- History of Ammonia Refrigeration
- What is Ammonia Refrigeration
- Ammonia Refrigeration Regulations
- Key Regulatory Bodies:
- How Does Ammonia Refrigeration Work?
- Components of an Ammonia Refrigeration System
- Types of Ammonia Refrigeration Systems
- Ammonia Refrigeration Cycle
- Hazards of Ammonia
- Ammonia Leak Detection Methods
- Advantages of Ammonia Refrigeration
- Piping Requirements
- International Institute of Ammonia Refrigeration (IIAR) Bulletins
- Industrial refrigeration ammonia systems
- Ammonia Pipe Labeling Requirements
- Ammonia Process Safety Management
Ammonia refrigeration is one of the older types of refrigeration that is still used today. While the average person doesn't realize it, just about all food and drinks that are purchased have been kept cold using ammonia refrigeration at some point along the way. This is because it is a reliable and efficient refrigerant with years of safe, proven utility.
History of Ammonia Refrigeration
People first started using ammonia as a refrigerant in France starting in the 1850's, and its use was brought to the United States in the 1860's. By the 1900's, ammonia refrigerators were being used in many commercial facilities to create blocks of ice, keep food cold, and produce other chemicals. Starting in the 1920's, it was used in ice rinks, and by the 1930's it was used in air conditioners for both industrial requirements and for keeping homes cool.
While ammonia is not commonly used in air conditioning units anymore, it is still very common for cold storage of food and in many industries that require this type of cooling. Today, ammonia is mostly used for larger scale cooling requirements such as college campus dorm room air conditioning, large office buildings, hospitals, airports, hotels, and more.
What is Ammonia Refrigeration
Ammonia refrigeration systems are, as the name implies, a system of refrigeration that uses ammonia. The ammonia is the chemical that is used to absorb the heat from one area, and bring it to another area to dissipate. Concentrated ammonia is much colder than typical room temperature, which makes it an excellent choice for keeping things cool.
Most people are used to using refrigeration systems that use CFCs, or even older systems that use Freon. Due to the environmental impact of these chemicals, and their cost, they are not the ideal choice in industrial environments.
Ammonia Refrigeration Regulations
Ammonia refrigeration systems are essential components in various industries, but due to the inherent hazards of ammonia, they are subject to a complex web of regulations. Understanding these regulations is crucial for ensuring the safe and compliant operation of these systems.
Key Regulatory Bodies:
Environmental Protection Agency (EPA): The EPA enforces regulations under the Clean Air Act (CAA) regarding the storage and release of ammonia. Facilities with a specific inventory threshold of ammonia may be subject to the Risk Management Program (RMP).
Occupational Safety and Health Administration (OSHA): OSHA enforces regulations under the Occupational Safety and Health Act (OSHA Act) to protect workers from exposure to hazardous chemicals like ammonia. Facilities with larger ammonia charges (typically exceeding 10,000 lbs) may be subject to OSHA's Process Safety Management (PSM) standard.
Additionally, industry standards play a vital role in ammonia refrigeration safety. These standards, while not strictly mandatory by law, are often adopted by regulatory bodies and provide detailed guidance for design, construction, operation, and maintenance of ammonia refrigeration systems. Key standards include:
ANSI/IIAR Standards: Developed by the American National Standards Institute (ANSI) and the International Institute of Ammonia Refrigeration (IIAR), these standards address various aspects of ammonia refrigeration systems, including operation procedures and decommissioning.
ANSI/ASHRAE Standards: Established by the American Society of Heating, Refrigerating and Air-Conditioning Engineers (ASHRAE), these standards provide comprehensive guidelines for the safe handling of refrigerants, including ammonia (ANSI/ASHRAE Standard 15).
These are just some of the major regulatory bodies and standards. Depending on your location and the specific characteristics of your ammonia refrigeration system, additional federal, state, or local regulations may apply. Consulting with regulatory agencies and qualified professionals is highly recommended to ensure complete compliance with all applicable regulations.
How Does Ammonia Refrigeration Work?
An ammonia refrigeration system, like all vapor-compression refrigeration systems, are made up of a number of components that work together. Essentially, the ammonia is the chemical that is contained within the system to remove heat from an area, and then dissipate it in another area. Ammonia is very efficient at this because it has a very low boiling point when liquid (-27F).
Components of an Ammonia Refrigeration System
As with all refrigeration systems, there are a number of components that are needed to keep the system working properly. If any of them are missing or break down, the refrigeration system will stop working almost immediately. The required components are a compressor, condenser, expansion device, and an evaporator.
