- What is a Bottleneck (or Constraint) in Manufacturing?
- Causes of Bottleneck
- Common Mistakes to Avoid During Bottleneck Analysis
- What is a Bottleneck Analysis
- Benefits of a Bottleneck Analysis
- Performing a Bottleneck Analysis
- Dealing with Bottlenecks: Examples of Solutions
- Bottleneck Analysis Tools and Softwares
- Training Teams to Watch for Bottlenecks
Improving efficiency within any process, whether it be for manufacturing, distribution, or another business objective, is an essential step in improving the bottom line for companies. Efficiency improvement also enables businesses to deliver quality products to their customers in a consistent manner.
The road to quality management, quality assurance, and overall plant success begins with the elimination of downtime. There are numerous different aspects of work that have the potential to cause slowdowns and disruptions of work. Unfortunately, bottlenecks are some of the most strenuous situations of downtime a company can face, resulting in low performance and productivity capabilities.
With the right Lean management tools, you can improve your understanding of what causes bottlenecks, how to get to any root causes, and prevent a blockage from occurring in the future.
What is a Bottleneck (or Constraint) in Manufacturing?
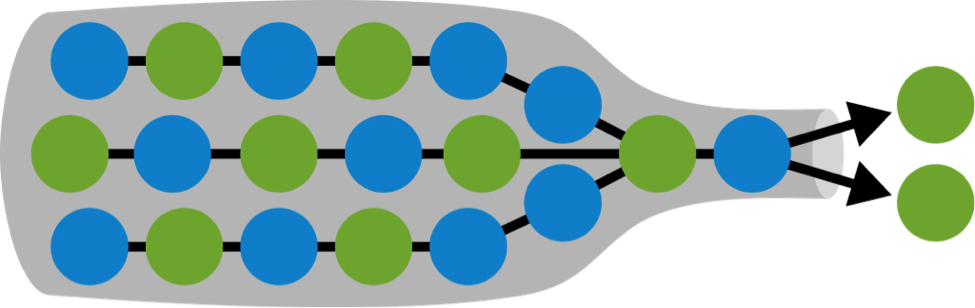
A bottleneck is any area along the production line where the number of tasks to be completed becomes too much for the maximum workload capacity. This problem often results in delaying subsequent steps in the workflow. Bottlenecks can stem from an entire stage of work, not enough employees, a lack of resources, and even computer issues.
There are three different classifications of bottlenecks that businesses can run into on any given day. Those include:
- Production line bottlenecks – When the output of one process is faster than another it leads to an increase in material piling up, waiting to be used.
- Supply chain bottlenecks – A poorly designed material flow from suppliers is what results in a supply chain bottleneck. This can be the result of lackluster inventory management, changing products frequently, financing issues, or an incorrect forecast of demand.
- Bottlenecks caused by People – A lack of effective training leads to inefficient work, which causes ineffective communication. Both are attributed to low employee morale due to constant work interruptions.
Short-term vs Long-term Bottlenecks
Aside from the different causes of bottlenecks identified above, there are also two different classifications that bottlenecks fit into. Those are:
- Short-term bottlenecks – These types of bottlenecks are caused by short-term problems. For example, a bottleneck can occur if an employee is out sick for the day or if a delivery is running late. These usually aren’t cause for concern, although you may do well to have a backup plan if something like this does occur.
- Long-term bottlenecks – These types of bottlenecks are more cause for concern. Long-term bottlenecks require management techniques such as root cause analysis or the creation of a fishbone diagram to get to the bottom of the issue. Long-term bottlenecks may come about because of an exhaustive audit procedure, a disorganized inventory system, or even an entire lack of real-time data that identifies issues.
Long-term bottlenecks are the types of bottlenecks that should be investigated immediately to reduce wasteful practices.
Causes of Bottleneck
Bottlenecks during the manufacturing process can arise from various factors that stall the smooth flow of production. Here are some of the most common causes:
Communication Breakdowns
Effective communication between teams or departments is very important. Communicating through verbal exchanges or paper documentation can cause a significant bottleneck within the manufacturing process, such as an operator taking a break or the misplacement of a clipboard. A solution to this lies in the implementation of automated machine data collection systems. The manual compilation of production data not only consumes valuable time but is also susceptible to inaccuracies, resulting in compromised communication and understanding.
