Kaizen is the Lean philosophy of constant, continuous improvement, working to ensure maximum quality, efficiency improvements, and elimination of waste. It’s the mindset that small process improvements over time can make a huge impact to industries.
What is the Kaizen Process?
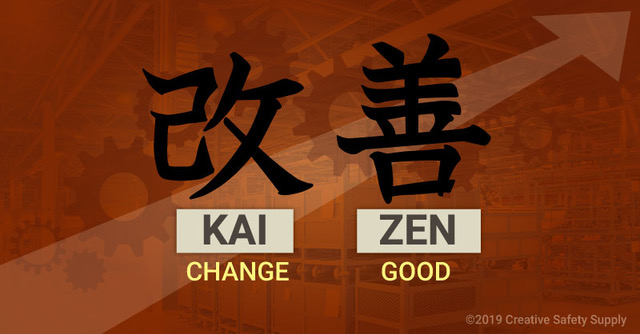
Kaizen is a Japanese term meaning “change for the better.” Kaizen is a foundational philosophy everyone in the company practices – from the CEO to assembly line workers. Businesses with a culture of continuous improvement reap many benefits, for example:
- Smoother and more efficient processes
- More accurate KPIs
- Improved employee morale and engagement
- Lower operating costs
- Cleaner, safer workspaces
- Higher quality products or services
- Improved communication between teams and departments
- Standard work documentation
Toyota Production System
Kaizen was developed as a core element to the revolutionary Toyota Production System alongside Jidoka and just-in-time. The automobile manufacturer believed developing quality systems and continuously improving those systems would in turn improve the quality of their products.
What are the 5 elements of Kaizen?
Successfully practicing Kaizen comes down to cultivating a strong, supportive culture with the following five core elements:
- Teamwork: Staff work together to achieve the common goal of improved performances and processes. Teamwork is developed within departments, through quality circles, and between levels.
- Personal Discipline: Self-discipline when it comes to quality and time management is key to the success of Kaizen.
- Improved Morale: When people are empowered to improve their tasks or job, people are more satisfied with their job and the whole business process benefits.
- Quality Circles: Made up of approximately five to seven employees, quality circles allow teams to meet regularly to discuss issues arising in their work processes.
- Suggestions for Improvement: From human resources and accounting to manufacturing operations and the shipping department, every employee should be trained to identify wastes or improvements. All suggestions should be considered and employees should feel comfortable either sharing them or implementing them themselves.
Plan-Do-Check-Act
The PDCA Cycle is a four-step scientific approach to problem solving and continuous improvements. The four phases of PDCA are:
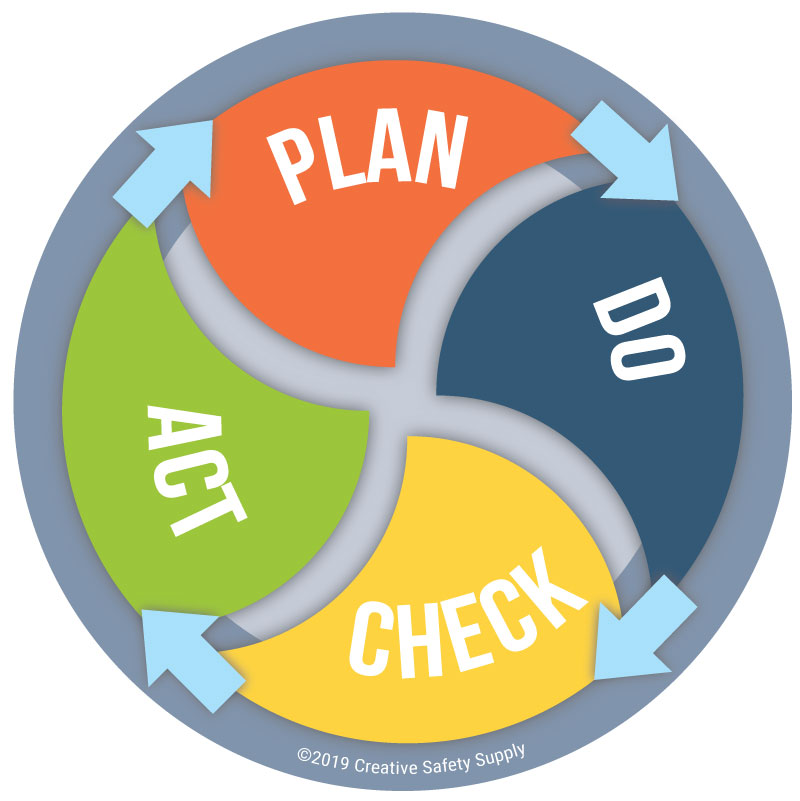
- Plan: An improvement opportunity is chosen, or an issue is identified. Goals are established to clarify the purpose of the project, stakeholders are considered, and an action plan is prepared.
