Zero Defects was first introduced by American businessman Philip Crosby in his "14 Step Quality Improvement Process". Since then, a number of manufacturing organizations have employed it to tackle and improve quality issues. Zero defects is referred to as a philosophy, a mentality, or a movement that aims to minimize the number of defects in manufactured products and service as much as possible. It doesn't have distinct steps to follow or rules to abide by, which leaves companies open to customizing how they want it to work for themselves.
This is perhaps why zero defects can be so effective, because it means it's adaptable to any situation, business, profession, or industry.
Principles of Zero Defects
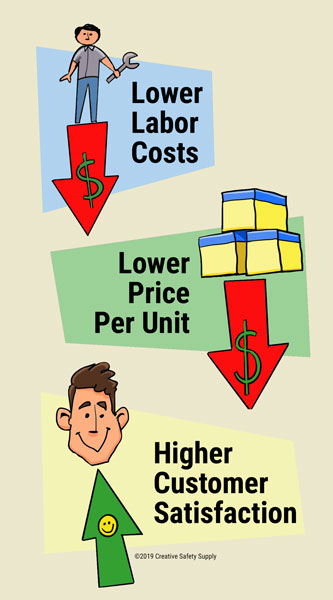
According to Philip Crosby, the principles of Zero Defects are as follows: Quality is defined as conformance to requirements – basically, every product or service has a requirement, a description of what the customer expects to see. Hence, a certain product is said to have achieved quality if and when it meets those requirements. However, this should not be confused with higher standards of products. For instance, it'll be unrealistic to say that a basic mobile phone is of low quality compared to the latest iPhone because they both have to meet different quality standards to pass the quality test. Based on this, Zero Defects means the basic mobile phone is a quality product if it meets the initial requirements set for it. That is, if it can make and take phone calls clearly, send and receive text messages, among other things, then it is only realistic to say it conforms to quality and has (close to) zero defects.
Defects Prevention Is Better than Quality Inspection and Correction – In a product quality management sense, it is preferable that defect prevention is made a part of manufacturing or company practice rather than quality inspection and correction. This is simply because Zero Defects management is almost always less troublesome, more certain, and less expensive, as it aims to prevent defects rather than to discover and correct them later on.
Quality Standards Means Zero Defects – The third principle of Zero Defects is based on the nature of requirements. If a requirement expresses what is genuinely needed by the customer or product itself, then any product or service unit that does not meet requirements will not satisfy the need and is nowhere near as good as expected. However, in some cases, some units that do not meet requirements could actually still satisfy the need, which means the requirement should be reviewed and changed to reflect reality.
Quality Is Measured in Terms of Money (i.e. The Price of Non-conformance (PONC) – Last but not least, Philip Crosby's principles of Zero Defects is based on the fact that Crosby believes that every defect represents a hidden cost, including: the costs of inspection time, reworking, and revenue. Furthermore, there's the cost of wasted material, labor, and customer dissatisfaction. When properly identified and brought to light, the effects of these costs can be made apparent. This will help provide a cost-justification for steps to improve quality. Businesses should find a way to measure Zero Defects management progress; this is essential to maintaining management commitment, rewarding employees, and ensuring company goals are made measurable so that actions can be made concrete and decisions can be made on the basis of relative return.
Similar Glossary Terms
- Cost of Quality
- Total Quality Management (TQM)
- TEAM Metrics
- DOWNTIME
- Cost of Poor Quality
- Quorum
- Quality Assurance (QA)
- CTQ Tree
- Quality Function Deployment