Those who work in any safety-focused role in any industry have heard a lot about OSHA, and the many requirements they have in place. While knowledge of its existence and the regulations they have is important, it can be very beneficial to have a fuller understanding of what OSHA is and how it can impact a given business.
Any company that wants to operate in America, and even many that just work with companies based in America, will need to be aware of what OSHA is and how they operate. While it can seem overwhelming at first, it is well worth the effort to learn more about this important agency and how it will impact the safety of any facility.
What Does OSHA Stand For?
OSHA stands for 'Occupational Safety and Health Administration' and it is a part of the United States Department of Labor.
What is OSHA?
OSHA got its start back in 1970 when the US Congress created the department. It is a distributed agency that has employees working throughout the country to do things like inspections, and investigations, and help businesses improve safety. The OSHA mission is stated as follows, 'With the Occupational Safety and Health Act of 1970, Congress created the Occupational Safety and Health Administration (OSHA) to assure safe and healthful working conditions for men and women by setting and enforcing standards and by providing training, outreach, education, and assistance.'
As a governmental agency, they do have the legal authority to impose fines and other penalties when a business doesn't follow their rules and regulations. It is even possible for a business to be shut down until the violations are resolved.
The organization has over 2000 employees and an annual operating budget of about $500 Million. There are very few employees who don't fall under the 'protection' of OSHA standards, which can impact businesses ranging from factories to office jobs to hospitals and everything in between.
What Does OSHA Do?
OSHA does many different things, all with the end goal of improving workplace safety so that every worker in America goes home safe and healthy each day. The different activities that are performed can be generally broken down into several different categories.
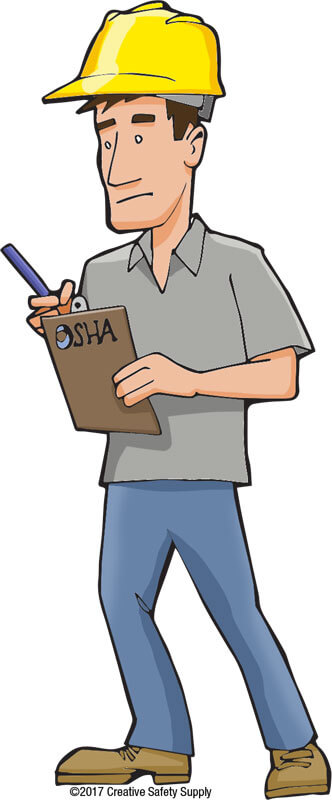
Know your OSHA incident rate?
The OSHA Incident Rate Calculator helps you find the rate of recordable injuries.
Outreach & Assistance
While many businesses see OSHA as a hindrance or obstacle to success, they are there to help. OSHA offers an extensive array of different resources to businesses to help them not only succeed in making the workplace safer but also succeed in business in general. A safe work environment has many benefits, and in most cases, will even result in an improved bottom line.
OSHA offers employers and employees things like:
- Print Materials - OSHA distributes many types of printed materials that can be used for company training and reminders. This includes documents, posters, booklets, and more.
- Training Classes - OSHA offers some training classes that employees or supervisors can attend to learn more about specific safety topics.
- Compliance Assistance - Companies can reach out to OSHA to get help in improving the safety of a facility. This can be done to inspect a facility for problems or to implement policies within the workplace that will lead to a safer overall environment.
While it is a common belief that OSHA is there just to force companies into compliance, their real goal is to improve safety. The agency would much rather identify safety problems and help eliminate them voluntarily than have to catch a company using audits or inspections that can result in fines or other problems for the company.
Cooperative Programs
OSHA operates an 'Alliance Program' that provides employers, unions, trade groups, associations, and others the opportunity to work with OSHA to improve safety. This program is a long-term partnership between OSHA and the other group where they come up with improvement opportunities, written agreements, and other things to help push forward the safety of employees.
These longer-term partnerships have a lot of benefits for everyone involved. Not only does OSHA help a company to directly improve their safety, but they can also take the data that is gathered and use it to make recommendations for other institutions. This is a win-win scenario for OSHA, companies, employees, and the community in general.
