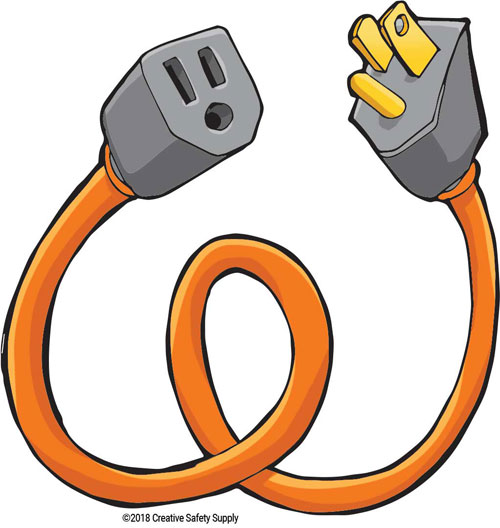
Poka yoke is a Japanese term that means “mistake-proofing” or “error prevention”. It is a concept and a set of techniques that aim to eliminate defects and errors in any process by preventing, correcting, or drawing attention to human mistakes as they occur
Poka yoke was developed by Shigeo Shingo, an industrial engineer and a pioneer of the Toyota Production System, in the 1960s. He observed that human errors were inevitable, but defects could be avoided if the process was designed to detect and correct them immediately. He also distinguished between errors (unintentional actions) and defects (nonconformities that reach the customer)
Poka yoke is based on the principle that “quality should be built into the process”. It is not enough to rely on inspection or testing to ensure quality; instead, the process should be error-proofed so that defects cannot occur in the first place. Poka yoke is also a proactive approach that seeks to prevent problems before they happen, rather than reacting to them after they occur
Poka yoke can be applied to any process, whether it is manufacturing, service, or administrative. It can also be implemented at any stage of the process, from design to delivery. Poka yoke can be used to prevent errors from happening, to detect errors when they happen, or to mitigate the consequences of errors
Types of Poka Yoke
There are two main types of poka yoke: control and warning
- Control poka yoke: This type of poka yoke prevents errors from occurring by making it physically or logically impossible to make a mistake. For example, a connector with a unique shape can only be plugged in the correct way, or a sensor can stop a machine from operating if an item is misaligned. Control poka yoke is more effective and reliable than warning poka yoke, as it does not depend on human attention or intervention.
- Warning poka yoke: This type of poka yoke alerts the operator or the user of a potential error before or after it occurs, by using sounds, colors, lights, or messages. For example, a car can beep if the driver forgets to fasten the seatbelt, or a software program can display a confirmation message before deleting a file. Warning poka yoke is less effective and reliable than control poka yoke, as it can be ignored, misunderstood, or overridden by the operator or the user.
Benefits of Poka Yoke
Poka yoke can provide many benefits to organizations that implement it, such as:
- Improving quality: By reducing or eliminating defects and errors, poka yoke can improve the quality of products and services, and increase customer satisfaction and loyalty.
- Reducing costs: By preventing defects and errors, poka yoke can reduce the costs associated with rework, scrap, waste, inspection, testing, warranty, and customer complaints.
- Increasing efficiency: By simplifying and standardizing the process, poka yoke can increase the efficiency and productivity of the operators and the users, and reduce the cycle time and the downtime.
- Enhancing safety: By avoiding accidents and injuries, poka yoke can enhance the safety and well-being of the operators and the users, and comply with the regulatory and legal requirements.
- Fostering improvement: By providing feedback and learning opportunities, poka yoke can foster a culture of continuous improvement and innovation, and empower the operators and the users to solve problems and prevent them from recurring.
How do you conduct Poka Yoke?
Poka Yoke involves implementing physical or informational changes to a process that prevent mistakes from happening in the first place. There are two main approaches: control and warning. Control methods make it physically impossible to make an error, like a power tool that won't turn on unless a safety feature is engaged. Warning methods, on the other hand, alert the worker to a potential error before it occurs. An example might be a computer program that won't let you save a file unless all required fields are filled in. By following a structured process that identifies potential error points and then applies the most appropriate poka-yoke method, organizations can significantly reduce defects and improve overall process quality.
