- What is Process Safety Management?
- When is a Process Safety Management program required?
- Process Safety Management + OSHA Compliance
- What are the 14 elements of PSM?
- Safe Management Tools for Chemical Processes in a Facility
- Visual Communication Within PSM Programs
- The Importance of GHS Labeling, Pipe Marking, and Signage
What is Process Safety Management?
Process Safety Management, also known as PSM, was introduced by OSHA to help companies improve employee safety in the presence of especially toxic, flammable, explosive, and reactive chemicals. This management program focuses on all processes involved in handling, utilizing, storing, transporting, and manufacturing chemicals classified as highly hazardous.
Process safety management was designed as an analytical tool to monitor how these chemicals interacted with. An accidental chemical release can occur at any time, but by looking to mitigate the risk of unexpected spills or leaks of those chemicals, countless industries can keep their workers safe from harm.
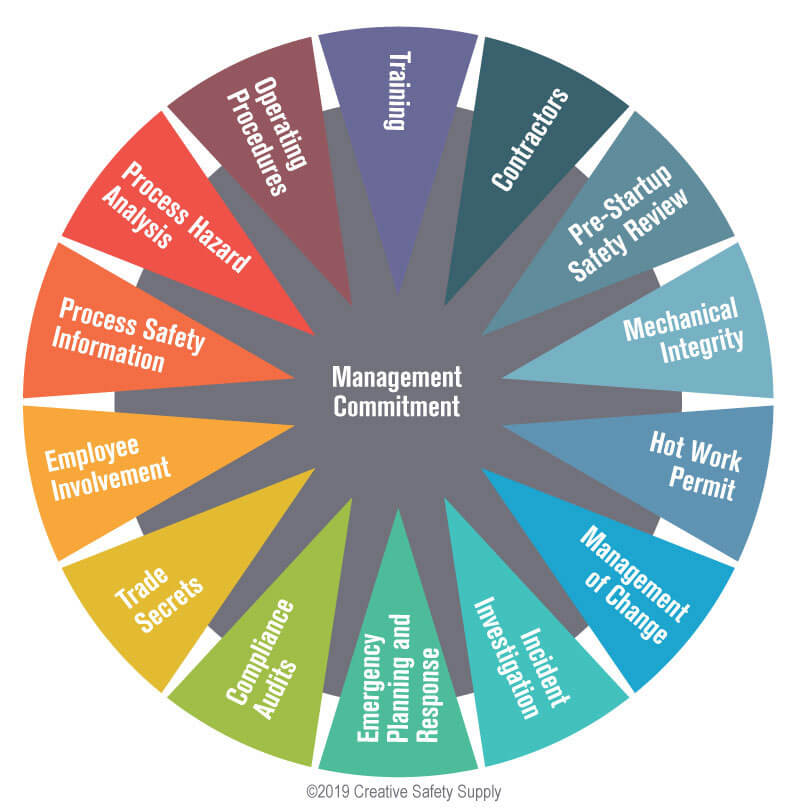
When is a Process Safety Management program required?
OSHA requires that process safety management be used when highly hazardous chemicals are necessary for production or are a byproduct of a process. There are 130 chemicals classified as highly hazardous. Once the possession threshold limits are exceeded or if the site is storing 10,000 pounds or more of a Category 1 flammable gas or liquid with a flashpoint below 100 °F, then a process safety management system is necessary to prevent accidents.
On the other hand, storing flammable liquids with flashpoints below 100 °F in atmospheric tanks or transferring them do not need PSM programs as long as they can be kept below their boiling points without the help of refrigeration.
The need to implement process safety management doesn’t involve retail facilities, oil, and gas well drilling, servicing operations for oil and gas, or normally unoccupied facilities. While still potentially dangerous, hydrocarbon fuels for workplace consumption like heating or gasoline refueling do not fall under the jurisdiction of this standard.
