Chaku Chaku is a Japanese term that translates to "Load Load." It is a manufacturing process that looks at how to improve processes, automate what can be automated, and allow workers to "cell load" machines. This means they take a part from one machine (or inventory) and put it into the next machine. Once secured in place, it should progress through the machine as far as possible and be removed from the machine all on its own.
Introduction to Chaku Chaku
Chaku chaku encourages companies to put all the machines required to create a product in the same area or cell. By having these machines physically close together, it reduces the amount of downtime involved when a part or product has to be moved from one machine to the next.
Work "Cells"
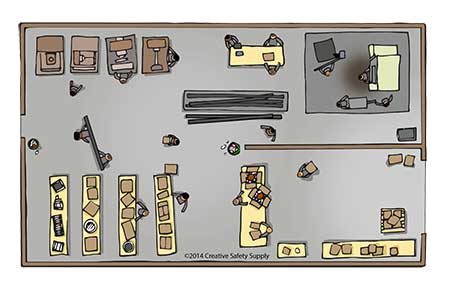
One of the key aspects of chaku chaku is the work cells, also called Lean manufacturing cells. The term cell refers to a small area and is not meant to suggest anything related to a jail cell. Setting up work areas in these cells helps keep all the work that needs to be done together in one area.
The recommended configuration of a work cell is in the shape of a U. The work starts at one end of the U, flows through each machine, and is then completed at the other end of the U. This is a very efficient option as it allows the employee to follow the progress of each product through to completion, and once it is complete, they are right next to the start again so there are very few wasted steps.
Positioning machines properly so the employee can load one machine, then grab the completed part from it and immediately load it into the next machine, is very important. This is a streamlined process that allows the workers to develop a rhythm in their work.
Chaku chaku also makes completing the necessary tasks very intuitive. Employees simply need to know that they load the parts into the machine right next to the one that the parts just came out of. This can dramatically reduce confusion, which can cause errors and other issues on the production line.
The work cells should be kept as small as possible, while still allowing all the machines to fit in place properly. Some larger cells are big enough for two or more employees to conduct the same tasks without running into each other.
Multiple Employees in One Cell
When multiple employees are working in one area, they shouldn't run into each other because they will both go through identical steps in the manufacturing process. Even if one step is much quicker than another, the employees each have to go through both the fast and slow steps, so there won't be any type of bottleneck in the process. Of course, multiple employees should only work in one cell when it is necessary for keeping production steady.
Automation
Automation is a very important part of chaku chaku. When implementing this strategy, it is important to analyze each step involved in creating a product and determine what can be automated. With modern machinery, it is often possible to automate a significant amount of manufacturing processes. Some reasons why something can't be automated include:
- Cost - Companies may not have the budget to purchase the machines or other equipment required for automating a specific task. Conducting a cost-benefit analysis can help determine whether it is worth purchasing a new machine when the budget is there.
- Complexity - While machines can do many things today, there are some tasks they still can't do properly (without massive innovation or investment). For example, when a part needs to be taken from one area and placed in an exact position, automation might not be the right option.
- Decisions - Using computers, machines can make surprisingly complex "decisions" about different tasks that need to get done. In some cases, however, it is easier or more affordable to have a human who can quickly analyze the situation and make the right choice.
There may be other reasons why automation won't work in a specific situation. While certain tasks won't be automated in any process, it is important to look seriously at every step in the manufacturing process to see what can and can't be automated.
Unloading Parts
One important thing that should always be automated is the unloading of parts from a machine. In chaku chaku, employees should only be loading machines, and the unloading process should be automated. This is how the process got its name (load, load). This is possible because unloading parts or products is very easy compared to putting them into a machine.
It is important because finished parts or full products need to be handled carefully to ensure they aren't damaged. Machines are much more reliable than humans since they can perform tasks in the same way every single time.
