When looking for ways to improve things in the workplace, having strong problem solving skills is very important. One of the most effective options for problem solving was developed at the Ford Motor Company, and is called "Eight Disciplines" or 8D. While it was developed by Ford, it can be used in a wide range of different environments to effectively resolve many types of problems.
The 8D problem solving process isn"t as well-known as many of the other strategies out there, but awareness continues to grow as it becomes clear just how effective it can be. The 8D strategy has more steps, and is often seen to be more detailed than most other options. When done right, this can result in being able to solve problems more effectively, so they don"t recur in the future.
The following image provides a quick list of some of the most popular problem solving strategies, and compares the steps involved in each:
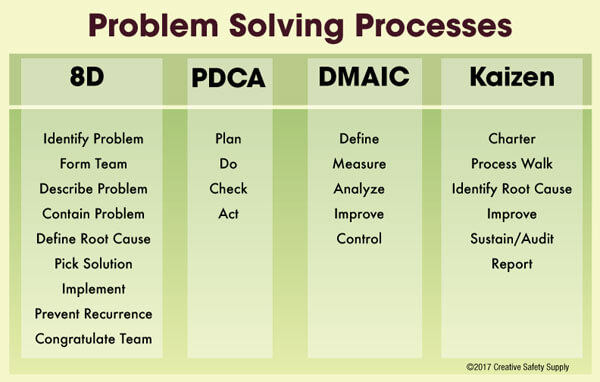
8D Problem Solving
When this system was originally created, it had eight steps, which is where the name came from. Over time, the 8D problem solving methodology has been updated with an additional step at the beginning for planning. This is considered "D0" and has made it so there are technically nine steps in this process.
When thinking about implementing the 8D problem solving concepts in the workplace, the first thing to learn is what the steps actually are:
- D0: Plan - Taking the time needed to make a plan on how to determine and solve a problem. This will include identifying prerequisites and information required to efficiently find solutions.
- D1: Use a Team - In almost all situations, having a team in place will ensure better results. Forming the team properly is critical.
- D2: Describe the Problem - Describing the problem accurately is very important. Make sure the description uses clear terms and answers questions about "who, what, when, where, why, how, and how many."
- D3: Develop Interim Containment Plan - It is often a good idea to implement an interim containment plan that may not solve the problem, but can isolate it in such a way as it doesn"t impact the customer.
- D4: Determine and Verify Root Causes and Escape Points - Identifying all the root causes of the problem, and why they weren"t noticed before. Getting to the root cause is critical for D8 problem solving.
- D5: Verify Permanent Corrections for the Problem - Through a series of tests an analysis, determine whether proposed corrective actions would result in a long term fix for the problem in question.
- D6: Define and Implement Corrective Options - Determine which proposed corrective actions will provide the desired results, and implement them.
- D7: Prevent Recurrence - Make sure all documentation, training, management, and other aspects of the facility are updated to prevent the problem from recurring.
- D8 Congratulate Main Contributors - Taking the time to acknowledge those who were involved with the problem solving process will help encourage others to get involved in the future.
Following these steps is a proven strategy for being able to identify problems, and get them solved properly. In addition to the primary benefit of being able to put in long-term fixes, this methodology also helps to ensure there is as little customer impact as possible.
The D3 step is often left out of other problem solving strategies, but it is very important. By taking temporary steps to reduce or eliminate customer impact, it will help protect the company reputation, which is very valuable. Some companies are tempted to skip that step in order to get to the root cause and solution more quickly, but that is almost always a mistake.
By eliminating the customer impact, 8D gives the problem solving team the ability to take their time to really dig into the issue and solve it properly.
Benefits of 8D Problem Solving
There are many benefits associated with using the 8D concepts to find true resolutions to problems in the workplace. To start with, the system is focused on getting to the root cause of problems, which is necessary to fix issues now, and prevent them from coming back in the future.
It is also helpful because it looks at "Escape Points" to improve the ability to detect failure should something go wrong again in the future. The prevention loop in this system helps to eliminate the conditions that allowed the failure in the first place.
To put it simply, the biggest benefits of the 8D systems is that it uses a multi-step approach to identify problems, come up with and implement solutions, and remain focused on ensuring the problem does not recur in the future. When implemented over time, this will help to dramatically reduce problems in the workplace, which will help to improve the overall bottom line.
Disadvantages of 8D Problem Solving
There are relatively few disadvantages of using the 8D problem solving concepts. The most significant one is that it will require those who participate in the problem solving efforts to receive some training on how 8D works.
In addition to learning about the actual 8D problem solving strategies, those learning this concept will also need to understand other related things. This may include things like fishbone diagrams, process maps, pareto charts, and more.
8D Template
Many companies choose to use 8D templates to help streamline the problem solving process. These templates can be printed off and used that way, or used on a computer or tablet. Having each problem documented in writing will not only make it a more tangible process for those working on the issue, it will also give organizations something to look back on should a problem recur.
8D templates can come in many forms. Many companies will create their own custom templates to ensure they can track information just how they want. Others will use pre-made options from a variety of suppliers.
8D Report
8D reports, like 8D templates, can be useful tools to get through a problem solving process. These reports are used within a facility to explain what 8D is, including information about each step, so that those attempting to solve problems will know what they need to be doing.
The term 8D report can also refer to a report generated by the problem solving team after a problem has been solved. The report can be pulled and looked at in the future should the same, or a similar, issue surface. Keeping these reports readily available can help to avoid having to repeat work on the same problems over and over again.
Reports should be as detailed as possible, and include information on each step within the 8D process. When completing a report, those working on the problem should attempt to provide enough information so if someone who was not on the current 8D team pulls it out, they will understand what the problem was, and what solutions were put in place.
8D Methodology
The 8D methodology can seem complex or confusing at first, but after being properly trained, it becomes clear. It builds on many other well-known problem solving processes such as the DMAIC, and PDCA concepts.
In addition, the 8D methodology fits right in with Lean and Six Sigma concepts. Being able to integrate 8D into these other systems will help to minimize the amount of training that is needed, and also help to make those strategies more effective. While it can certainly be used on its own, combining it with other workplace improvement concepts is very common and very helpful for the company as a whole.
Putting in the needed effort to understand how 8D works, and why this methodology is worth the effort is important for any company. This methodology is often implemented by higher level managers due to the fact that it can be intimidating at first, but when done correctly, will help to better find the root cause to a problem and get it fixed permanently.
Continuous Training for 8D Problem Solving
After the employees who are engaged in 8D problem solving have had their initial training so they understand what 8D is and how to do it, they will want to continue working to learn more. Going through the 8D process on real problems can be seen as a form of continuous training since each problem will be unique, and provide them with opportunities to learn more and refine their knowledge.
There are also options for training on 8D itself, as well as concepts used within 8D. There are many different problem solving concepts out there, and helping employees to learn each of them will allow further improve their ability to go through the 8D problem solving process.
Keep in mind that other than the basic introduction to what 8D is and how it works, people can begin using this problem solving process without extensive training. Over time, they can be given additional training and experience to help improve skills and benefit the team as a whole.