Several OSHA standards require employers to conduct a hazard assessment and identify hazards which their workers may be exposed to. In the event of community spread of a respiratory illness, it is especially important to evaluate whether workers are at risk of contracting this illness while on the job. The majority of workers will generally have a low exposure risk, with the exception of industries such as healthcare, death care, laboratories, retail settings, and airline operations or other types of international travel. Depending on the level of risk, new work policies and hazard controls must be implemented.
Employers should consider whether their workers may encounter a person or a surface that has been infected. They should also determine whether their workers are exposed to environments or materials that could be contaminated, such as waste management settings or laboratory samples. OSHA has developed guidance for businesses and employers to plan for and respond to workplace exposures to respiratory illnesses. Lack of planning can lead to workers who are inadequately trained and a failure to reduce exposure.
OSHA’s guidance is based on industrial hygiene practices and traditional infection prevention measures, with a focus on the need to implement administrative and engineering controls as well as personal protective equipment (PPE). Employers and workers can use this advisory guidance to plan for outbreaks, identify their risk levels in the workplace setting, and determine control measures so workers are not infected by illness as much as possible.
Applicable OSHA Standards to Preventing Exposure
There are five main OSHA standards that employers should adhere to when preventing worker exposure to illness. These are:
- PPE Standards 29 CFR 1910.132-1910.138. Personal protective equipment that is effective in preventing exposure may include eye and face protection, gloves, and respiratory protection. These OSHA standards provide guidelines on the use, maintenance, and disposal of PPE.
- The Respiratory Protection Standard. When respirators are needed to protect workers from exposure, employers must implement a respiratory protection program that adheres to standard 29 CFR 1910.134, Respiratory Protection.
- The Bloodborne Pathogens Standard. OSHA’s 1910.1030 standard applies whenever there is occupational exposure to materials such as human blood that are potentially infectious and do not involve respiratory secretions. If workers are exposed to human blood or other body fluids in your workplace, they must be trained in accordance with the Blood Pathogens standard to help control certain sources of viruses.
- Hazard Communication Standard, 29 CFR 1910.1200. Some common sterilizers and sanitizers that are used for disinfection and cleaning contain hazardous chemicals. Employers are required to protect their workers from exposure to these hazardous chemicals, and must use proper labeling and communication of these hazards as according to OSHA’s HazCom standard.
- The General Duty Clause, which requires employers to provide each worker with “employment and a place of employment which are free from recognized hazards that are causing or likely to cause death or serious physical harm.”
On top of these main standards, there are also 28 State Plans that have been approved by OSHA for specific state occupational safety and health programs. These plans have potentially more stringent requirements and are as effective as OSHA’s federal standards. Check with your state plan for more information.
Classifying Worker Exposure
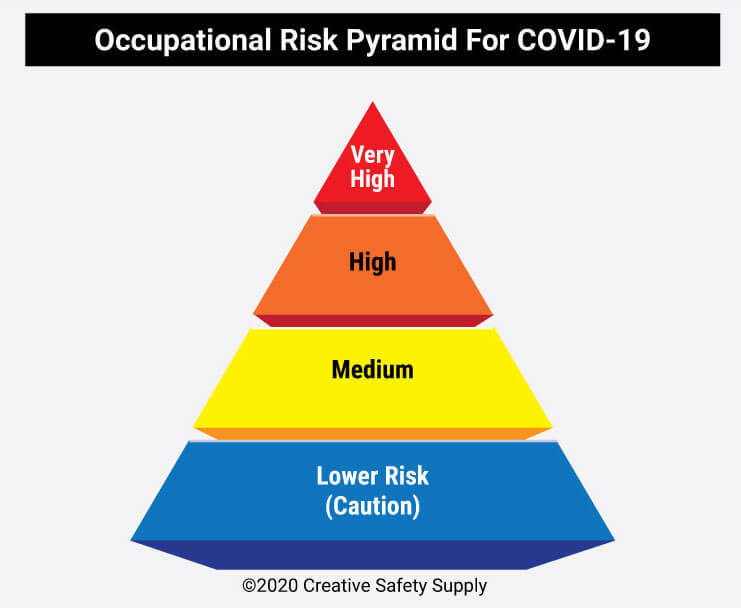
In the case of respiratory illness and other diseases, employers must determine their workers’ risk of exposure. Risk of occupational exposure to illness varies from lower, medium, and high to very high. OSHA’s Occupational Risk Pyramid indicates these four exposure risk levels:
Risk depends on industry type, the need for contact with coworkers or visitors who are known or suspected to be ill, and nature of operations. Most of the workers in America typically fall into the lower level of exposure risk, where they do not maintain frequent close contact with other people or with each other. Other workers, however, will fall into higher levels of risk. For example, workers in retail settings, schools, and international travel will have a medium exposure risk. People who work in healthcare, morgues, and medical transport will be in the high or very high risk level.
