It can be difficult to establish and maintain an efficient warehouse. Large amounts of inventory can lead to many kinds of waste, including overproduction and bottlenecks—which is why it’s highly important to organize your warehouse’s storage system by numbering it. Once aisles and shelves are numbered, you can create labels that help workers track what type of warehouse inventory is being stored and where items are located. This prevents items from idling on shelves and allows employees to complete their work more efficiently.
Most warehouses use WMS (warehouse management system) software to keep track of their inventory, orders, and procedures so they can ensure transparency within the warehouse as well as within the company’s larger supply chain. With a WMS, warehouse locations can be effectively mapped for optimized efficiency. Formulating a warehouse storage numbering system can take a lot of training and logistics, but once your plan is in place, you’ll able to streamline operations in your warehouse as much as possible.
What Are Storage Systems in a Warehouse?
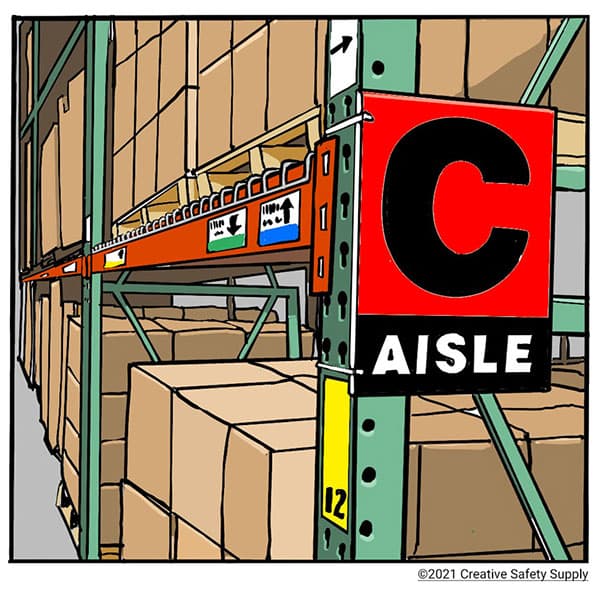
In order to establish a warehouse that is fully organized and functional, one of the first steps is to select what type of storage system best complements your layout. There are several categories of systems available, and these storage systems are a major investment that can enhance your throughput as long as they are compatible for your warehouse design, floor plan, and processes. Common categories of storage systems in a warehouse include:
- Pallet rack systems. This racking system accommodates pallet racks and is most commonly used for grocery stores. Pallet racking systems hold inventory that’s stored in large boxes or in bulk. If you have pallet racks, you’ll also need automated mechanisms or forklifts to transport items.
- Mezzanines. Mezzanine flooring is popular for many warehouse layouts, as it’s a very space-saving option. This involves constructing one or more platforms above the main warehouse floor for varying levels of storage. While you have a lot of options for customization, mezzanines do tend to be more expensive.
- Static shelving. Static shelving is a popular choice for warehouse inventory that needs to be constantly replenished, as this system stays in one place and can be much easier to organize. It’s not compatible with forklifts, so with this system your items must be manually placed and picked.
- Wire partitions. This storage system is most commonly used for creating storage rooms or securing tools. If you have anything in your warehouse that requires additional security, wire partitions are a great option, as they can be modified in shape and expanded or reduced as needed.
- Multi-tier racking. This is the best choice if you have a large stock of items with small unit sizes, because it utilizes vertical space as much as possible. Muti-tier racks are also very flexible to work with, as you can remove or add tiers depending on your needs.
The system that works best for your warehouse depends on your unique business operations, your industry, and the nature of the items you store. Select a system that has enough flexibility to support your company as it grows.
Need barcodes?
Our free barcode generator allows you to create custom barcodes readable with any scanner.
Warehouse Location Mapping
Once you’ve selected your warehouse storage system, the key is to implement an effective warehouse location mapping strategy. Warehouse location mapping is defined as identifying and naming all the shelving positions for your products, work areas, and paths of travel within your warehouse facility. An effective analogy is to think that each product should have its own place to “live,” and to think of a warehouse as an item’s home address, with aisles as the street, shelves as floors within an apartment building, and shelving units as the individual apartment unit. When a worker picks an item, your warehouse location system should direct the worker to where the unit “lives” as quickly and accurately as possible.