Checking for Problems
When an employee puts the initial part into the first production machine, they will be physically holding it in their hand. In addition, they will grab the ejected part from the machine when it is done and place it into the next machine in the process. At each step of production, the employee will move the piece and load it into the machine.
In addition to keeping production flowing, this step is an excellent opportunity for employees to watch out for problems. If a part is ejected and has an improper cut on it, the employee can stop production immediately to figure out what caused the issue. If it was a problem with the machine, it can be fixed before any more parts are damaged.
The faster a defect is discovered, the fewer parts will have problems. This will help reduce the amount of waste a facility produces. Waste elimination is a huge priority for most businesses, so anything that can be done to address this problem is critical. Chaku chaku has a system of problem detection built right into it, which is one of the reasons it is such an effective production system.
One Piece Flow
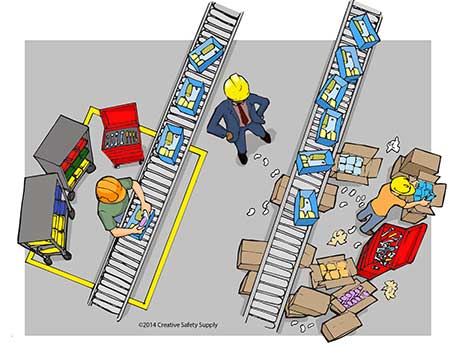
One of the most important concepts to understand while considering chaku chaku is the idea of "one-piece flow." When first considered, it seems to go against what many other production methods recommend.
One-piece flow is the idea that a single piece (or product) should enter the manufacturing process at one location and be continuously worked on all the way through until completion. This is in contrast to the concept of batching, where a large number of parts go through a single step of the manufacturing process and then are held until they are ready to go through the next step.
One-piece flow greatly reduces the amount of inventory that needs to be kept in the facility at any given time. Rather than having to store a large number of parts that have completed 2 of 5 production steps, a facility only has raw inventory that hasn't gone through any production and completed parts that should be shipped out as soon as possible.
This allows companies to use much more "on-demand" manufacturing, which lets them avoid the risk of overproduction. Overproduction can cause significant issues in manufacturing, which is why this is such a good standard to work toward.
Benefits of Chaku Chaku
There are many advantages of using the chaku chaku process in a manufacturing facility. The amount of improvement a facility will enjoy will depend on their existing way of doing business and how much automation can be used. The following are some of the many perks that companies see once they have implemented chaku chaku:
- Automation - Relying on automation is essential in any modern facility. Any system that strongly encourages automation will help improve the bottom line of the company.
- Visual Controls - Having the "in" locations and "out" locations physically close together makes it easier to visually inspect products as they are worked on.
- Reduced Inventory - Many other production methods encourage batches of individual parts to be created all at once and then stored until they are needed. This can result in significant amounts of inventory having to be stored on site for extended periods of time.
- Lean Production - Chaku chaku is completely in line with Lean manufacturing standards, which a growing number of companies are moving toward.
- Efficient Use of Floor Space - By positioning the machines used to make a product close together, the floor space is used more efficiently. This can make it possible to produce more things in a smaller area.
- Standardized - The tasks employees perform are all extremely standardized. Using standardization helps avoid defects, improves efficiency, improves safety, and generally allows for higher rates of production.
- Defect Identification - Since parts constantly go through the entire production line, it is much easier to detect when there is a problem. Rather than having dozens, or even hundreds, of parts end up with defects, a problem will be noticed after just one or two.
Implementing Chaku Chaku
When a facility is implementing chaku chaku, it is important to show the employees the benefits that will come from this system. Some employees are resistant because it really puts an emphasis on following set processes and routines. Even if the existing workflow processes are repetitive, the wasted time and energy used walking from one machine to another can make it seem less like a pattern.
Most facilities that implement this system find that their employees like the routines and are able to get a lot more work done per shift. This can help raise the bottom line while also eliminating waste, which is a good thing for everyone.