Unclear Processes
Having unclear processes and old equipment really messes things up in manufacturing. Think about how long those machines have been running and how often they get checked or fixed up. Take a good look at how things are done to figure out where things are getting stuck. Also, if the factory setup is poor, like if there's no storage to put materials, that's going to cause more delays and damage.Bad Forecasting
It is essential for manufacturing companies to bring in components and materials efficiently in order to avoid excess storage and ensure readiness for use. Failure to prepare necessary materials can lead to bottlenecks in production. Predicting high demand through forecasting and prediction is crucial. Utilizing analytics tools and monitoring customer behaviors and industry trends are necessary for effective long-term planning and prevention of bottlenecks in manufacturing companies.
Limited Machine Capacity
As the deadlines draw near, your equipment may need to exceed the normal operational capacity to meet the requirements. Such behavior can lead to the likelihood of machinery breakdown. Whether you are overloading a single stage or all stages of the production process, the danger of causing a critical bottleneck remains consistent.
Lack of Automation
Relying too much on people doing things manually instead of using automation tools increases the likelihood of mistakes in important parts of the production process. Automation, whether it's machines or computer software, is good for performing repetitive tasks without needing to make important decisions.
Common Mistakes to Avoid During Bottleneck Analysis
Bottlenecks can affect your business growth; therefore, it is important to address them accurately to avoid common errors that may arise.
Ignoring Small Bottlenecks
mall interruptions in the workflow may be easy to ignore, but just a five-minute delay happening multiple times daily can ultimately result in the loss of an hour of productivity. If you observe that your team wastes a few minutes each day waiting for a slow software to load, address the issue promptly and find a quicker alternative.
Overlooking Employee Input
Managers often concentrate solely on data analysis while neglecting the valuable insights provided by their staff members. It is essential to remember that your team members are the ones directly facing operational challenges and obstacles. For instance, a sales representative currently dedicates a significant amount of time to manual data entry. Implementing automation in this process could potentially enable him to allocate more time to engage in sales activities.
Focusing on Symptoms, Not Causes
A drop in sales could seem to be an issue with your sales team, but it might also be the result of a bottleneck in product development that is causing shipments to be delayed. Investigate more thoroughly and look past the cursory examination.
Ignoring Stakeholders Reviews
Management's failure to listen to the feedback and insights of employees directly engaged in the process can result in the oversight of valuable information and potential solutions to improve efficiency and productivity. Employees have firsthand experience and insight into the difficulties within their roles or departments. Ignoring their input could result in missed chances to recognize and resolve bottlenecks, ultimately causing prolonged delays, decreased output, and decreased overall performance.
Neglecting Data Analysis
Insufficient or full of error data often hinders the effectiveness of bottleneck analysis. Using outdated or partial data may result in incorrectly pinpointing bottlenecks, which leads to ineffective solutions.
Overreliance on Technology
It is commonly believed by many that technology is the ultimate solution for all obstacles, yet sometimes a simple adjustment in processes can be effective. In some cases, the effectiveness of a routine team meeting can outweigh the benefits of getting a new project management tool. The critical factor lies in creating a balance between utilizing technological resources and human problem-solving capabilities to achieve the most efficient solutions.
What is a Bottleneck Analysis
Identifying the cause of a bottleneck requires the company to perform a bottleneck analysis. Like a risk assessment, a bottleneck analysis is used to identify a problem. However, in this case, that problem is a slowdown in the workflow rather than a hazard that poses a risk to employee safety.
Once the cause of the bottleneck is identified, the company can start to work towards potential solutions to be able to push product through the production line at a more consistent rate again.
Benefits of a Bottleneck Analysis
In addition to eliminating the bottleneck at its source and achieving a steadier workflow, a facility can enjoy the following additional advantages:
- Waste elimination – Bottlenecks are often caused by unnecessary or inefficient processes, which can result in a variety of types of waste. Being aware of any waste is the first step in making improvements to the existing processes.
- Increased knowledge - The more a company knows about a specific process, the easier it is to make smart decisions and take control of the throughput capacity. Knowledge provides advantages not only when it comes to eliminating bottlenecks, but also when making large process improvement decisions in general.
The productivity of a facility depends on how much value it can produce for its clients. As waste becomes more rare and the knowledge base of the workers increases, they then become able to produce consistent and highly-valuable materials.
