Mass production is production of a large number of products that are the same, or very similar. This type of production often uses assembly lines where either people or machines perform the same tasks repeatedly to create as many of a single product as possible, as quickly as possible, and with as few variations or defects as possible.
The concept has been around for a very long time, but it really became a standard way of doing business when Henry Ford and the Ford Motor Company began mass producing vehicles in the 1920's. This is also where the term was originated.
Benefits
Mass production is used in many industries because it is a great way to meet large scale demand of most types of products. The following are some of the most significant benefits that companies, and consumers, can get from mass production:
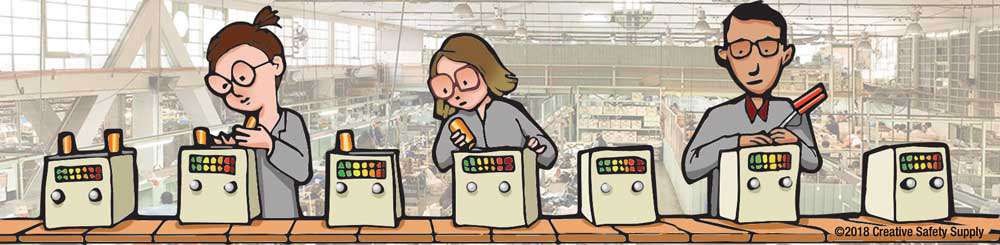
- Efficiency - Producing large numbers of a product is much more efficient than creating multiple different products in one facility.
- Specialization - When mass producing something, it makes sense to buy or create a machine that specializes in performing one specific task very well. Without mass production, a machine like this would not be useful, or would need to be much more complex.
- Training - Facilities can often be trained on their specific roles quickly, so that they can perform it properly every time. With other types of production, employees often have to learn many more tasks, which can take a lot more time.
- Standardization - By mass producing a product, it is easier to eliminate defects or variation, which allows a company to produce a much more uniform product. This is good for consumers who will know what they can expect when purchasing.
- Reduced Costs - The costs associated with mass production can be significantly lower than small-batch production. This is because the supplies can be purchased in bulk, and a discount can often be secured.
Drawbacks of Mass Production
There are some advantages to mass production, but there are also many disadvantages to mass production. Understanding the pros and cons is important for any business that is weighing their options. The following are some of the most significant disadvantages to mass producing products:
- Initial Expenses - Setting up a facility for mass production usually comes with a much higher cost than just creating individual products. Specialized machinery can be very expensive, and even cost prohibitive for newer companies.
- Job Satisfaction - Employees who need to perform the exact same task day in and day out can lose motivation, and this can lead to job dissatisfaction and higher worker turnover.
- Lack of Flexibility - This kind of production system is not very flexible for making customizations or unique products for customers.
- Risk of Production Outages - If one machine fails, it will often shut down the entire production line until it can be fixed.
Maximizing Production
Companies that use mass production techniques typically do it so they can maximize their output, and their profits. By using mass production, it is not only possible to produce a large number of products quickly, but it can also be easier to make improvements over time.
If a company makes even a small change to the way things are done, it will immediately impact every product that is created. For small scale production, this will have a limited impact. With mass production, the impact is quickly multiplied to make it well worth the effort.
Without mass production, many improvements wouldn't be worth the cost and effort required to implement them because they wouldn't be able to pay for themselves quickly enough. With mass production, an improvement in efficiency of even a small amount can quickly produce a great return on investment.
Safety Improvements
One area where changes can have a strong positive impact not only on the products, but also on the people working in the facility, is with safety improvements. Having a facility where the same products are made over and over again, the standardization can help to eliminate many safety concerns.
Employees working in an area will know precisely what needs to be done, and can even spot abnormalities more quickly because of the standards. If something isn't working the way it should, teams can investigate before anything goes wrong.
In addition, if someone comes up with a safer way of performing a task, it can be evaluated and implemented throughout the facility. Even if it is only slightly safer, the end result will be fewer accidents and injuries. In addition to the benefit of not having someone get hurt on the job, this will also help to reduce work stoppages due to accidents, which can have a positive impact on the bottom line.
Waste Elimination
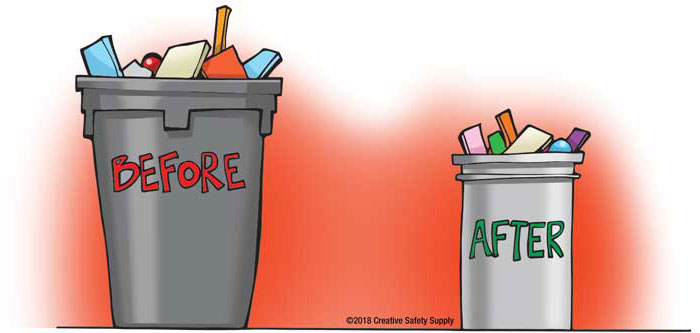
Mass production facilities are typically far more efficient than other types of production, and it is also much easier to further eliminate waste when it is identified. Using Lean manufacturing strategies, a company that is mass producing can identify waste and make plans to eliminate it much more easily than would otherwise be possible.
If a new process is developed that would reduce the physical waste of a product by 1%, it may not be worth the time and effort to implement it in facilities that make a few hundred of the product per year. Manufacturing facilities that are making thousands of them per day, however, will want to make the change as soon as possible as the reduced waste will add up to very significant savings.
In addition to reducing physical waste, it is easier to reduce wasted time and effort when engaged in mass production. When one employee finds a more efficient way of doing things, it can be quickly tested to confirm it works well. Once it is confirmed, the facility can change the procedures of that job, and have everyone who performs it follow the new and improved standards. This is especially helpful in facilities that run multiple shifts.
Visual Communication in Mass Production
Many workplace techniques can be used more effectively in mass production environments. Visual communication is an excellent example of this. By using visual cues in the workplace, employees can have a constant reminder of exactly what needs to be done, and when.
Using floor markings, for example, a facility can show the flow of products through the manufacturing process. This makes it easier to track how things are done, and identify where problems are occurring. Employees will also be able to better track where they are supposed to be throughout their work day, which can help to avoid mistakes or other issues within the workplace.
Additional Mass Production facts:
- Mass production is a method of manufacturing that uses standardized parts, assembly lines, and specialized workers to produce large quantities of identical goods at low unit costs. Source: https://www.britannica.com/technology/mass-production
- Mass production was pioneered by Henry Ford in the early 20th century, when he introduced the Model T automobile and the moving assembly line. Ford’s innovations revolutionized the automotive industry and influenced other sectors such as aviation, consumer goods, and food processing. Source: https://www.masterclass.com/articles/mass-production
- Mass production has many advantages, such as economies of scale, increased productivity, lower prices, and higher quality. However, it also has some disadvantages, such as environmental impact, worker alienation, loss of flexibility, and reduced innovation. Source: https://corporatefinanceinstitute.com/resources/management/mass-production/
- Mass production is often contrasted with mass customization, which is a strategy that combines the efficiency of mass production with the personalization of custom-made products. Mass customization uses technologies such as computer-aided design, 3D printing, and modular design to create products that meet the specific needs and preferences of individual customers. Source: https://www.wallstreetmojo.com/mass-production/
- Mass production is not only applicable to physical goods, but also to digital products and services. For example, software development, online education, and social media platforms are examples of mass production in the digital realm. These products and services can reach millions of users with minimal marginal costs and high scalability. Source: https://en.wikipedia.org/wiki/Mass_production