Process Safety Management + OSHA Compliance
Complying with OSHA's 29 CFR 1910.119 standard helps with reducing overall risk in potentially hazardous environments. When a facility properly implements the process safety management standards, as required by OSHA, they are working to prevent disasters involving these dangerous chemicals. The risk preventatives simultaneously assist in helping educate employees and others nearby to identify and take the necessary steps to avoid injury as well as property damage.
What are the 14 elements of PSM?
Once an organization has determined that it must implement a PSM program to keep its workers safe, it will find that there are 14 elements specified within OSHA's process safety management standard to establish an effective PSM program. While this is not an exhaustive list of information on the standard required by OSHA, it does include the basics of those 14 elements:
- Employee Participation: All employees involved with facility operations should be informed of the PSM program and all its elements. Employees must also be represented in meetings where PSM is addressed. Each of the following aspects of PSM should have an experienced team to work with as well.
- Process Safety Information: All highly hazardous chemical information needs to be compiled by the employer into a written document for reference. This must be done before any process hazard analysis is completed. The document must include information on the chemicals, technology used, and equipment used in the process.
- Process Hazard Analysis: This type of analysis must be conducted once every five years with the help of several analysis methods and will attempt to rank the greatest risks while resolving the high-priority ones first. The analysis itself must be completed by a team of engineering and maintenance experts as well as at least one knowledgeable employee who specializes in that process. They will then work to identify, evaluate, and eventually control the hazard present.
- Operating Procedures: For each operating phase the facility will need to address the initial process setup and startup instructions, normal and temporary operating conditions, and normal and emergency shutdown situations. All operators need to be aware of these conditions to be able to identify when deviation from normal conditions occurs and how to prevent them from happening.
- Training: Operator training will be provided by the employer and will emphasize the process’s specific safety and health hazards, safe work practices, and what to do in emergencies. Refresher training will be provided every three years at the very least. Once training has been completed, documentation must be kept on the date as well as a means of verifying that the employee understood the safety training.
- Contractors: Those who are hired to come in to perform maintenance, repair, renovation, turnaround, or specialty work must be evaluated by the employer regarding the contract employer’s safety performance and programs. The employer must warn the contractors of the potential danger of the highly hazardous chemicals and provide them with the basics of an emergency action plan as a precaution. They must also come up with safe work practices for the contractors to abide by. This information will be relayed to all other contractors before work has begun.
- Pre-startup Safety Review: The employer is required to perform a pre-startup safety review for new and modified facilities when the change is large enough to alter the process safety information.
- Mechanical Integrity: Pressure values, storage tanks, piping systems, relief and vent systems and their devices, emergency shutdown systems, controls, and pumps must be inspected routinely and documented. The procedures for checking this equipment must be contained in a written document and follow recognized and generally accepted good engineering practices.
- Hot Work: The employer must issue a hot work permit for when the activity will be conducted on or near a covered process. The permit must be kept on file until the task is completed.
- Management of Change: There must be a standard procedure for managing changes in chemical processing, technology, equipment, and other necessary procedures. The employer must take into account the technical basis for the change, the impact it has on the safety and health of employees, the modifications required for operation, the necessary period for the changes, and the authorizations needed for the changes to take place.
- Incident Investigation: An investigation must take place within 48 hours of an incident or a near miss involving the release of highly hazardous chemicals. The report must contain the date of the incident, a description, the contributing factors, and resulting recommendations. These reports must be kept for at least five years following the event.
- Emergency Planning and Response: Employers must establish an emergency action plan in accordance with 29 CFR 1910.38 and may be subjected to also follow the hazardous waste emergency response provisions within 29 CFR 910.120.
- Compliance Audits: Every three years the employer must verify that all practices and procedures under 1910.119 are being followed. The employer must keep the two most recent audits on file.
- Trade Secrets: Employers must make necessary information known as required in the previous sections despite the possession of a trade secret, as employee safety takes priority.
