As the COVID-19 pandemic continues to make an impact around the world, the main concern is how to stay safe in the workplace. Safety is absolutely the priority—as it was before the pandemic. However, it’s important to keep efficiency in mind as you adapt your business operations to changing public health requirements that are meant to slow the spread of disease. Even if all your employees are working from home, the current crisis presents an opportunity to implement Lean manufacturing techniques and focus on efficiency strategies.
The Toyota Production System, which originally developed the methodology behind Lean manufacturing, was created partly in response to the struggles that Japan’s industry experienced after World War II. Toyota had to find a way to establish new and better ways to work, while also revitalizing the community and securing positive employee morale. This makes Lean the perfect technique to help your company adapt to the pandemic.
Not only can Lean methodologies help ensure your business continues to operate successfully, they can also help reduce the spread of disease and provide a comfortable, safe workplace. Lean incorporates organization and cleanliness as it streamlines operations. Due to a visual management system, Lean makes it easy for workers to instantly see “out-of-standard” problems or conditions—which is essential during a public health emergency. As time goes on, implementing Lean may prove to be more important than ever.
The Importance of Lean Manufacturing During COVID-19
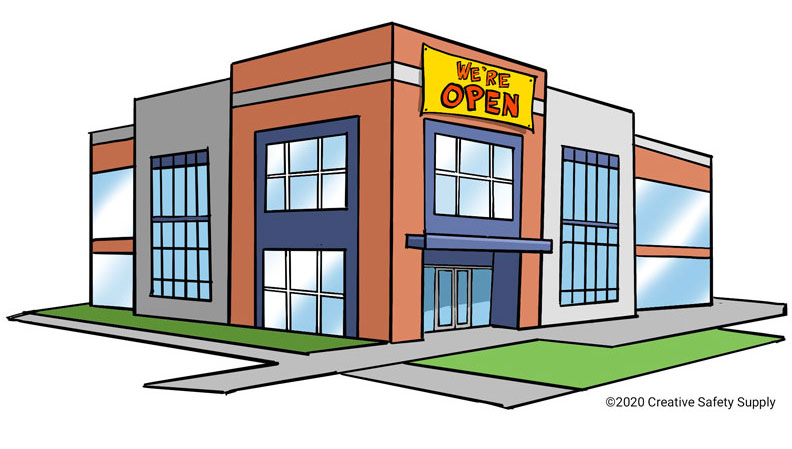
Some manufacturers have not shut down or faced layoffs during the pandemic—instead, they’ve actually increased production. Food suppliers have needed to boost operations in response to panic-buying at grocery stores, and other companies have stopped producing their traditional products to instead create hand sanitizer, ventilators, or face shields. Pharmaceutical companies are also working harder than ever in the race for a COVID-19 vaccine.
For other manufacturers, however, they are emerging out of lockdown and bracing for the many challenges that lie ahead. Businesses must revise their demand forecasts, provide different services, and adopt new work practices. It’s beneficial, however, to see this time as an opportunity, one in which you can implement Lean manufacturing techniques alongside all the other changes you are likely going to have to make, no matter your industry.
It’s ample time for all manufacturers to reevaluate their strategies and make improvements. Companies that already suffered from low productivity, waste, and inefficiency before the pandemic will likely continue to struggle the most. More than anything, COVID-19 has shown how important it is to practice innovation and resilience. To ensure long-term survival, many businesses are focusing on their productivity and performance, reducing errors, and utilizing available resources as much as possible.
Establishing a Consistent Cleaning Routine with 5S
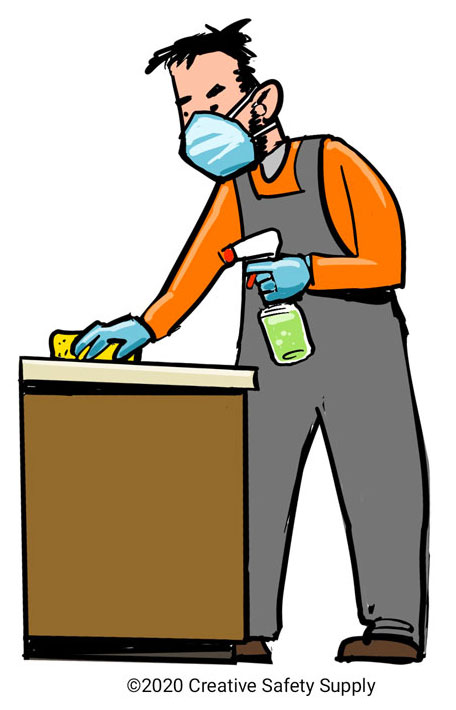
One of the new work practices that every company must now implement is a consistent cleaning and disinfecting routine. By constantly cleaning high-touch shared surfaces and personal workstations, employees can help reduce the possibility for transmission of disease in the workplace. 5S is an effective Lean manufacturing methodology that makes it easy to maintain this type of cleaning routine, which relies on individual effort. 5S enhances overall improvement through five steps: Sort, Set in Order, Shine, Standardize, and Sustain.
By implementing a 5S program in your company, you’ll train workers on how to effectively perform the Shine step, in which they completely clean their workstations and organize equipment or tools as an aspect to their daily asks. With 5S, workers understand what to clean, how to effectively clean it, where cleaning materials are stored, and how to use them safely.