The best way to begin your process of warehouse location mapping is to walk through the warehouse and conduct an assessment that identifies the most ideal picking strategy. Take note of streamlined routes, highly trafficked areas, and other spots that may lead to trouble or waste. It helps to speak with workers and gain first-hand knowledge about movements and routes to prevent anyone from having to double back to retrieve products. The most popular items should be placed in the most accessible areas.
Location Numbering Systems and Where They Are Used
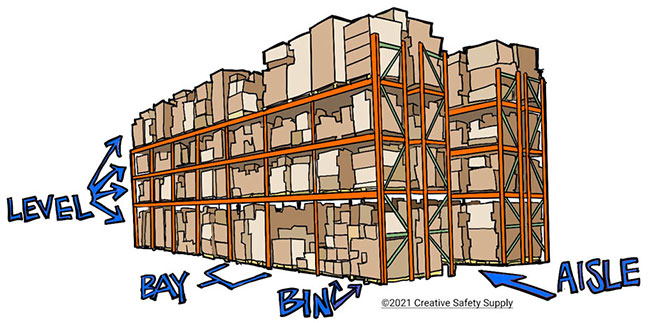
Your warehouse storage numbering system should be as specific as possible so it’s easy to locate items. Your location system should identify each element of storage location, including aisle, shelf or level, and position on the shelf from left to right (for example, pallet racks may contain two or three pallet positions).
Each aisle in your warehouse should have a corresponding aisle number, general starting with “01” and beginning from one side of the building to the other. Rack sections (the area between the uprights, also known as “bay”) are given ascending numbers with even-numbered sections on the right side of the aisle and odd-numbered sections on the left. The same numbering system can be used for shelf/level, and position.
Once you have an idea of how to strategically implement location mapping for your warehouse, the next step is to order warehouse location labels. Label stock that was designed to hold up to the harsh conditions of warehouses is most ideal, especially considering the varying climate, temperature, and general wear and tear of warehouse environments. If you use transitional racks or temporary storage solutions, you can invest in magnetic labels for temporary labeling and easy removal. To make your warehouse as efficient as possible, proper labeling is essential.
What Information is Found on a Rack Label?
The most common tool for rack labeling and other types of warehouse numbering systems is industrial barcode labels. These labels present a one-of-a-kind, scannable code that provides the information workers need about the particular item they need to pick within a warehouse. When a worker scans a barcode, they’ll be able to find information such as how much inventory there is, where it is located within the warehouse, and how long it’s been there.
With barcode labels, locating the aisle number, shelf number, and position for an individual item takes a matter of seconds. This enables workers to complete their jobs as efficiently as possible and boosts your warehouse operations. It also prevents waste from occurring, as it helps prevent items from idling on shelves.
Best Practices for Creating a System
While there are no universal requirements for warehouse storage numbering systems and each system tends to be unique to its business and industry, there are some common rules of thumb that make implementing a system much easier. These best practices also ensure that your numbering system is customized to your unique needs:
- Base the system on your picking technique. The “picking technique” is the method in which workers select products. Picking techniques tend to be either standard, in which pickers move from location to location, or serpentine, in which pickers weave up and down the aisles, a strategic option that prevents workers from having to double back.
- Label from the bottom up. In many warehouses, a storage solution will involve multiple levels and high density—especially if you select mezzanine flooring or multi-tier racking. If you have more than one level of shelving, it’s recommended to label from the ground up. Starting with “01” and using double digits accommodates the fact that you may add more levels in the future so you won’t need to change your system.
- Sustain your system for the long term. Optimizing the efficiency of your warehouse is made much easier with a numbering system that is standardized. Consistency and durability are key; if you implement a system and an aspect to it doesn’t work, you may need to make several attempts before you find a universal solution for your facility. Once you identify what works, you can ensure the system is used indefinitely by installing permanent, durable labels that will stay easily legible for the long term.
Similar Articles
- Rack Labeling
- Warehouse Management (Supply Chain Systems + Visual Management)
- MIL-STD-129: Military Marking for Shipment and Storage
- Perpetual Inventory System
- Tool Storage Ideas
- Kanban Production System
- Creating a Visual Workplace
- How to Implement 5S in an Organization
- Choosing to Implement a Periodic Inventory System