Safe Management Tools for Chemical Processes in a Facility
Safe management of chemicals within industrial sites require the help of safety systems because they have the potential to prevent accidents, detect risks, and even respond to incidents. The following are some examples of safety systems that can be seen in facilities:

- PSM charts: Within the process safety information section of PSM the use of a block flow diagram or simplified process diagram/PSM chart will assist with identifying important parts of a process that are within a higher risk category.
- Interlocks - Having a physical lock or using a lockout/tagout strategy can protect employees from entering high-hazard areas. This can also be a system that prevents the engagement of a machine until specific safety checks have passed.
- Detection Systems - Many advanced detection systems can identify small leaks or spills before they become a serious hazard.
- Suppression Systems - In the event of a fire or other hazard, a suppression system can help keep the risk contained to a small area.
- Filters - Filters can help remove dangerous particles, vapors, or gases from an area quickly and prevent them from coming into contact with people or the environment.
Choosing the right safety system for a facility is an important part of a PSM program. Depending on the type of chemicals that are present and how they are used, one or more safety systems may be necessary.
Visual Communication Within PSM Programs
Visual communication is extremely important in a process safety management program. Without labeling or signs placed around the facility, there will be no guarantee that employees will remember, or be experienced enough, to avoid emergency situations in the event one occurs. To avoid confusion and promote clear complete mutual understanding there are a few tools that come in handy, and those are GHS labeling, pipe labeling, and signage placed throughout the industrial site.
The Importance of GHS Labeling, Pipe Marking, and Signage
The Globally Harmonized System of Classification and Labeling of Chemicals, or GHS labeling, is an indispensable tool when it comes to identifying highly hazardous chemicals. These labels have the ability to quickly alert employees of the immediate danger that a chemical possesses. This is done with the help of GHS’s six main label requirements, of which include:
- A signal word
- GHS pictograms
- A hazard statement
- The manufacturer’s information
- A Precautionary statement
- Product identification, meaning the definition of the chemical’s properties
More in depth information on the chemicals should be able to be found on a safety data sheet, also known as an SDS. This document should have detailed information about the chemical hazards included on labels or signs. Some examples of information that can be found include the following:
- Thermal or Chemical Stability Information
- Information about Corrosiveness
- Details on Reactivity
- Physical Information
- Information about Toxicity
While these are referred to as tools, properly using GHS labels and keeping SDS documents on file is mandatory by OSHA. In fact, GHS labeling should be a part of every facility’s hazard communication program.
Pipe marking also falls under the category of visual communication and can be a lifesaver either in emergency situations or simply as a precaution within facilities that have a maze of piping infrastructure. Correctly labeling pipes is an easy task with the right information which can be found in the ANSI/ASME A13.1 standard. This standard specifies color combinations, label and text sizes, as well as placement for maximum visibility.
OSHA references the A13.1 standard within their own mandatory labeling requirements, which means that companies can be penalized for not following these best practice methods. For that reason, almost all businesses have adopted the voluntary pipe marking practices put forth by ANSI to make sure they are not cited by OSHA for not providing the safest environment possible for their employees.
Visual communication within a process safety management program would not be complete without safety signage. These can take the form of warning, danger, or caution signs, as well as signs detailing PPE requirements for the area, or even signs prohibiting food on the factory floor. Safety signs can come in numerous sizes, subjects, and colors as long as the message is short, easy to understand, and in a place where it is seen often to remind employees to be safe.
Overall, a process safety management program is a necessary analytical tool when it comes to managing chemical processes that involve highly hazardous substances. It will not only prevent leaks and spills, but also protect the community, employees, and the surrounding environment from dangerous chemicals.
Similar Articles
- Improving Workplace Electrical Safety
- Quality, Health, Safety, Environment (QHSE) Management Systems
- Workplace Safety Inspections & Audits
- Safety Colors (OSHA Guidelines and Color Codes)
- ISO 31000:2018 – Risk Management
- Anhydrous Ammonia – Safety & Labeling
- Material Safety Data Sheets [How-To Guide for Upgrading to SDS]
- Job Safety Analysis
- Warehouse Management (Supply Chain Systems + Visual Management)