Performing a Bottleneck Analysis
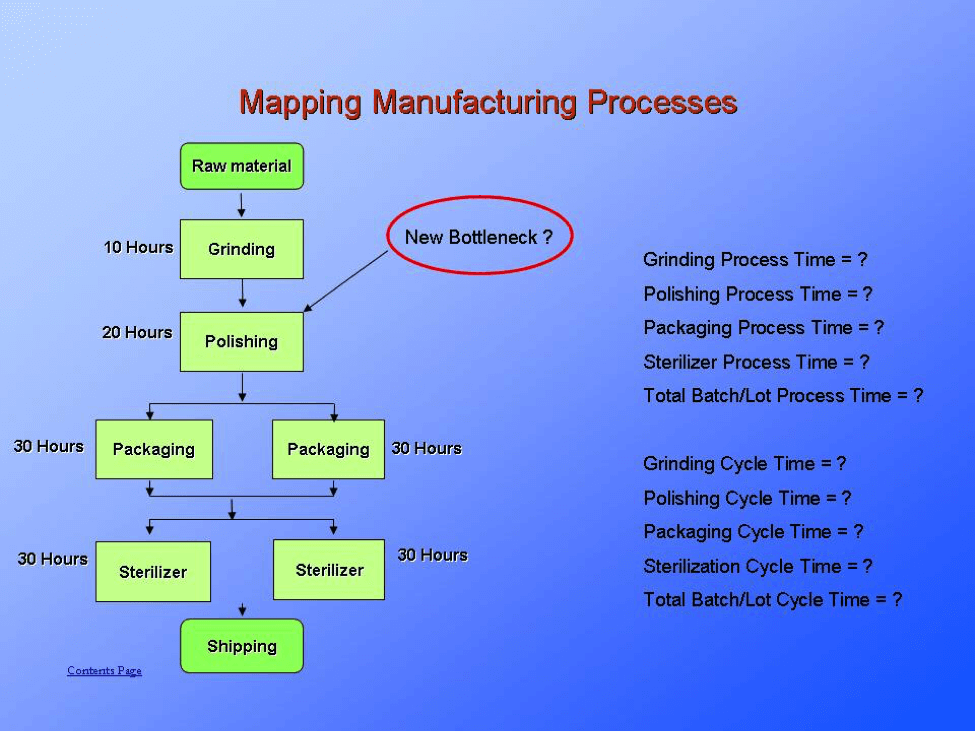
Specifically used to identify the cause of a bottleneck, or to identify where a bottleneck is likely to occur in the future, bottleneck analyses are an essential tool for all businesses that work with sequential steps to complete a product or service. In the end, no matter what the reason was for conducting this analysis, its completion will provide important information about how a product moves through the production process, and how processes can be improved. Talking about performing a bottleneck analysis and following through with performing one is often one of the most difficult parts of the process. The following examples of performing a bottleneck analysis will help you start your very own elimination process for bottleneck problems.
Gathering Information
Performing a bottleneck analysis is a detailed operation that begins with the company gathering as much information as possible about the manufacturing flow of a particular product or process.
When performing a bottleneck analysis, it is important to look at both the specific step where the bottleneck is occurring as well as the entire manufacturing process. Looking at the entire process will provide essential information about the steps leading up to the bottleneck, the bottleneck itself, and what takes place directly after the bottleneck. It is also necessary to note that if a bottleneck early in the production process is eliminated, that action may result in a new one forming further down the line.
A properly performed analysis will not only help to find solutions to the existing bottleneck, but it will also help to prevent new ones from forming.
Using Lean Manufacturing Tools
Some bottlenecks can be identified and resolved quickly and without any need for extensive analysis. In most cases, the tools used for this process are going to be either a written flowchart or a computer program. Computer programs geared towards process flow management allow a company to enter in information gathered from each step of a process so that it provides a visual display of what is happening along the workflow.
Bottlenecks can easily be detected if the business utilizes the Kanban method. By implementing this technique, visualizing the flow of work on a Kanban board or within a software program allows employees to see where tasks are piling up within a production process or within a supply chain. For that reason, Kanban is an excellent tool for continuous improvement endeavors regarding consistent and efficient workflow.
Other bottleneck analysis tools available to use include the DMAIC method and the Theory of Constraints method. These are only some of the tools that can be used in an analysis but finding the right one is important for maximizing positive results. For a simple situation, using a template can be an effective choice. However, when there are multiple products or different flows, a more advanced set of tools should be used.
Avoiding Future Bottlenecks
Completing a bottleneck analysis is the first step in a longer process of continuous improvement regarding the efficiency of production. Taking the information gathered from the analysis and using it to make process changes is the next task that must be completed.
Companies that take the time to analyze this type of information and use it to avoid bottlenecks in facility operations will benefit from a more efficient process long into the future. That said, rather than just identifying what appears to be the surface cause of a bottleneck, it is better to take the time to really dig into the data to discover the root cause of the manufacturing constraint. This will not only get rid of the bottlenecks as soon as possible, but also set the processes up to prevent them from occurring again in the future.
