Design for Lean Six Sigma
Design for Six Sigma (DFSS) is a methodology of improvement that helps businesses create new products or services at a high level of quality. The technique aims to meet the needs of customers and utilize the company’s capability as much as possible during the original development of a process. This reduces the need to redesign and reintroduce a product multiple times, which creates excessive waste.
The main objective of DFSS is to design things right the first time with minimized defects or variations. Rather than the traditional Six Sigma method of improving an existing product or process to reduce defects, DFSS utilizes the five stages of Define, Measure, Analyze, Design, Verify (also known as DMADV) to determine the needs of customers and then design a solution to meet those needs. Additional work is conducted up front to ensure the company has a full grasp of its customers’ needs and expectations, which requires an extensive amount of data and analyzation.
History of Design for Six Sigma
The evolution of DFSS methodology began in the 1980’s, when Motorola hired Bill Smith and Dr. Mikel J. Harry to improve its quality control. Building upon improvement theories that were developed by quality professionals such as W. Edward Deming, Smith and Harry introduced the methodology of Six Sigma. This statistics-based approach aims to reduce the number of defects to less than 3.4 per million, controlling quality and achieving near perfection.
Once introduced, Six Sigma helped businesses analyze data to measure success and identify opportunities for improvement. While it had a large and beneficial influence, it was soon realized that not every process can be fixed with the traditional Six Sigma approach, as some things need to be completely redesigned rather than simply improved. Over time, DFSS was created as a variation of Six Sigma intended to help businesses develop new products and services that were designed to fulfill customer requirements as soon as they were introduced to the market.
The 5 Phases of a Project
The DMADV approach is widely used to implement new products or processes. It’s especially beneficial for supply chain operations due to its basis in data and comprehensive analysis, and the ability it provides to determine success early on. The five phases of a Design for Six Sigma project are as follows:
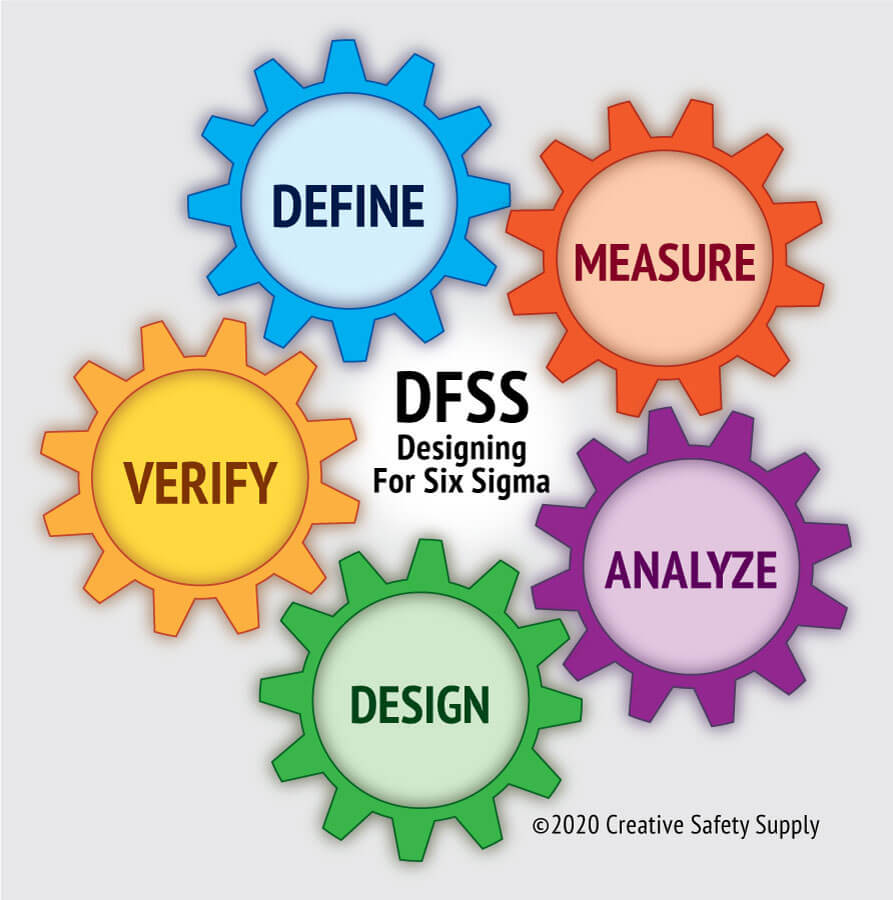
- Define. This initial phase determines everything from the project’s purpose, schedule, and budget to how the results will be communicated. It also details any risks associated and establishes quantifiable goals.
