When attempting to adhere to EHS standards, it’s best to use the Hierarchy of Hazard Controls to efficiently and effectively mitigate occupational hazards within the workplace. The National Institute for Occupational Safety and Health (NIOSH) defines the five levels of the Hierarchy of Controls as elimination, substitution, engineering controls, administrative controls, and personal protective equipment.
Following this hazard control hierarchy provides the user with the power to reduce workplace hazards in such a way that accidents become less likely to occur and much less likely to cause serious injury. It also doesn't require any advanced knowledge of other industry strategies or philosophies, though it is often included as part of other risk management and EHS-centered systems.
The Hierarchy of Hazards
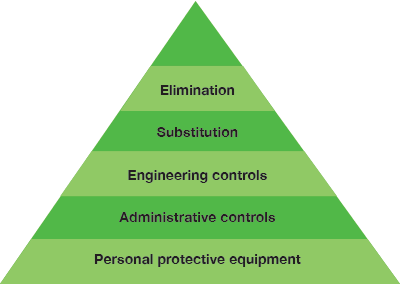
The Hierarchy of Hazards is almost always pictured as an upside-down triangle or a pyramid and occasionally depicted right-side-up. Regardless, whenever applying this methodology, it’s essential to start at the end of the triangle labeled “elimination” first and go forward from there. As the progression of elimination, substitution, engineering controls, administrative controls, and PPE moves through in that order, the effectiveness of each action is reduced. However, when used together, each of these methods packs a powerful punch.
Most occupational hazards can't be eliminated, otherwise companies would have gotten rid of them in the very beginning. The workplace is, by nature, somewhat hazardous. Now with that being said, one of the most important points regarding the use of the Hierarchy of Hazard Controls is the fact that PPE, while last on the list, is still paramount to employee safety. When a hazard exists and other options can't completely mitigate the danger, PPE can protect employees if/when a dangerous situation arises. For that reason, all plausible options must be meticulously sorted through for each step! This way all employees can be supplied with the appropriate PPE for the level of risk present.
In the end, the Hierarchy of Controls is used throughout all types of industries, and OSHA even recommends it as an important safety improvement step. To dive into this topic a little deeper, each step of NIOSH's hazard method will be covered in the following sections.
Elimination
The ideal way to address a hazard is to eliminate it, but this step can be one of the most difficult and not always possible. When exploring the possibilities of elimination try and target:
- Dangerous equipment
- Hazardous chemicals
- Unnecessary processes
Consider getting rid of the above occupational hazards if possible as they are high-risk hazards to both the employees and the facility.
Substitution
The next best option, if elimination is not possible, is to substitute the hazard with something less dangerous. Try replacing:
- Lethal chemicals with less dangerous ones.
- Old machinery for ones with new safety features.
- Current manufacturing procedures for ones that are less risky.
For example, if a fire hazard exists and can combust at just 110° F and it's possible to replace it with something that combusts at 250° F, the hazard can be dramatically reduced. While there is still a hazard, the facility and employees are much safer.
Engineering Controls
Taking steps to control the hazard is the third best option. Engineering controls work by isolating employees from the existing hazards and providing protection via accident prevention through design. This can include:
- Implementing machine guards to prevent loss of limbs.
- Designing and installing an HVAC system to improve facility ventilation.
- Using sound dampening materials to prevent hearing loss.
Take the above example of combustible material. It may be impossible to eliminate the use of that material or replace it with something less combustible. If that's the case, it may be possible to design and build a fire containment room around the area where this material is used. This way, if there was a fire, it would be confined to one area and the rest of the facility will be safe.
Administrative Controls
The next option is to use administrative controls to change the way people work. Rules and regulations must be put into place to minimize any risks that weren’t able to be eliminated, substituted, or adequately minimized with engineering controls. Administrative controls involve:
- Training employees who are around any existing hazards.
- Improving procedural work.
- Keeping up with maintenance.
- Performing regular housekeeping roles such as cleaning.
- Implementing visual safety tools to remind employees of the hazard.
When working with combustible materials, an administrative control might be prohibiting smoking in the area. While the risk is still present, administrative controls help reduce the chances of a dangerous incident occurring.
Using Multiple Hazard Controls
If a facility is unable to eliminate the hazard, it’s often a good idea to use multiple other hazard controls to maintain an effective occupational safety and health program.
For example, where combustible materials are used, a facility may be able to switch to a less combustible version of the material (substitution) and also require that it only be used in a safe room (engineering controls). The facility could further be protected by using an industrial label printer to create safety signs warning people not to bring any heat source into the room (administrative control).