Inspections
Of course, OSHA also conducts inspections of companies in just about every industry. These inspections are conducted by trained individuals who know how to spot safety violations in a variety of industries. Some specialized auditors focus on specific types of workplace hazards, and more general individuals who can help identify a variety of different issues.
These inspections can be either coordinated with the company management or as 'surprise visits' where they come in to do an inspection unannounced. Both of these options serve a purpose when it comes to keeping facilities safe.
Enforcement
When OSHA discovers safety issues that aren't being addressed, they can resort to enforcement tactics. OSHA has a lot of options when it comes to enforcing its regulations. They can do anything from issuing a corrective warning to shutting the facility down until changes are made.
While many people fear OSHA's enforcement tactics, they are typically used as a last resort. OSHA is more interested in helping companies to improve the level of safety in a facility than penalizing them. Most companies today are also happy to make safety improvements whenever possible since this type of thing has been repeatedly shown to improve the productivity of a facility.

What Does OSHA Look For?
When conducting either a scheduled or a surprise inspection, OSHA is going to be looking for any type of safety issue that violates their regulations. In addition, they will look for improvement opportunities even if they aren't in direct violation of a specific regulation. The goal of every OSHA inspector should be to help a company identify potential hazards and eliminate them. The following are some things that OSHA watches for based on the amount of fines they gave out (in the last year data was available):
- General Requirements - OSHA issued a total of 1830 citations adding up to $3,217,665 in fines for violating general safety requirements. This is why it is so important that all companies and safety professionals are well-aware of all the different rules and regulations put in place by OSHA.
- Eye & Face Protection Violations - There are many regulations regarding eye and face safety, and companies often violate them. OSHA issued 556 citations about this, and $886,023 in fines were collected.
- Hand Protection - Hand protection is critical in many industries, but companies often forget that it is a safety requirement. 565 citations were given, adding up to $330,840 in penalties.
- Head Protection - Wearing a hard hat and other types of personal protection equipment for the head is critical for overall safety. OSHA collected $179,538 in fines related to this from a total of 79 citations.
- Foot Protection - Foot protection is all to commonly overlooked, and resulted in 55 citations adding up to $93,696 in penalties.
There are many other violations that OSHA cites, even when they don't issue fines or penalties. OSHA often notes safety violations in the workplace so that the company will fix the problem. If the issue is fixed at the next inspection, there won't be any type of fine, which is another indication that OSHA's top priority is safety rather than issuing fines.
How Do I Prepare for OSHA?
All companies, no matter how safety focused they are, need to take proactive steps to prepare for OSHA. In many situations, this simply means focusing on safety and taking the necessary steps to address problems when they come up. In other cases, it will mean taking the time to know about the OSHA requirements and performing an internal 'inspection' to evaluate whether or not the facility would pass.
Finding ways to improve safety in the workplace doesn't have to be difficult, nor does it require a facility to wait for an OSHA inspection. There are many types of safety training available to companies, each of which will provide significant benefits to both the company itself, and the employees. One of the best ways to make sure a company is always ready for an OSHA inspection is to look at the potential hazards in a workplace, and address them with safety training.
A construction company might benefit from providing ladder safety training. A hospital should provide employees with training on how to deal with blood borne pathogens and other health related risks that are present in this environment. All companies can also benefit from a good emergency action plan, which will provide information on what to do in almost any type of emergency.
This is important for all companies, but especially for newer ones. Most established companies develop a relationship with OSHA and their inspectors over time so they know what is being looked for. This helps to create and foster an environment of more open communication so that safety becomes a joint effort rather than a battle.
Resources
Similar Articles
- Quality, Health, Safety, Environment (QHSE) Management Systems
- Mine Safety & Health [Expert Advice]
- What is HAZCOM? (Hazard Communication Definition + OSHA Standards)
- Safety Audit
- NFPA 99: Understanding the Health Care Facilities Code
- OSHA Facts [Updated Statistics 2019]
- Compliance Audit
- Workplace Safety Inspections & Audits
- Forklift Safety