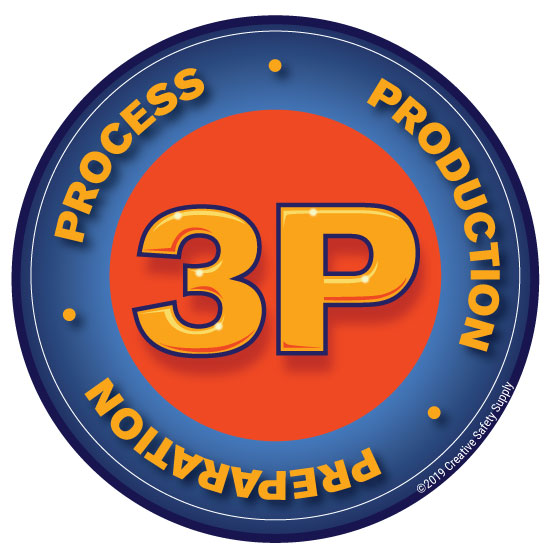
While most Lean principles focus on improving existing processes, Production Preparation Process (3P) is a bit more proactive.
Most Lean methods are designed to improve previously-established processes, with the end goal of producing more efficiently and eliminating waste. Rather than improving the processes already in place, 3P eliminates waste through product and process design.
It’s one of the most powerful manufacturing tools, and is best implemented in organizations that have previous experiences with Lean manufacturing methods like Kaizen or 5S. The concurrent development required in 3P allows the product design to influence its manufacturing process and vice versa, which inevitably generates new insights on how to improve the product or how to streamline its production. These insights are also easier to implement under 3P, as they emerge during the design phase and not the production phase, where reworking a process to be more efficient may cost significant amounts of money and require shutting down production processes altogether.
Creatively, 3P starts from a blank slate in order to think about customer requirements a brand new, fresh way. Best of all, 3P elicits input on process and product design from a wide range of disciplines. Workers and supervisors, engineers and stakeholders; during the design process, all of these groups are informed, involved, and ready to offer helpful feedback. Not only does this create a holistic sense of responsibility for the process and product in question, but it also elicits a variety of new ideas on how to reduce waste. 3P requires small teams of workers from different backgrounds—management, production, safety, etc.—to work together to create several alternative ways of manufacturing and designing products to meet customer needs.
Originally, the 3P methodology grew out of the Shingijustsu company’s analysis of Toyota’s product and process development system. Since then, it has been used by many Lean-savvy corporations to push their manufacturing processes and product design to the next level. Like a Kaizen blitz or 5S event, 3P should be implemented in a designated window of time, usually a week.
Actions that occur during 3P:
- Revising product designs
- Utilizing different process designs
The benefits from 3P are often dramatic, extreme, and immediate. They include the following:
- Less complex products
- Simpler manufacturing processes
- Produces products that are easier to use/maintain
- Eliminates unnecessary steps
- Utilizes smaller, more cost-effective equipment that better meet production needs
In a nutshell, 3P acts as the catalyst for a jump in design/production improvements. These methods allow workers, managers, and engineers to work in teams to make drastic changes in production and waste elimination. When approached with the 3P methods, production can be greatly improved.
Additional 3P facts:
- 3P is an acronym for Production Preparation Process, which is a method that focuses on eliminating waste through product and process design. It was introduced to the US in the mid-1980’s by Chihiro Nakao, founder of the consulting firm Shingijutsu, and a contemporary of Taiichi Ohno. Source: https://www.leansixsigmadefinition.com/glossary/3p/
- 3P is defined as an event-driven process for simultaneously developing new products and the standards and workflows that support them in an effort to take product design and production to the next level. 3P’s concurrent development process allows the product design to dictate the processes that will be used to produce it, which provides an opportunity to start gathering insights for improving products/processes from the get-go. Source: https://www.gembaacademy.com/resources/gemba-glossary/3p-production-preparation-process
- 3P is one of the most powerful Lean tools available, with the potential to unlock innovation, rapid learning, and improved collaboration. 3P occupies a unique role in Lean, as it essentially eliminates waste by heading back to the drawing board and starting from scratch. Source: https://www.velaction.com/3p-production-preparation-process/
- 3P is an advanced technique that makes use of many of the basic Lean tools and other methods, such as value stream mapping, brainstorming, prototyping, and experimentation. 3P can be applied to either a product design or a process design, depending on the problem to be solved. Source: https://safetyculture.com/topics/3p/
- 3P consists of several phases, such as defining the problem, setting goals and objectives, analyzing and diagramming the current state, generating and evaluating alternatives, selecting and testing the best solution, and implementing and standardizing the new design. Source: https://www.leansixsigmadefinition.com/glossary/3p/