And finally, any employee working in the area may be required to wear fire retardant clothing (personal protective equipment).
In this case, four of the five steps in the hierarchy of hazards are used to keep the facility safe. By applying each of these steps properly, the facility will be far safer than if only one of them were used. Determining which of the hazard controls should be used in which situations can be difficult, but a facility should work to weigh out the benefits, hazards, costs, and other factors before making a final decision.
What is a Job Hazard Analysis?
Before implementing any part of the Hierarchy of Controls, it is important to determine the risks present in a given situation. A Job Hazard Analysis, or JHA, is an excellent strategy for identifying already existing and potential hazards in the workplace. A JHA also works to identify the consequences of present risks and helps determine which steps in the hierarchy will be most effective.
A job hazard analysis must be completed by a team of people who are most familiar with the actual job in question. Typically, this will be two or three front-line employees, one supervisor, and a safety manager. Some things that must be looked for in a JHA are:
- Unsafe Shortcuts - Being aware of common shortcuts that compromise occupational safety and health will open up opportunities for improvements that promote safe behavior instead.
- Improper Equipment - Having the wrong equipment for a job can make it much more dangerous. Using a hammer to do the job of a screwdriver, for example, will result in a less secure fastening.
- Lack of Awareness - Hazards that could take employees by surprise should always be addressed. For example, imagine a ledge that is difficult to see, this is a major hazard that needs to be resolved.
Each facility is going to have a unique set of hazards, so it's important to take the time to perform JHAs and identify all risks.
Performing a JHA
Gearing up to perform a Job Hazard Analysis first begins with gathering the support from all the employees, reviewing the facility’s accident history, and conducting a preliminary job review. Once that is complete, the one performing the JHA can proceed with the following:
- Observe the Job - Break down the job into small steps.
- Identify Potential Hazards - Identify hazards that can be found in any of the job's steps.
- Assess the Severity of the Hazard - Rate each hazard based on severity. If a hazard is present, but the only risk is that someone might get a papercut, the facility won't likely want to invest a massive amount of time or money into a solution.
- Assess the Probability of it Occurring - Similar to assessing the severity, assessing the probability of a dangerous outcome is also important. Problems that have a 1 in 100 million chance may not need as close of scrutiny as something that has a 1 in 10 chance of occurring.
- Categorize Each Hazard - Order hazards according to importance. Do this by taking the severity of the hazard and the probability of it occurring and combining them. A serious hazard that has a high probability of happening is the most important to address.
Finally, once this information is collected, it is time to make recommendations for each hazard using the Hierarchy of Hazards. It is best to make initial recommendations right after the job hazard analysis is completed. This is when the specific hazards and surrounding activities will be fresh in the team's mind.
Just because a particular solution is proposed first doesn't always mean that it will be implemented. Writing down proposed solutions from the hierarchy of hazards is a good first step in determining the proper response to a given hazard and will serve as a starting point for making decisions in the future.
Ensure Effective Hazard Control
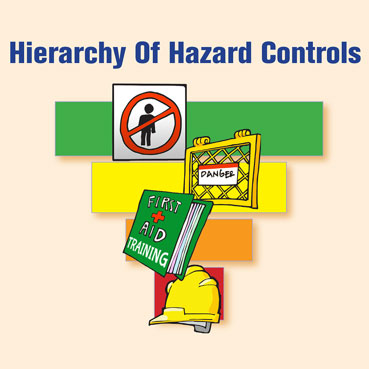
There are five simple steps when it comes to ensuring a facility has excellent control over the hazards that exist within the workplace. Those include:
- Identify who is held accountable for health and safety.
- Conduct regular maintenance to not only find problems but prevent them as well.
- Ensure that the employees are up to date on their safety training.
- Always maintain up to date hazard information.
- Regularly review this material with employees.
Knowing Each Person's Role
Whenever identifying hazards or working to implement hazard controls, everyone must know their roles and responsibilities. This will prevent miscommunications and facilitate open communication between employees and management.
- Role of Management - Management is responsible for making sure jobs are designed to be safe. This applies to all tools and equipment available to the employees, the processes and procedures in place, and all PPE provided by management.
- Role of Employees - Employees need to be on board with following the Hierarchy of Hazard Controls.They need to make sure they are using all the equipment and tools in the way they were designed and know that they are responsible for reporting any new hazards they discover.
Formalizing the Process
Even if a business already uses a safety improvement method, it’s important to have something formalized, like the Hierarchy of Hazard Controls. This will ensure each situation is reviewed properly and the right solutions are put in place to get the best possible results.