In just the United states alone, the third most common chronic condition is hearing loss. In fact, the CDC and NIOSH have estimated that 22 million employed U.S citizens are exposed to hazardous levels of noise every year. This not only affects the employee’s quality of life, but it also has the potential to come with hefty compensation costs from employers.
Occupational hearing loss, also known as OHL, occurs when people are exposed to 85 decibels or higher for long periods of time or from exposure to ototoxic chemicals such as solvents, asphyxiants, nitriles, and compounds. OHL can range anywhere from tinnitus to significant hearing loss at 50% or more.
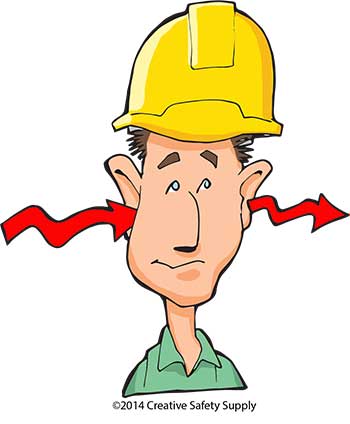
Unfortunately, this type of hearing damage can occur over the course of months or even years. For that reason, people don't notice it happening at first. To help combat this problem, OSHA has issued a number of requirements that employers must follow regarding hearing protection. Becoming familiar with OSHA's 29 CFR 1910.95 standard is not only important for remaining in compliance with government regulations, but also to ensure employees are given the protection they need.
Two Types of Hearing Hazards
There are two types of hearing risks associated with loud noise. The first is a sudden spike in loud noise—things like gunshots or explosions fall into this category. The other is prolonged noise exposure that is significantly louder than normal.
Sudden Bursts of Noise
Sudden bursts of noise can cause immediate hearing damage. In addition, due to the nature of this type of noise, people are often unable to prepare for it ahead of time, unless it is a planned event.
In the workplace, these types of sudden loud noises often come from machine presses that are used to shape metal or other objects. This type of extreme noise hazard can easily surpass 120 dB—the louder the noise is, the more damaging it will be. However, as with all noise pollution, proximity to the noise determines how loud it will be. Any facility that has machines or other objects that cause sudden loud noises will need to make sure there are signs nearby reminding employees of PPE requirements.
Prolonged Noise Exposure
Prolonged noise exposure is typically quite a bit lower in terms of decibels, but it is no less dangerous. Most manufacturing facilities have some amount of noise at all times, which means employees are often unable to find any relief from it. Even after just a couple minutes of enduring these “normal” sounds within a working environment, most people will become desensitized to the noise and barely even notice it.
Just because someone doesn't notice the noise does not mean they are not damaging their hearing. In fact, people who work in loud environments without sufficient hearing protection will likely experience permanent hearing loss, tinnitus, or other hearing-related problems that can affect them for the rest of their lives.
Overall, both loud bursts and prolonged noise exposure are dangerous, but what may be surprising to some is that the prolonged noise exposure can actually be more hazardous at lower levels compared to a burst of loud noise. Because of this, facilities need to identify all potential sources of noise, determine the hazard level, and then implement safety strategies to protect their employees.
How Loud Is Too Loud?
Hearing damage from noise exposure is based on how long the exposure lasts and how loud the noise actually is. OSHA has identified how long someone can be exposed to different levels of sound without hearing protection before it becomes unsafe.
However, while these are the limits stated by OSHA, most facilities will want to provide their employees with proper hearing protection at levels and durations significantly lower than those in this list just because it’s better to be safe than sorry. OSHA’s exposure limits include:
- 90 dB - Requires hearing protection if an employee is exposed for 8 or more hours.
- 92dB - Requires hearing protection if an employee is exposed for 6 or more hours.
- 95dB - Requires hearing protection if an employee is exposed for 4 or more hours.
- 97dB - Requires hearing protection if an employee is exposed for 3 or more hours.
- 100dB - Requires hearing protection if an employee is exposed for 2 or more hours.
- 102dB - Requires hearing protection if an employee is exposed for 1.5 or more hours.
- 105dB - Requires hearing protection if an employee is exposed for 1 or more hours.
- 110dB - Requires hearing protection if an employee is exposed for 30 minutes.
- 115dB - Noise at this volume is only safe for up to 15 minutes without protection.
Anything above 115 dB requires hearing protection, even if employees are only going to be exposed to it for a brief time. Having earplugs or other types of hearing protection available at the entrance to an area that has loud noises is an effective way to remind employees of the risk and to take proper precautions.
Eliminating and Mitigating Noise Exposure within a Facility
Before PPE for hearing protection is considered, the employer has the opportunity to take initiative in reducing noise within a facility with engineering and administrative controls. The following are only some of the many options for containing or eliminating noises within a facility via engineering controls:
- Noise Absorbing Panels - Installing these throughout the facility can dramatically reduce overall noise levels.
- Mufflers on Machines - Machines or vehicles that have gas engines can be very loud. Having a muffler installed can reduce OHL risk.
- Modernizing Machines - In many cases, newer machines run much quieter than older ones. Consider replacing machines or updating them to reduce noise.
- Containment - Moving particularly loud equipment into a soundproof room can help reduce noise in the rest of the facility. In many cases, these machines can even be operated by someone outside of the room.