Dealing with Bottlenecks: Examples of Solutions
In addition to identifying exactly where a bottleneck forms, bottleneck analyses also aim to identify potential solutions. Every company is going to have its own way of solving this type of problem, but the following are some common options that should be considered whenever looking for ways to eliminate bottlenecks in the workflow.
- Add additional capacity – If a bottleneck is being caused at a specific step in the production process, consider adding additional capacity. For example, bottlenecks can occur during painting tasks because it may take a longer time than other steps. Adding a second painting station will effectively double capacity and should eliminate the bottleneck problem.
- Eliminate wasteful steps – Some products may have extra features that customers don't want or need. If these types of steps are causing a bottleneck, it is a good idea to eliminate them all together to keep work moving along smoothly. Eliminating waste is an important part of fixing bottlenecks and improving efficiency.
- Add staff – One of the most common causes of a bottleneck is insufficient staffing to complete a task. Hiring additional employees to work in a specific area is an excellent solution.
- Reduce production – While reducing the rate of production is not typically a good long-term solution, it is better to reduce production rates than to have huge amounts of inventory building up along the production line.
- Adjust the flow – It is often possible to adjust the workflow to keep things moving. When a bottleneck forms, see if the step where it is occurring can be skipped and then completed later. This is only a good solution for situations where a temporary bottleneck forms for some reason, such as a broken machine or absent employees.
Brainstorm ways to remedy process constraints when they occur. It will help improve manufacturing operations and help the team keep product demand in check.
Bottleneck Analysis Tools and Softwares
Bottleneck analysis can be complex, but there are tools available to facilitate this process and identify mistakes in your operation. Here are some of the common types of bottleneck analysis tools and software:
- Process mining software: This software analyzes data from your enterprise resource planning (ERP) system and other sources to identify bottlenecks in your workflows. Process mining software can help you to visualize your processes, identify areas for improvement, and track the impact of changes you make.
- Task mining software: This software uses task capture technology to analyze user interactions and activities within business applications. Task mining software can help you to identify bottlenecks in tasks and processes that are not captured by traditional ERP systems.
- Process simulation software: This software allows you to create a digital model of your production process. You can then use the software to simulate different scenarios and identify potential bottlenecks before they occur.
- Business intelligence (BI) tools: BI tools can be used to collect and analyze data from a variety of sources, including production data, sales data, and customer data. BI tools can help you to identify trends and patterns that may indicate bottlenecks in your operation.
- Low-code/no-code workflow management software:This type of software allows you to easily create and automate workflows. Workflow management software can help you to identify and eliminate bottlenecks in your processes by streamlining the flow of work.
The best bottleneck analysis tool for you will depend on your specific needs and budget. However, all of the tools listed above can be helpful in identifying and eliminating bottlenecks in your manufacturing operation.
Training Teams to Watch for Bottlenecks
Far too many companies wait until a serious bottleneck occurs before taking action. It is important to act quickly when this occurs to avoid slowdowns, but it is even better to avoid bottlenecks entirely. The best way to do that is to have employees watching out for early signs of a problem.
Training teams to watch for bottlenecks will typically involve department managers first informing front line employees on what to watch for. Some common recognizable features include the following:
- Trouble keeping up - If one department or step in a workflow process is constantly falling behind and other areas don't have this issue, it is an early sign of a bottleneck problem.
- Shuffling staffing - If a floor manager needs to take staffing from one area of the facility and move it to another to help keep up, this can be another sign of a problem. Shuffling staffing can be an effective temporary solution before a more long-term fix can be identified.li>
- Short staff - When employees from a specific area call in sick or take a vacation day, does it cause an unreasonable burden to other team members? If so, the staffing or workflow should be evaluated for improvement opportunities.
- Other - In general, listening to the concerns of employees can be one of the best ways to discover potential issues. Employees are typically the first to notice that there are problems and can be an excellent 'alarm' to watch out for future problems.
Anytime issues like these are found, it is a good time to perform a full bottleneck analysis on the process in question. Since the problem isn't a serious issue yet, the company will have some extra time to be able to perform a full analysis without interrupting workflow.
Similar Articles
- The Five Whys (Root Cause Analysis)
- Fault Tree Analysis
- Job Safety Analysis
- Kano Model (Analysis & Diagram)
- Value Stream Mapping (VSM Analysis)
- Hazard and Operability (HAZOP Analysis)
- Job Hazard Analysis: Addressing Coronavirus Risk in Your Workplace
- Quality Control in Manufacturing
- Organizational Development Process