It’s widely known that mining is a risky occupation. Due to explosions or cave-ins that may kill dozens of workers at once, and the large population of miners who have contracted illnesses due to coal dust and other respiratory exposures, the dangers of being a miner are highly publicized.
Two major factors lend to mining’s high level of risk. First, by nature the mine itself constantly changes. The shape and size of tunnels fluctuate, structural integrity is regularly updated, and devices such as electrical equipment need to be moved. This shifting workplace makes it difficult to communicate changes, which means miners may be working near live electricity or are in the new path of a vehicle without knowing it.
Second, there are a wide variety of dangers within this ever-changing environment; miners not only have to protect themselves from respiratory illnesses and be aware of potential cave-ins, they’re also surrounded by a wider variety of hazards than people typically face in the workplace.
Hazards that commonly compromise mining safety include:

- Noise. Miners use loud equipment, such as front end loaders, drills, bulldozers, and roof bolters. Since they work in tight spaces, the physical impact of this on hearing can be amplified. Miners have suffered from permanent hearing loss due to not wearing or not being provided the proper hearing protection. Preventing this irreversible damage is a major concern in many mines.
- Fires. There are a number of factors that may cause a fire in a mine, from equipment that could create sparks when it comes into contact with rock or an accidental release of gases into the air. For example, if shafts are not sealed or vented properly, a methane ignition could occur. Unfortunately, traditional fire suppression systems may not be suitable for certain mines. Between this and the fact that workers may be unable to escape if a fire breaks out, fire safety is especially important in mining health and safety programs.
- Electrical hazards. Electricity is essential in mining, as it allows workers to be able to see and operate machinery. However, this means that several pieces of electrical equipment are used throughout the mine. These pose a risk of arc flash, shock, and fire. Electrical safety training is important for miners, especially if the equipment is dangerous or has recently been extended to a new area.
- Vehicle hazards. Industrial vehicles are often used at mining sites, both inside and out. Tractors, cranes, cement trucks, excavators, and man lift baskets are common outdoors, while shuttle cars operate in the tunnels. Operators typically have poor visibility and communication is essential for both the intentions of the operators and any workers who may be doing their job around these vehicles. In fact, a high number of miner fatalities occur through vehicle accidents. Careful traffic plans, extensive training, and high visibility clothing such as safety vests are essential steps to preventing accidents.
- Explosions. Flammable gases and chemicals often flow through pipes and the air in underground mines. The two most common explosions that occur come from methane and coal dust. Methane gas is a byproduct of coal, and if either this or the dust comes into contact with a heat source, this may lead to an explosion. This is a serious threat to miners’ safety and the common culprit when multiple workers are injured or killed in a single event. Ventilation systems need to be regularly maintained and checked, and warning signs should be posted to remind workers of safe practices.
- Collapses, rock falls, and cave-ins. The natural infrastructure of mines may sometimes lead to disaster. Both the roof and walls are vulnerable to collapse, and rocks and other debris may become unstable and fall, striking workers. Sometimes miners are also seriously injured if they become trapped between the rock wall and vehicles, machinery, or automatic doors. Safety training should be in place and workers should have a plan of action if a cave-in or rock fall ever occurs.
- Dust exposure. Miners are at risk for breathing in debris and dust as they work, and over time, the consequences of this can be serious. The most well-known example is black lung disease, which is caused by coal dust and still impacts miners today.
Keys to Ensuring Mining Safety
Although there are a variety of hazards present in mining, there are steps that both employers and workers can take to reduce the risk of these hazards and protect themselves. The following are effective prevention methods: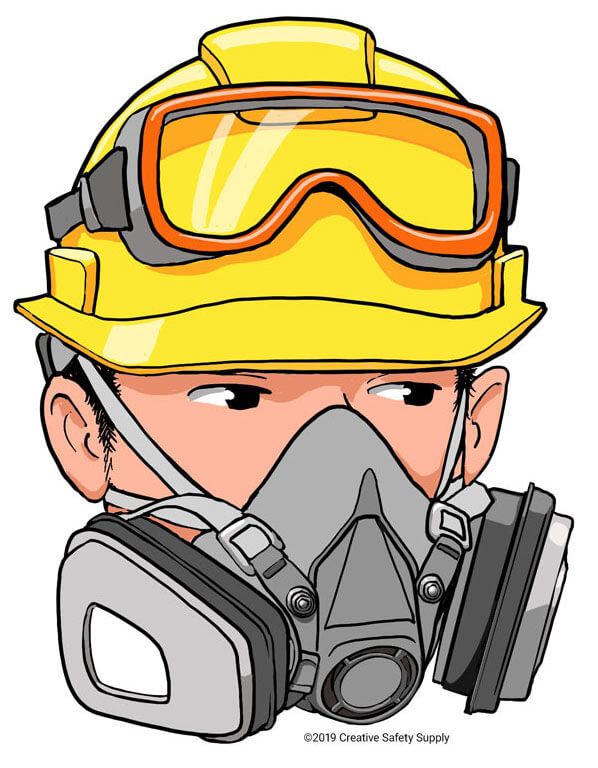
- Hazard communication and visual management. In the shifting environment of a mine, it is essential that workers are aware of hazards and potential dangers at all times. Communication throughout the workplace should be strong and standardized. Visual management of communication includes safety labels, highlighted emergency exits, reflective clothing and signs, and glow-in-the-dark signs. These mining safety supplies are easily available and compliant with federal and local regulations. Using them will inform workers of hazards, guide them to safe areas, and warn about proper safety precautions.