You can see the basics of how this works in the following image:
In addition to these basic components, many units will have additional parts to help ensure everything works as efficiently as possible. Many refrigerators will have a fan to direct the cool air where it needs to be, and of course there will be an insulated area to help keep heat out so that the refrigeration unit doesn't have to work any harder than necessary.
Types of Ammonia Refrigeration Systems
Ammonia refrigeration systems utilize the thermodynamic properties of ammonia (NH3) to achieve a cooling effect. There are three main classifications based on the method of refrigerant feed and control:
Thermal Expansion Valve (TXV) Systems: These, also referred to as dry expansion systems, precisely control the amount of liquid ammonia entering the evaporator using a thermal expansion valve (TXV). This ensures all liquid is vaporized before reaching the compressor, preventing damage. TXV systems are generally less complex but have slightly lower efficiency due to the need for larger evaporators to guarantee complete vaporization.
Flooded Liquid Recirculation Systems: In flooded systems, a pump or pressurized gas circulates a large quantity of liquid ammonia through the evaporator, often exceeding the amount that can be vaporized. This ensures a constant liquid level in the evaporator coil, maximizing heat transfer efficiency. However, flooded systems require additional equipment like pumps and separators, increasing complexity.
Liquid Overfeed Systems: Similar to flooded systems, liquid overfeed systems circulate a large amount of liquid ammonia. However, the driving force is the pressure difference between the high-pressure receiver and the evaporator, eliminating the need for a separate pump. This simplifies the design but requires careful management of pressure differentials to prevent excessive liquid carryover to the compressor.
The most suitable type of ammonia refrigeration system for a specific application depends on various factors, including:
Desired cooling capacity: Flooded and overfeed systems are generally better suited for larger capacity applications.
Temperature control requirements: TXV systems offer precise temperature control, making them ideal for situations requiring tight tolerances.
System complexity and maintenance needs: TXV systems are simpler but may require more precise control measures. Flooded and overfeed systems offer higher efficiency but involve additional equipment and maintenance considerations.
Consulting with qualified engineers is crucial to determine the optimal type of ammonia refrigeration system for your specific needs.
Ammonia Refrigeration Cycle
An ammonia refrigerator works in the same basic way that most other refrigeration systems operate. The ammonia refrigeration cycle begins with bringing in warm air, stripping the heat out of it, and then sending the cooled air back where it needs to be.
Each step in this cycle is essential in regulating the temperature properly. The following image gives a good introduction to the ammonia refrigeration cycle, which will be explained in more detail after. Part of this is offering advice on how to recognize a hazard in these refrigeration units. Early detection of a leak can allow everyone time to safely evacuate while the leak is repaired.
While ammonia refrigeration hazards need to be taken seriously, they aren't a common enough issue to make most facilities worry about installing these refrigeration units. When installation is done properly and everyone receives the right training, ammonia refrigeration units are a safe way to keep areas cool.
In the cycle, the ammonia gas is compressed using the compressor, which causes it to heat up as it is pressurized. Upon reaching this point, the ammonia travels up into the coils typically located in the back of the refrigeration unit. In the coils, the heat is dissipated, which causes the ammonia to condense into a liquid.
That liquid ammonia then travels through the expansion valve, which is a small hole that opens up into a lower pressure area. When this occurs, the ammonia quickly begins to boil. It is important to note that liquid ammonia boils at -27F, and obviously is much colder than the surrounding area.
The cold ammonia cools the air around it, the inside of a refrigerator in many cases. While the ammonia begins to warm, the air gets colder. The ammonia continues to travel through the refrigerated area slowly becoming warmer as it goes. Finally, it will be sucked back into the compressor where it will begin the cycle again.
Hazards of Ammonia
When using ammonia refrigeration, or ammonia for anything in the workplace, there are a variety of OSHA regulations that need to be followed. Having proper safety equipment in place and keeping the refrigeration unit well maintained can help reduce the risk to employees.
Ammonia can be extremely dangerous. If someone is exposed to as little as 300 parts per million in the air around them, they will likely experience extreme health issues and potentially even die from exposure. Ammonia is a highly corrosive chemical and must be washed off immediately and treated promptly to prevent long-term problems from skin or eye exposure.
OSHA provides guidance for handling ammonia emergencies, as well as first aid recommendations.
Fortunately, ammonia has a very strong odor that people naturally find offensive. This odor is very distinctive and detectable at around 20 parts per million, which is significantly lower than the hazardous levels. When people begin smelling ammonia, they can evacuate the area quickly and have the maintenance teams take care of the problem.