- Do: The process is mapped out, data is collected, and the facts are analyzed to develop the best solutions. These changes are implemented on a small-scale capacity.
- Check: Solutions are tested and measured to check whether or not the improvements met the goals set in the planning phase.
- Act: If the changes didn’t pan out, the cycle is started over and a new solution is tested. If improvements were successful, the cycle restarts and the team begins planning wide-scale implementation.
PDCA should be repeated again and again as solutions are retested and refined to support continuous improvement.
The Continuous Improvement Philosophy
At the heart of Kaizen is the philosophy of continuous improvement – focusing on incremental improvements to achieve larger process improvements.
The philosophy of continuous improvement believes everything (staff, business processes, products, etc.) can be improved, and there is always room for improvement. When goals are met, the process isn’t over! Instead, new goals are set, and workers are constantly challenged. Continuous improvement should be seen as the responsibility of everyone in the organization and everyone should be looking for ways to improve.
Muda: The 8 Wastes of Lean
The starting point of an effective continuous improvement program is identifying waste. Kaizen aims to eliminate muda. Muda refers to the eight most common wastes in manufacturing: defects, overproduction, waiting, unused talent, transportation, inventory, motion, and extra-processing. Eliminating wastes keep production running smoothly and as each waste is reduced, quality is increased.
Standardized Work
Taiichi Ohno, the father of the Toyota Production System, has said “When there is no standard, there can be no Kaizen.”
Standardized work, the set of rules and procedures dictating how a task should be performed, provides a baseline for improvement processes. The three components of standard work are:
- Takt Time: The time it takes to manufacture a finished product in order to meet demand.
- Work Sequence: Step-by-step, the order of operations within a production process.
- Standard Inventory: The total number of materials, machines, and units needed to keep up with manufacturing.
Managers use this information to determine the most efficient methods for productivity, standardizing it across the board. Workers are encouraged to follow process steps as closely as possible – any variations can result in quality problems. or an increased cycle time. The foundation set by standard work allows improvements to be measured for effectiveness against it. Each time the standard improves, the new standard for work is set as the baseline and the improvement cycle starts all over again.
What is 5S?
5S is more than just the housekeeping strategy it’s often thought to be – it’s a strategy that promotes self-discipline and increases engagement. As part of Lean manufacturing and the Toyota Production System, the 5S framework for organization lays the groundwork for successful Kaizen implementation. Just like how standardized work establishes a baseline for continuous improvement, 5S creates an environment where continual improvement can thrive.
The 5S’s stand for:
- Sort out the clutter, keeping only what is necessary for the process.
- Set in Order the items remaining, placing tools in a logical manner and making everything easy to access.
- Shine the space, perform maintenance, and clean equipment.
- Standardize the efforts from the first three steps, making sorting, setting, and shining a part of routine.
- Sustain new practices, maintaining discipline through audits and continuing to improve 5S over time
5S drives continuous improvement by standardizing cleaning and maintenance procedures while instituting visual management. Through 5S, staff develop a sense of ownership and responsibility for their space. A sense of trust and respect is established for an environment where workers feel comfortable suggesting improvement ideas to the leadership team.
Kaizen Examples in Practice
Although Kaizen involves staff from all levels, creating a culture to sustain improvements will need to begin at the top and usually involves training:
- CEO and Executives: Executives need to understand how their role fits into developing a Kaizen culture.
- Managers and Supervisors: It’s key to provide managers and coaches with the context of Kaizen within in their teams – what to look for, keeping momentum up, etc.
- Frontline workers: Employees should understand why Kaizen is being implemented, and training should be focused on encouraging and empowering workers to perfect business processes on their own.
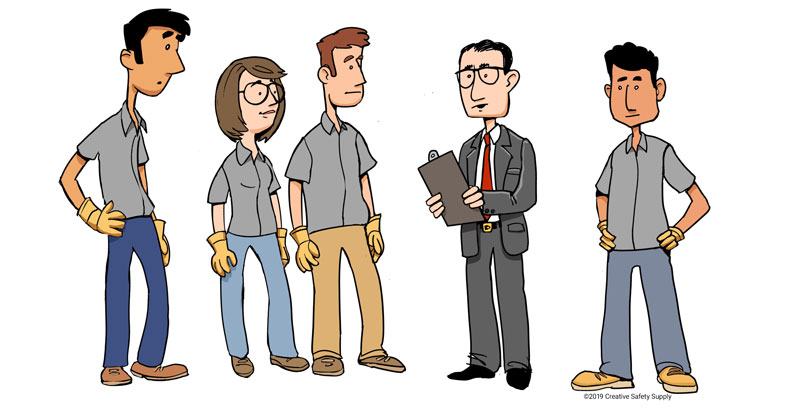
As a former Toyota executive describes, Lean and continuous improvement can be tough for executives to adopt. The former executive realized his workers had ideas he had never even thought of, and this practice encouraged collaboration and problem-solving.