Poka-yoke tackles human error in a two-pronged approach: prevention and detection. Ideally, poka-yoke systems are designed to prevent errors from happening altogether. This can be achieved through physical mechanisms or design features. For instance, a power tool might require two hands on the grips before it activates, preventing accidental use.
However, unexpected situations or unforeseen mistakes can still occur. This is where the detection aspect of poka-yoke comes in. These systems flag potential errors as they're happening, giving the worker a chance to correct them before they snowball into bigger issues. Imagine a computer program that highlights missing information in a form before it allows submission, prompting the user to double-check their entries.
By proactively preventing and detecting errors, poka-yoke minimizes the impact of human fallibility, leading to a more reliable and consistent process.
How does poka-yoke respond to human error?
Poka-yoke, also known as mistake-proofing, relies on a set of core principles to achieve its goal of error reduction. These principles can be broadly categorized into two main approaches: elimination and detection. Elimination focuses on completely removing the possibility of mistakes by redesigning the process or product. This could involve things like using parts with unique shapes that only fit together one way or implementing automated checks that prevent a machine from operating unless specific conditions are met.
When eliminating errors isn't feasible, detection comes into play. Detection methods aim to identify mistakes as soon as possible, allowing for quick correction and minimizing the potential for rework or scrap. This might involve installing sensors to detect missing components or incorporating visual cues like colored lights to alert workers to potential issues. By following these principles and creatively applying them to specific situations, poka-yoke helps organizations build robust and error-resistant processes, ultimately leading to higher quality and efficiency.
Examples of Poka Yoke
Poka yoke can be found in many aspects of our daily life, as well as in various industries and sectors. Here are some examples of poka yoke:
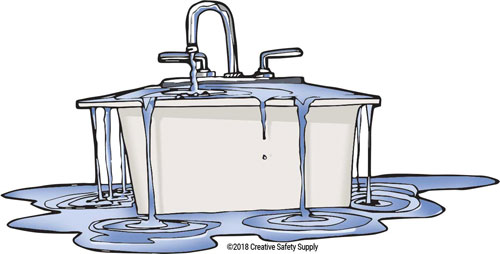
Examples of poka yoke in everyday life are:
- The microwave oven stops running when the door is opened, preventing exposure to microwave radiation.
- The gas pump nozzle has a different size and shape for different types of fuel, preventing the wrong fuel from being used.
- The USB plug can only be inserted in one way, preventing damage to the device and the port.
- The car key can only be removed when the gear is in park, preventing the car from rolling away.
- The spell check function on most writing programs can highlight and correct spelling errors, preventing typos and grammatical mistakes.
Examples of poka yoke in manufacturing are:
- A fixture that holds the parts in a specific position and orientation, preventing misalignment and incorrect assembly.
- A counter that tracks the number of parts or operations, preventing missing or extra components or steps.
- A barcode scanner that verifies the identity and quantity of the parts, preventing mix-ups and errors in inventory and shipping.
- A light curtain that stops the machine if a hand or an object is detected in the danger zone, preventing injuries and damage.
- A checklist that ensures all the required tasks and checks are completed, preventing oversights and omissions.
Examples of poka yoke in service are:
- A ticket dispenser that issues a numbered ticket to the customer, preventing confusion and disputes in the queue.
- A timer that reminds the service provider of the time limit for each service, preventing delays and inefficiencies.
- A survey that asks the customer to rate the service and provide feedback, preventing dissatisfaction and complaints.
- A password generator that creates a strong and secure password for the user, preventing hacking and identity theft.
- A confirmation email that summarizes the details and terms of the service, preventing misunderstandings and errors.
Principles of Mistake-proofing/Poka-Yoke
Poka-yoke, also known as mistake-proofing, tackles errors through a hierarchical approach with two main principles: elimination and detection. The ideal scenario lies in elimination, where mistakes are engineered out entirely. This can involve redesigning processes or products to prevent errors from physically occurring. For instance, a power tool that requires two-handed activation or a puzzle piece with a unique shape that only fits one way. By eliminating the possibility of mistakes upfront, poka-yoke prevents defects and rework from the get-go.