Ammonia is also quite flammable. If there is a 15% or higher concentration in the air, it can ignite when exposed to an ignition source. In ammonia refrigeration, the ammonia is often mixed with lubricating oils, which can cause it to become even more flammable. Having fire suppression systems in place around ammonia refrigeration units is often recommended.
Ammonia Leak Detection Methods
Prompt detection of leaks is critical for ensuring the safety and environmental compliance of ammonia refrigeration systems. Various methods are employed to identify and locate ammonia leaks, each with its own advantages and limitations.
Direct Detection: The most basic method involves physically observing the system for signs of leakage, including visual inspection of piping, flanges, and joints for frost formation or liquid ammonia accumulation. However, this method can be unreliable for small leaks or those obscured by insulation.
Ammonia Detectors: These electronic devices continuously monitor the atmosphere for ammonia gas. They typically employ electrochemical sensors or infrared absorption spectroscopy to detect ammonia concentration exceeding a preset threshold. Upon detection, alarms are triggered, alerting personnel and initiating appropriate response protocols.
Leak Detection Solutions: Certain solutions, often applied with a spray bottle, change color when exposed to ammonia. These solutions are relatively inexpensive and easy to use for qualitative leak detection, but may not be suitable for continuous monitoring.
Ultrasonic Leak Detection: Ultrasonic detectors can identify leaks by pinpointing areas emitting high-frequency sound waves generated by escaping ammonia gas. This method is particularly useful for detecting small leaks that may not be readily apparent by other methods.
Infrared Cameras (IR Cameras): IR cameras can visualize temperature variations. Since escaping ammonia gas causes a localized cooling effect, IR cameras can be used to identify potential leaks by detecting areas with lower than expected temperatures.
Selection of the appropriate leak detection method depends on several factors, including:
Desired sensitivity: Some methods, like ammonia detectors, offer high sensitivity for small leaks, while others may only detect larger leaks.
Monitoring needs: Continuous monitoring with ammonia detectors may be necessary for critical systems, while spot checks with leak detection solutions may suffice for less critical applications.
Cost and complexity: Simple methods like visual inspection are cost-effective but less reliable. Electronic detectors and IR cameras offer higher reliability but come with a higher upfront cost.
A comprehensive leak detection strategy often involves a combination of methods, employing continuous monitoring with electronic detectors supplemented by periodic visual inspections and targeted use of other methods like ultrasonic detection or IR cameras.
Advantages of Ammonia Refrigeration
When proper precautions are taken, ammonia refrigeration units offer many advantages compared to traditional CFC or HCFC based units. For many large industrial situations, these advantages make this type of refrigeration unit a smart choice:
- Less Expensive - Ammonia refrigerators require narrower piping, which is less expensive to make. This type of refrigeration unit will cost 10-20% less than other models.
- Efficient - Ammonia refrigeration is also 3-10% more efficient to run than units that use CFCs. This translates to lower electric bills and a facility that is more environmentally friendly.
- Ozone Safe - Unlike CFCs, ammonia does not harm the ozone layer. Experts also agree that ammonia use in refrigeration does not contribute to global warming.
- Chemical Cost - Ammonia is significantly less expensive to obtain and use than CFCs, which makes it more affordable to "recharge" a unit.
Piping Requirements
Whenever working with ammonia refrigeration units, it is important to remember that ammonia can be corrosive to certain types of metals. Copper piping, which is commonly used in other types of refrigeration units, cannot be used when working with ammonia.
Labeling the piping in these units to alert those performing maintenance to this requirement can help avoid potential problems. If this precaution is not taken, someone may unintentionally replace a pipe with one made of copper, leaving the facility at risk of a leak.
International Institute of Ammonia Refrigeration (IIAR) Bulletins
The International Institute of Ammonia Refrigeration is an organization that educates and informs about best practices for safely using ammonia for refrigeration. IIAR also provides standards for this purpose.
Additionally, IIAR publishes bulletins that offer guidance to facilities. This guidance provides clarification about safe ammonia use, especially when standards do not explain a particular topic. Below are relevant bulletins:
IIAR Bulletin 108 - Guidelines for: Water Contamination in Ammonia Refrigeration Systems
- Explains how water can contaminate an ammonia refrigeration system, how this can be prevented, and how water can be removed.
IIAR Bulletin 109 - Guidelines for: IIAR Minimum Safety Criteria for a Safe Ammonia Refrigeration System
- Covers the safe design, operation, and inspection of ammonia refrigeration systems. Also includes ammonia refrigeration safety inspection checklists for equipment.
IIAR Bulletin 110 - Guidelines for: Start-Up, Inspections and Maintenance of Ammonia Mechanical Refrigerating Systems
- Covers ammonia hazards as well as equipment maintenance and start-up issues.