Following initial implementation, managers and supervisors should be looking for types of ways to improve their own work, help maintain and improve standards, and support actions with evidence. The Kaizen toolbox is filled with improvement tools, but these tools are futile without a strong cultural shift.
Kaizen Event
So far, we’ve only discussed implementing the tenets of Kaizen as a daily practice. However, Kaizen can also benefit larger projects with a Kaizen event (also called a continual improvement blitz).
A Kaizen event is a scheduled short-term event where employees come together to focus on a particular issue or process. Organizations can also hold an event to improve or implement certain Lean tools like 5S, total productive maintenance, SMED, etc.
A typical Kaizen event will last anywhere from a few hours to a full week following this process:
- Prep: Define the scope of the event, choosing the target process. Select an event team, establish goals, and schedule a start/end date for the event. It’s also important to establish goals.
- Training: Ensure that everyone on the event team is given appropriate process improvement training.
- During the Event: Document the current state of the process by going to the Gemba and creating a value stream map. Conduct bottleneck analyses, root cause analyses, future value stream mapping, and implement a test solution.
- After: Follow up at a later date to measure results for effectiveness. Following the PDCA cycle, decide what the next steps are.
Process Mapping
No matter where your organization is in the process of implementing Kaizen, a process map will help get an accurate state of business processes. organization.
Before any changes are made or improvements implemented, a process map should be drafted to give others a detailed look at the current state of the process. This will help to quickly identify opportunities for improvement while establishing a baseline to measure any future changes against. To kick off a process mapping event, you’ll want to start by going to the Gemba.
Going to the Gemba
Gemba is a Japanese term referring to the actual place where the value is created or where work is performed. Gemba walks are a powerful tool to help the leadership team to meet the Kaizen objective of humanizing the workplace and respecting the people. It works to break down barriers while encouraging workers to feel comfortable sharing improvement suggestions.
Gemba walks typically have a theme and will usually focus on a specific process or waste. Management can support Kaizen in their organization by performing a Gemba walk to identify areas of improvement, evaluate standardization, and talk with employees.
Toyota Chairman Fujio Cho’s words, “Go see, ask why, show respect” encapsulates the best practices of Lean and Gemba. Managers must:
- Go to the Gemba to see not only how processes operate, but how they fit in with the broader purpose of the organization.
- Ask why things are being done – what is the root cause of the waste/issue?
- Show respect to workers creating value for the organization, they’re the experts in the process.
In the beginning of your continuous improvement journey, your achievements may seem small. But as time passes and employees become more engaged, organizations that adopted the Kaizen philosophy will likely see noticeable gains in the way processes operate. This is when business processes work better, customers are happier, and your business is more successful.
Additional Kaizen facts:
- Kaizen is a Japanese term meaning change for the better or continuous improvement. It is a business philosophy that concerns the processes that continuously improve operations and involve all employees. Source: https://www.investopedia.com/terms/k/kaizen.asp
- Kaizen was first practiced in Japanese businesses after World War II, influenced in part by American business and quality-management teachers, and most notably as part of The Toyota Way. It has since spread throughout the world and has been applied to environments outside of business and productivity. Source: https://en.wikipedia.org/wiki/Kaizen
- Kaizen is based on the PDCA (Plan-Do-Check-Act) cycles, which means that an organization first identifies areas for improvement, develops a plan to make changes, implements the changes, and then checks the results to see if further improvements can be made. This continuous cycle of improvement leads to a culture of innovation and progress. Source: https://www.lean.org/lexicon-terms/kaizen/
- Kaizen aims to reduce waste in terms of time, materials, and resources. By using the PDCA cycles, organizations can identify areas where resources are being wasted and take steps to reduce or eliminate this waste. The result is a more efficient organization that delivers high quality products/services at a lower cost. Source: https://business.adobe.com/blog/basics/what-is-kaizen
- Kaizen requires management commitment and employee involvement. The top management of the company has the most important role in implementing the Kaizen approach, and then every manager, and then it goes down to rank-and-file employees. When top management demonstrates its long-term commitment to continuous improvement, managers inevitably follow through on Kaizen initiatives and workers personally develop a Kaizen mindset. Source: https://safetyculture.com/topics/kaizen-continuous-improvement/