Once the level of risk has been determined, employers may then select and implement control measures to prevent exposure. Regardless of level of risk, there are certain steps that all employers can take to reduce their workers’ exposure. These steps include:
- Creating an infectious disease preparedness and response plan. This work-specific plan should include recommendations from local, state, and federal health agencies such as the need for social distancing, delivering services remotely, using a reduced workforce, and other measures of reducing exposure. The plan should consider where, how, and to what sources workers might be exposed, as well as workers’ individual risk factors (those of older age, or who have medical conditions).
- Implementing basic infection prevention measures. In most cases, protecting workers depends on good hygiene and infection control practices. These include promoting hand washing, providing alcohol-based sanitizers, encouraging workers to stay home if they are sick, and encouraging respiratory etiquette such as covering coughs. Employers should determine whether they can establish policies such as flexible work hours or telecommuting. On the worksite, regular housekeeping practices such as consistent cleaning and disinfecting of commonly touched surfaces should be maintained.
- Developing workplace flexibilities and protections. Make sure sick leave policies are flexible and workers are aware of new procedures. Employees should be able to stay home to take care of a sick family member or children whose school or daycare are closed. Be aware of, and attempt to address, concerns about leave, pay, safety, and health. Actively encourage workers to monitor themselves for symptoms and to stay home if they feel ill. It helps to develop a procedure for reporting symptoms or cases of illness.
Implementing Workplace Controls and Prevention
OSHA’s recommendations for infection prevention follow the hierarchy of controls, a framework that helps to determine ways of controlling workplace hazards. The best way to control a hazard is to remove it from the workplace. In the event that it may not be possible to eliminate the hazard, which is typically the case for exposure to illness, the best protective measures (in order of most effective to least effective) are:
- Engineering controls
- Administrative controls
- Safe work practices
- Personal protective equipment
Engineering Controls
These are controls that attempt to isolate employees from work-related hazards, and reduce exposure without relying on worker behavior. For preventing exposure to illness, engineering controls may include installing physical barriers such as clear plastic sneeze guards or high-efficiency air filters, establishing drive-through or curbside pickup services for customers, and increasing ventilation rates.Administrative Controls
These are controls that rely on action conducted by workers and employers. Typically, this involves changes to work policy and procedures in order to reduce or minimize exposure to a hazard such as illness. This may include encouraging workers to stay home if they are sick, minimizing contact among people by replacing face-to-face meetings with virtual communication, asking employees to work from home, implementing social distancing, and canceling non-essential travel.Safe Work Practices
These practices are a type of administrative control that outline procedures for safe operations. They may be used to reduce the intensity, frequency, or duration of exposure to illness. This includes promoting personal hygiene and providing soap or sanitizer so employees may wash their hands. It also includes conducing a regular cleaning and disinfecting routine, and reminding workers to wash their hands especially as they move from workspace to workspace and any time after they have removed their PPE.Personal Protective Equipment
While PPE may be effective in preventing certain exposures, it should not take the place of other prevention strategies. The type of PPE required for your workplace depends on the specific job tasks and level of risk. Appropriate PPE may include gloves, gowns, masks, goggles or face shields, and respirators. All types of personal protective equipment must be selected based on the hazard, properly fitted, properly worn, properly removed, stored, and disposed of, and regularly inspected. As according to OSHA’s PPE standard, employers are obligated to provide their workers with the PPE that is needed to keep them safe on the job.Training for Illness Exposure and Prevention
Adequate training and informational material on proper hygiene practices and the use of any workplace controls, including PPE, must be provided to workers. Workers should be knowledgeable about the sources of exposure to illness in their workplace, appropriate protocols to put in place to reduce the likelihood of exposure, and how to report possible cases of illness. This training should take place during regular work times at no cost to the employee.
PPE is especially important to train workers on, as workers should know what type of PPE is specifically necessary, when to use it, how to properly use it, how to don and doff PPE, how to dispose and maintain their equipment, and most importantly, the limitations of PPE. In many cases, wearing protective equipment can give workers a false sense of protection and they may let their guard down.
Employees who are properly informed and trained are safer at work. By adhering to applicable OSHA standards, determining risk of exposure, and administering hazard controls in your workplace, you can help protect your workers from being exposed to illness. Especially at times when there are community outbreaks, every employer has guidelines they can follow to preserve the health of their employees and ensure the success of their business.
Similar Articles
- Job Hazard Analysis: Addressing Coronavirus Risk in Your Workplace
- Returning to Work Safely
- Fall Protection in the Workplace: OSHA’s Guidelines
- Cleaning the Workplace During COVID-19
- OSHA Respiratory Protection Standard (29 CFR 1910.134)
- An Introduction to Industrial Hygiene
- OSHA General Duty Clause
- OSHA Ear Protection Requirements (Standards for Hearing Safety)
- OSHA Facts [Updated Statistics 2019]