IIAR Bulletin 114 - Guidelines for: Identification of Ammonia Refrigeration Piping and System Components
- Provides ammonia labeling guidelines that cover label materials, sizes, colors, etc.
Industrial refrigeration ammonia systems
Industrial refrigeration ammonia systems are the workhorses of various industries, particularly those requiring large-scale cooling for food preservation, chemical processing, and cold storage. Ammonia, a naturally occurring refrigerant with efficient thermodynamic properties, forms the core of these systems. The system operates through a closed loop: a compressor pressurized ammonia gas, raising its temperature. This hot, high-pressure gas travels through a condenser, where it releases heat to the surrounding environment and condenses into liquid ammonia. A regulated flow of this liquid ammonia then enters the evaporator, where it absorbs heat from the space or product being cooled, transforming back into a gas. Finally, the low-pressure ammonia gas re-enters the compressor, and the cycle repeats. These systems offer high efficiency and low operating costs but require careful design, operation, and maintenance due to the inherent hazards of ammonia, which is toxic and can form explosive gas mixtures under certain conditions.
Ammonia Pipe Labeling Requirements
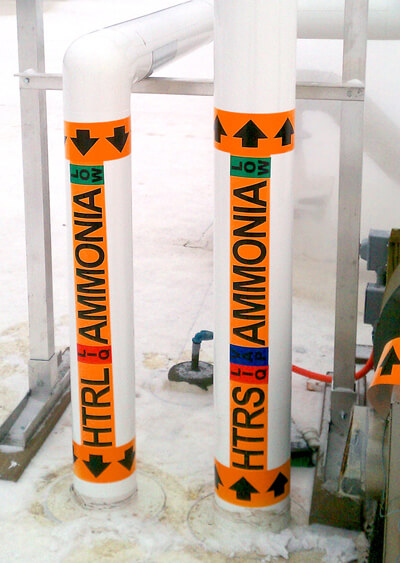
As mentioned above, IIAR Bulletin 114 covers the requirements for ammonia piping labels. These requirements are different from ANSI pipe label guidelines, which apply to most other pipes and are accepted by OSHA in its pipe labeling requirements as well.
IIAR's guidelines explain that ammonia marking labels must meet specific requirements for content and formatting.
Labels have five parts: abbreviations for ammonia system components, physical state (liquid/vapor), marker body ("AMMONIA"), the pressure level (low/high), and an arrow indicating the flow direction.
Ammonia Pipe Abbreviations
IIAR Bulletin 14 includes a list of abbreviations that can appear on an ammonia pipe label such as: CD (Condenser Drain), LT (Liquid Transfer), LTRS (Low Temperature Recirculated Suction, OD (Oil Drain), and RV (Relief Vent). Users can consult IIAR for a full list of accepted abbreviations.
Ammonia Piping Color Code
Recent updates to IIAR Bulletin 114 require that ammonia pipe labels are orange with black text (they were previously yellow). The physical state Liquid should be on a yellow rectangle, and Vapor should be on a blue rectangle. The pressure Low should be on a green rectangle, and High should be on a red rectangle. Consult the diagram above for placement of these label parts.
Those interested can also learn more about these industrial labeling requirements in our Ammonia Pipe Marking Guide, which explains how to create labels according to IIAR pipe marking guidelines.
Ammonia Process Safety Management
Businesses that use ammonia for refrigeration and have systems that contain 10,000+ pounds of ammonia (about 2000 gallons, according to the EPA) should also consult guidelines for process safety management. OSHA's standards can be found here. OSHA's Ammonia Refrigeration eTool also has information about IIAR Process Safety Management Guidelines for Ammonia Refrigeration.
Process safety management deals with how to safely manage processes that use hazardous chemicals, and ammonia falls into this category of very hazardous chemicals.
Resources
- https://www.osha.gov/ammonia-refrigeration
- https://www.goodway.com/hvac-blog/2009/08/ammonia-as-a-refrigerant-pros-and-cons/
- http://www.aboutammoniarefrigeration.com/aaranswers_history.cfm
Similar Articles
- Anhydrous Ammonia – Safety & Labeling
- A Guide to Pipe Marking Standards
- ANSI Color Codes for Pipe Marking
- Waste Water Treatment Labeling
- Pipe Color Codes – ANSI/ASME A13.1
- Your Guide to Pipe Labeling Standards
- Hazardous Materials Identification System (HMIS Labels)
- Understanding the NFPA 704 Diamond Labeling System
- GHS: The Globally Harmonized System for Labeling [Updated 2019]