- Personal protective equipment. Having the correct mining safety PPE can reduce injuries and fatalities in mines. This equipment includes hard hats, hearing protection, gloves, steel-toed boots, personal fall protection, visible safety apparel such as reflective vests, safety glasses, and masks. Depending on the environment within the mine or the material that is being mined, a powered air-purifying respirator may be required.
- Preparation for emergencies. Having a detailed emergency response plan can make all the difference in the case of fires, explosions, and poisonous gas events.Miners should receive training in rapid response and know how to get to the nearest exit.Many mines also install emergency chambers stocked with gas masks, air, food, and water. If workers can reach these rooms and close the doors, they can protect themselves from carbon monoxide and other poisonous gases or from a cave-in, and survive until mine rescue workers are able to reach them.
- Strengthening infrastructure to prevent cave-ins. Besides explosions and fires, a major concern among mining operations is a cave-in. Even small events may leave workers with no food or water and limited oxygen for hours at a time. To reduce this risk, companies need to take precautions and practice proper ground control. Ground control includes designing support pillars, reinforcing roof support, and reinforcing the side walls of tunnels through horizontal stress support.
- Extensive training, especially on special equipment such as vehicles, and compliance to established health and safety standards. If a worker handles electrical equipment or operates vehicles, specialized training is required. For example, they should understand lockout-tagout practices and wear electrical gloves. Vehicle operators often are fatally injured due to not wearing a seatbelt. Safety regulations for mines have been established by a governing body, MSHA, and these are the guidelines that employers may use to implement health and safety in their workplace.
The Mine Safety and Health Administration (MSHA)
The Mine Safety and Health Administration is currently the governing body that oversees the safety of mines in the United States. Similar to OSHA, it is an agency of this country’s Department of Labor. Its mission is to prevent injury, illness, and death from mining, and supports healthful and safe workplaces for miners.
The agency develops and implements rules concerning health and safety for all mines in the U.S. regardless of the material that’s mined, the method of extraction, number of employees, or physical size. It also provides assistance to operators and employers, such as programs and information on education, training, and technical operations within mines. MSHA cooperates with other state and federal agencies such as OSHA to improve health and safety conditions.
MSHA is goverened by the Federal Mine Safety and Health Act of 1977 (which is also known as the Mine Act). This act expanded on 1969’s Federal Coal Mine Health and Safety Act, which mandated consistent inspections of coal mines and required that financial penalties be enforced if violations were found. This landmark safety law protecting miners was established after the 1968 Farmington coal mine explosion in Virginia, which killed 78 miners.
The 1977 Federal Mine Safety and Health Act not only created MSHA, it also expanded and strengthened miners’ rights and established mine rescue teams. The impact of the creation of both the agency and this law have significantly improved mining safety and prevented hundreds of deaths. In 1978, 242 miners died while on the job; in 2018, this number was just 28. Every year, the number of mining fatalities is kept in the low double digits. Currently, MSHA continues to reduce death, illnesses, and injury through substantial enforcement as well as training, education, technical support, and outreach to the mining industry.
Both the Federal Mine Safety and Health Act and MSHA regulations require that mining operators provide their employees with:
- The required amount of safety training
- Proper personal protective equipment
- Proper dust collection, ventilation, and air purification, as well as regular samples taken to test compliance for respirable dust and to inspect air quality
- Adequate and accurate signage, which warns of dangerous work environments and potential liquids, obstacles, gases, or hazards
- Consistent equipment inspection and replacement/repair of damaged or malfunctioning parts
- Records of mine conditions that are updated daily
- Accurate maps of the mine, a copy of which is given to each miner and to rescue crews
- Safe and operational electrical power and electrical-powered items that are kept in good condition. These should also be deenergized to reduce the potential of arc flash
- Sufficient firefighting equipment and proper training on using it
- Communication devices such as radios or phones that are kept in good working order
- An understanding that employees should be able to express concerns or complaints to MSHA without fear of punishment or termination
It is required that each surface mine is inspected by MSHA twice each year, and each underground mine inspected four times, for health and safety compliance. Mines that have high levels of toxic or explosive glasses are inspected more, and inspections are also conducted when complaints of non-compliance or hazardous conditions have been reported. MSHA offers resources on mining safety compliance as well as a breakdown of the conduction of their inspections to aid mines in remaining compliant.
Enhancing and Ensuring Mining Safety
Miners face a wide variety of hazards in their work environment. From coal dust explosions to an ever-changing environment, there are a multitude of events that may occur and a lot of potential for accidents. By providing proper training and personal protective equipment, using visual communication, and adhering to MSHA standards, employers can help make sure that their workers are as safe as possible in the mines.
Similar Articles
- Occupational Safety and Health Administration
- Quality, Health, Safety, Environment (QHSE) Management Systems
- Arc Flash and Electrical Safety
- Fire Safety in the Workplace
- 10 Essential Steps for Electrical Safety
- OSHA Construction Safety
- Improving Workplace Electrical Safety
- Forklift Safety Procedures
- OSHA Compliance: What You Need to Know