEE revolutionized how manufacturers assessed loss because it took into account every possible reason for the loss. Every breakdown, shift changeover, line restraint, coffee break, lunch, minor stoppages, reduction in production speed, and out-of-specification units - OEE takes all these seemingly small losses that happen at every facility and calculates them to give a comprehensive portrait of just how much a company is losing.
Metrics for measuring OEE:
While there are a few different ways to measure OEE, the most common and easiest way for determining the effectiveness of the production floor is to figure out scheduled hours of production and what maximum production numbers would look like. Then, you'll weigh those numbers against the OEE factors: availability, performance, and quality.
- Availability: The portion of the metric that represents the scheduled time a production line is in operation (AKA uptime).
- Performance: The portion of the metric that represents the actual speed at which the machines operate.
- Quality: The portion of the metric that represents the number of saleable units compared to total units produced.
These metrics equal effectiveness in the following way:
- Making the right product: right unit or SKU is produced at the right speed (Performance)
- Making it the right way: no re-dos, no defects, no waste (Quality)
- Making it at the right time: producing as planned, keeping the machine in operation, minimizing time losses (Availability)
To calculate OEE, you'll need to measure the APQ (Availability/Performance/Quality) against the maximum rate of production.
OEE In Action
Let's say we own a button factory. We want to get a complete understanding of why our production rate is in its current state. First, we must find the maximum rate our machines can produce. For the sake of example, let's say our equipment can produce 120 buttons per minute. Given the theoretical maximum speed, at the end of the eight-hour shift (480 minutes there should be 57, 600 units.
- 1 shift = 8 hours = 480 minutes
Maximum production speed= 120 per minute
480 x 120= 57, 600 units
Then you need to figure out what we produced at an endpoint in the production process such as what's on the pallet going to the warehouse. If there are only 28,800 good products on the pallet your effectiveness was 50%, but how do we figure out why we lost out on half of our production?
When broken into its main components - availability, performance, quality - OEE tracks down where we lost the other 28,800 units. Every day that we run 50% OEE, we can lose units for different reasons, and every loss has its cost structure.
Availability
To start our discussion on how we manage time in our button factory, let's take a standard shift of 480 minutes. Our operators take two ten-minute breaks and a thirty-minute lunch for a total of 50 minutes. We also have 2 changeovers of 35 minutes each and lose 60 minutes of machine downtime during the shift. For the rest of the shift, the machine is up and running.
- Breaks = 10 minutes in AM + 30 minutes for lunch + 10 minutes in PM = 50 minutes.
Changeovers = 2 x 35 minutes = 70 minutes - Machine downtime = 60 minutes per shift
Total = 180 minutes lost time
Our shifts maybe 480 minutes, but a great deal of our time is spent out of production. We've lost 180 minutes; only 300 minutes left to be effective. Even at full speed with no quality losses, the best we can do is be 62.5% effective each shift. This ratio is called availability.
- 480 minutes - 180 minutes = 300 minutes
300 * 480 = .625 = 62.5% availability
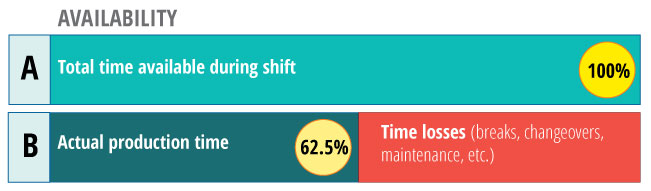
Now that we know how much actual operation time we have, let's see how we spent it.
Performance
Assuming our machine has an ideal cycle time (also known as takt time) of 1 second per 2 buttons, which is 120 buttons per minutes, we want to determine the actual speed at which our production system is running.
If we're running at maximum speed, that means that in the remaining 300 minutes, the machine should be able to make 36,000 buttons. If at the end of a shift, the machines would have produced 36,000 buttons during the time it was running, it would've been performing at 100% speed. If the production speed is at, say, a cycle time of 1.5 seconds, it would slow down the maximum speed by 2/3, and thus its performance would be 66.7%. Now we have to find how many buttons we make when our factory performs at 66.7%.
- 300 x 120 buttons = 36,000 units
1.5 seconds per 2 buttons = 1 * 1.5 = 66.7% performance - 66.7% x 36,000 buttons = 24,000 units
Running at 66.7% performance means that we're losing another 300 x 33.3% = 100 minutes. To put in another way: since our line ran at 2/3 its maximum speed, it means we produced 2/3 x 120 = 80 buttons per minute.
If all output meets specifications for saleable products, what would be the effectiveness?
From our starting point of 480 minutes, we've lost 180 minutes to inoperative time and 100 minutes to slow cycle time. Here's where we're at now:
- 480 - (180 + 100)/480 = 41.7 %.
- (480 minutes - (180 minutes + 100 minutes)) * 480 = 41.7% Efficiency
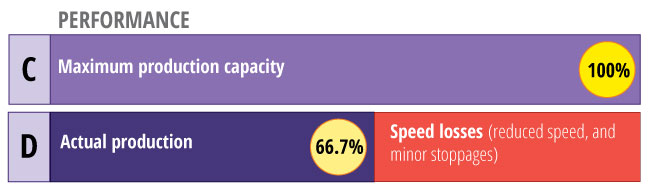
So far, we're a long way from the maximum number of units our machines can produce in a shift, and we're not yet done calculating OEE.
Quality
Whether or not the 41.7 % reflects our actual effectiveness depends on how many of our buttons are saleable. If from the 24,000 buttons there were 6,000 that didn't meet specifications, then the quality rate of those buttons was (24,000 - 6,000) / 24,000=75%, or, if we want to convert to minutes, loss would be 6,000 buttons / 120 buttons per minute = 50 minutes due to quality.- (24,000 - 6,000 defects) * 24,000 = 75% Quality
- 6,000 buttons * 120 buttons per minute = 50 minutes lost Quality
In theory, we could produce 480 x 120 = 57,600 buttons. At the end of the shift, the actual number of saleable buttons are 18,000; therefore, the OEE is 31.25%.
- 18,000 * &57,600 = 31.25%
Availability (62.5%) x Performance (66.7%) x Quality (75%) = 31.25%
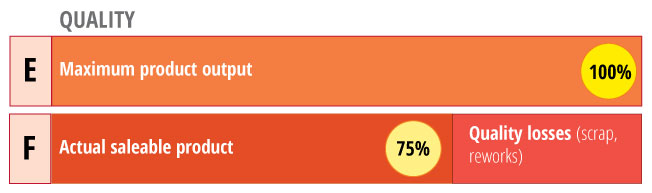
So We Know OEE. What Now?
While it may seem discouraging to know our button factory is running at 31.25% OEE, the good news is that now that we've been able to visualize our losses, we can make a plan of action to attack these problems and increase production.
To help us combat our losses and improve our manufacturing processes, we should implement Lean methodologies into our production line:
- Gemba - Japanese for 'the real place,' Gemba is the practice of going to the place where value is created for the customer. This gives management a better understanding of how the product gets made and discover what needs to change.
- Six Sigma - created by Motorola in the late eighties, Six Sigma is an ideology that reduces the number of product defects to near-zero levels.