Once you’ve established a cleaning schedule, 5S also aids in maintaining this schedule for the long term with its last step: Sustain. The key to success and safety as the pandemic continues is diligence. Establishing a routine and upholding that routine is a necessary Lean aspect to keeping workers healthy in your facility.
Gemba Walks and Respect For Workers
During the pandemic, continually checking in with your team members and having an understanding of frontline operations is more important than ever. Gemba, another Lean technique, means “go and see” and requires supervisors or managers to observe the actual place where operations are conducted to identify areas for improvement. This also provides an opportunity to speak with frontline workers. Team leaders can incorporate Gemba by:
- Checking in on a consistent basis and holding team meetings or huddles. This can be done remotely if employees are teleworking, through video conferences.
- Monitoring the situation carefully to ensure team members are being treated fairly and respectfully.
- Encouraging employees to share new ideas or to discuss problems that may come from conditions impacted by COVID-19.
- Making sure that communication continues to be strong and that guidance and leadership continue to be aligned.
A major aspect to Gemba is treating people with respect. Each team member should be treated politely and respectfully, especially in times of stress or crisis. Physical safety is highly important for employees, but their psychological safety is important as well.
Aiming for Continuous Improvement
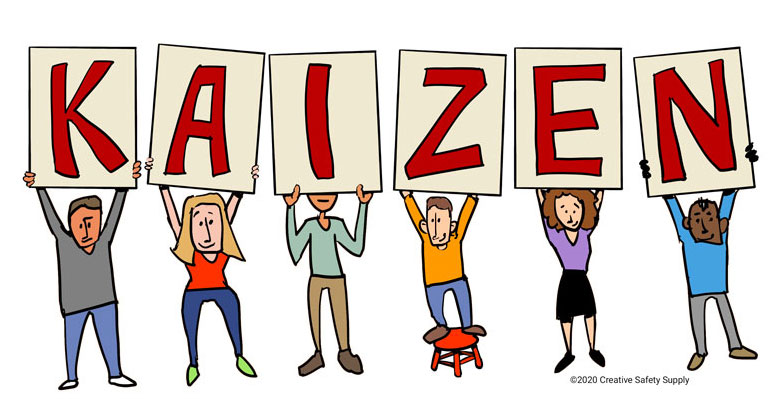
Kaizen is a foundational Lean philosophy that translates to “changes for the better.” By incorporating a culture of continuous improvement in your workplace during the pandemic, you can improve communication, create more efficient processes, improve employee morale, and ensure cleaner, safer workspaces.
It can be difficult to adapt to a Kaizen mindset, but successfully practicing continuous improvement is possible by cultivating a supportive culture that contains the five core elements of Kaizen:
- Teamwork. Ensuring the success of the business and reducing the spread of COVID-19 requires everyone to work together. Each employee must strive for a common goal.
- Suggestions for improvement. With Kaizen, every employee is trained to identify waste and look for opportunities for improvement. Everyone should feel comfortable to either suggest these opportunities to their team or to implement improvement themselves.
- Quality circles, which are regular team meetings of about a half a dozen employees. During these meetings, workers are welcome to discuss any issues or problems they have encountered in the work process.
- Improved morale. When workers are empowered to improve their job or their tasks, they are more satisfied with their work. As the pandemic continues, it’s highly important to ensure that your workers are satisfied.
- Personal discipline, as each employee is responsible for their own time management and should continually strive for high quality effort.
Improving with the PDCA Cycle
PDCA stands for “Plan, Do, Check, Act,” and it is an integral aspect to the concept of Kaizen. Implementing the PDCA cycle helps you observe operations, make plans for improvement, see if those improvements do indeed happen, and then act upon failure or success.
PDCA works well for both on-site and remote teams; if your employees are teleworking, use PDCA continuously to ensure workers have the resources they need to complete their tasks successfully. As more information on COVID-19 and community transmission is discovered, PDCA can also be used to make changes in your organization to ensure you are in compliance with ever-changing government regulations.
What You Can Do During a Pandemic
In varying ways, the COVID-19 pandemic is impacting every single business across the globe. To survive this event, many businesses are pivoting the way they offer their products and services to adapt or help out their local communities. Using Lean manufacturing techniques, you can identify what your customers need the most right now and consider new ways to efficiently match those needs. Since many work practices and safety standards are changing, it’s perfect timing to implement Lean methodologies such as 5S and Kaizen to ensure your workplace is clean and that new policies are making a positive impact.
Even during times of crisis, efficiency is important. Lean manufacturing techniques were created from a need to increase efficiency, boost morale, and support the community. Whether your business is reopening or your employees continue to telework, the pandemic requires us all to innovate and adapt. Use Lean to ensure long-term success.
Similar Articles
- Kaizen (Lean Continuous Improvement)
- Cleaning the Workplace During COVID-19
- Lean Safety | Understanding the Lean 6S Methodology
- What is Toyota Lean Management?
- Toyota Production System (TPS & Lean Manufacturing)
- Understanding the Principles of Lean Construction
- Lean Thinking: The Foundation Of Lean Practice
- Lean Manufacturing [Techniques, Solutions & Free Guide]
- 5 Lean Principles for Process Improvement