However, some errors are unavoidable. This is where detection comes in. Detection methods aim to catch mistakes as early as possible, allowing for quick intervention and minimizing the impact. This might involve installing sensors to detect missing components on an assembly line or using color-coded lights to visually alert workers to potential problems. By implementing these principles creatively, poka-yoke builds a safety net within processes, fostering a more reliable and consistent operation that ultimately leads to higher quality and efficiency.
Related Concepts
Poka yoke is closely related to other concepts and tools that are used to improve quality and prevent defects, such as:
- Kaizen: Kaizen is a Japanese term that means “continuous improvement”. It is a philosophy and a practice that involves everyone in the organization in identifying and solving problems, and making small and incremental changes to improve the process and the product.
- Six Sigma: Six Sigma is a methodology and a set of tools that aim to reduce variation and defects in a process, and achieve a high level of quality and customer satisfaction. It is based on the DMAIC cycle (Define, Measure, Analyze, Improve, Control), and uses statistical techniques to measure and improve the process performance.
- Lean: Lean is a philosophy and a set of principles that aim to eliminate waste and optimize value in a process, and achieve a high level of efficiency and productivity. It is based on the concepts of value stream mapping, pull system, flow, just-in-time, and 5S (Sort, Set in order, Shine, Standardize, Sustain).
- 5 Whys: 5 Whys is a technique that helps to identify the root cause of a problem by asking “why” five times, or until the underlying cause is revealed. It is a simple and effective way to solve problems and prevent them from recurring.
Poka yoke is a powerful and practical concept that can help any organization to improve its quality and prevent defects and errors. By applying poka yoke techniques, organizations can achieve the following benefits:
- Improve quality and customer satisfaction
- Reduce costs and waste
- Increase efficiency and productivity
- Enhance safety and well-being
- Foster improvement and innovation
Poka yoke can be applied to any process, whether it is manufacturing, service, or administrative. It can also be implemented at any stage of the process, from design to delivery. Poka yoke can be used to prevent errors from happening, to detect errors when they happen, or to mitigate the consequences of errors.
Poka yoke is closely related to other concepts and tools that are used to improve quality and prevent defects, such as kaizen, six sigma, lean, and 5 whys. By integrating poka yoke with these approaches, organizations can achieve a higher level of performance and excellence.
Additional Poka Yoke facts:
- Poka yoke is a Japanese term that means “mistake-proofing” or “error prevention”. It is a process improvement technique that significantly reduces the number of defects produced by preventing, correcting, or drawing attention to human errors as they occur. Source: https://en.wikipedia.org/wiki/Poka-yoke
- Poka yoke was developed by Shigeo Shingo in the 1960s as part of the Toyota Production System. He redesigned a process in which factory workers would often forget to insert a required spring under one of the switch buttons. He used a placeholder to help the workers remember to insert the spring and avoid the mistake. Source: https://en.wikipedia.org/wiki/Poka-yoke
- Poka yoke can be applied to any process that involves human interaction, such as manufacturing, service, or office work. Poka yoke can be classified into three types: contact methods, fixed-value methods, and motion-step methods. Contact methods detect physical attributes such as shape, size, or color. Fixed-value methods ensure that a certain number of actions or steps are performed. Motion-step methods signal the completion or non-completion of a step. Source: https://www.lucidchart.com/blog/poka-yoke-in-lean-manufacturing
- Poka yoke can benefit businesses by improving quality, reducing costs, increasing customer satisfaction, and enhancing safety. Poka yoke can also empower workers by giving them feedback, autonomy, and responsibility. Source: https://www.indeed.com/career-advice/career-development/poka-yoke-meaning
- Poka yoke can be implemented using simple and inexpensive devices, such as sensors, checklists, alarms, or color-coding. Poka yoke can also be integrated with digital tools, such as software, apps, or online platforms. Source: https://safetyculture.com/topics/poka-yoke/
Similar Glossary Terms
- Jidoka
- Andon Lights
- Toyota Production System
- Understanding Lean Manufacturing Terms
- SMED
- Lean Manufacturing Tools
- 3P
- Quality Assurance (QA)
- Katalab