Administrative controls for noise mitigation are also an option, some include:
- Limiting the time an employee is exposed to noisy equipment
- Using noisy equipment when less people are around
- Providing rooms that are noise free to give employees a break
- Ensuring employees are well away from noisy equipment if they are not using it
Options for Hearing Protection
Once noise control measures have been taken, the employer can then think about establishing required hearing protection for employees. There are a few options for hearing protection such as earplugs, earmuffs, or even both at once, but every situation has a mode of protection that works best.
Earmuffs
Earmuffs are designed to fit over or around the head and then cover the entire ear rather than just going into the ear canal. A properly fitting pair of earmuffs can provide a tremendous amount of protection since they stop the sound from entering the ear at all.
Some types of highly advanced earmuffs are actually built with a microphone on the outside and small speakers on the inside. These earmuffs can "listen" to the environment and replay sounds at a safe volume to the person wearing them, eliminating much of the noise during that process. This makes it possible for people to talk freely in loud environments, without being at risk of hearing loss.
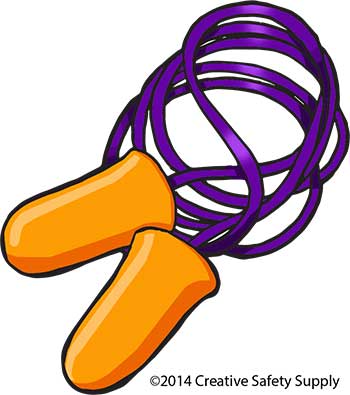
Earplugs
Earplugs are one of the oldest forms of hearing protection, but they are still very effective. Earplugs are sufficient for environments with low levels of dB where hearing protection is required.
This type of hearing protection is extremely inexpensive and is disposable in most cases. Employers can put out large containers of them for the employees to wear when entering loud environments, and then employees can discard them when leaving. This is one of the easiest and most affordable ways to remain in compliance with OSHA’s hearing protection requirements.
Understanding Noise Reduction Rating
The noise reduction rating, or NRR, works to measure the efficiency of earmuffs and earplugs. Currently, the highest noise reduction rating that can be found is for earplugs, and that’s at 33 decibels. Earplugs are able to have a higher NRR because they are in direct contact with the ear, whereas earmuffs can reach up to a rating of 30-31.
Now, the NRR number doesn’t directly correlate with a reduction of dB. In fact, the user will have to do a bit of math to figure out how much protection is provided. To determine the actual rate of protection, the user has to take the NRR and subtract seven, then divide that number by two. Once that is done, they must then take the dB level in the environment that they are in and subtract the new NRR number from that. For example, the equation would look something like this:
(31-7) /2=12. 100-12=88dB
88 dB is much safer than 100 dB, especially with earmuffs or earplugs protecting the wearer’s hearing. However, there is a trick if the user needs even more protection that earmuffs or earplugs cannot provide by using just one of them, and that is to wear both! The NRR calculated in this situation requires the user to add five to the higher NRR rating. So, say they have earmuffs rated at 30 and earplugs rated at 33, the equation would look like this:
33+5=37
(37-7) /2= 15. 100-15=85dB
The user must keep in mind the dB level that they will be exposed to when choose the right hearing protection equipment. If the wrong equipment is chosen, they will not escape the potential for hearing loss down the road.
OSHA Requirements for Hearing Protection
OSHA’s hearing protection requirements boil down to implementing a hearing conservation program for employees that enables the correct PPE to be obtained, monitoring of the noise levels within the building where employees work, as well as monitoring potential hearing loss in employees via audiometric testing. OSHA also makes it clear that employees need to know all the risks associated with a given job, including risks associated with noise pollution.
By informing employees of the necessary hazards and training them on proper use of hearing protection, the company will be well on its way with complying with OSHA regulations.
Employee Fit Testing
Employee fit testing for hearing protection is much more complicated than say a respirator fit test in that it’s entirely up to the user to correctly apply the earplugs or earmuffs. To combat this, employees are instructed on how to properly insert earplugs or use earmuffs and then checked with what is called a personal attenuation rating. This is done mostly with audiometric testing for the user.
However, what is found at the time of the test is not necessarily what the level of protection will be as the employee goes about their day adjusting and readjusting their hearing protection. It comes down to reminding and instructing employees of the proper use of hearing protection—without it, there is no guarantee that they will be completely safe.
What is a Hearing Conservation Program?
Implementing OSHA’s hearing conservation program is a requirement within any business that has any sort of noise pollution within their facility. The conservation program includes:
- Monitoring noise levels
- Audiometric testing for individuals
- Hearing protection
- Training
- Recordkeeping requirements
Overall, hearing protection is absolutely necessary to ensure that employees retain their health. Loss of one’s hearing has been attributed to an increase in the possibility of cognitive function decline, mental health issues, and chronic pain associated with an increase in stress.
Similar Articles
- What is a Noise Reduction Rating? [ANSI S3.19 Explained]
- OSHA Respiratory Protection Standard (29 CFR 1910.134)
- What is HAZCOM? (Hazard Communication Definition + OSHA Standards)
- Fall Protection in the Workplace: OSHA’s Guidelines
- OSHA’s Guidelines to Protecting Employees from Coronavirus
- NFPA 25: Standards for Fire Protection Systems
- Understanding OSHA/ANSI First Aid Kit Requirements
- OSHA Construction Safety
- OSHA Safety Sign Requirements [1910.145]