- Measure. During this phase, customer expectations and needs are translated into quantifiable design requirements. Methods such as surveys, site visits, and consumer focus groups are utilized to obtain customer information.
- Analyze. Once the design requirements are established, multiple designs are created. Assessment tools evaluate how well each concept meets customer needs and its potential for success.
- Design. The best design is selected, and detailed production work begins. The technology required, materials, manufacturing process and location, risks, and packaging are all evaluated through analysis tools and computer simulation. This phase is finished once a final design has been decided upon and a validation plan is developed.
- Verify. Validation testing is conducted to assess whether the design does actually meet performance and customer requirements. Often, a prototype or pilot build is created before the actual product launch. Whether the design is successful or not, project documentation is completed and results are shared.
DFSS v. DMAIC v. DMADV
DFSS/DMADV
Design for Six Sigma is also known as DMADV. The DMADV approach is a variation on the traditional Six Sigma method, but shares the end goal of reducing defects and helping a company provide high quality products that fulfill customer needs. Rather than improving an existing process, DMADV designs an original one, then verifies whether it is successful.
DMAIC
Define, Measure, Analyze, Improve, Control (DMAIC) is a method used during traditional Six Sigma, where an existing product or service within supply chain operations is redesigned. It is most effective when a current product needs to be remodeled to match fluctuating customer needs.The first three steps to this method are the same as DMADV, with two major differences toward the end:
- Improve. After customer and design requirements are analyzed, companies use this data to develop a plan in order to improve a current product. Successful improvement can be achieved through various techniques such as poka yoke (mistake proofing) to establish new process capabilities.
- Control. Thisis the last step as a means to sustain the achievements gained in the first four phases. It ensures that there are no future potentials for defects in the process.
When is it best to use DFSS instead of DMAIC? First, consider whether the product has already been implemented, or if it is going to be introduced for the first time. DMAIC should be used for processes that a company already has in effect. For example, DMAIC can help a company that makes phones evaluate the types of updates its newest version requires in order to stay competitive in the cellphone market.
The DMADV approach should be used for products and services that are not currently in existence. It is also ideal to use DMADV if you would like to create a product that fully meets customer expectations, want to initially provide a product of high quality, or are interested in being more likely to achieve success on the first attempt. A company that is introducing its first cellphone can utilize DMADV to develop a phone that meets customer’s needs right off the bat. DMADV is widely used in other variations, including DMADOV, which contains the additional step “Optimization,” and IDOV, which is Identify, Design, Optimize, Verify.
No matter the methodology that is used, Six Sigma ultimately focuses on understanding the needs of customers and applying this knowledge to the design of products and processes.
Design for Six Sigma Tools
A major aspect to Design for Six Sigma is identifying an improvement to make, which begins with identifying the core problem. Many companies conduct a root cause analysis and use fishbone diagrams or the 5 Whys to determine these underlying issues, but there are a variety of tools you may use to aid your organization’s DFSS methodology, including:
- Critical to Quality (CTQ) Trees. CTQs are the parameters required for a product to be considered satisfactory. Trees, or diagrams, break these parameters down into crucial needs, quality drivers, and performance requirements. Once these requirements are determined, they can be implemented into the design process.
- Control charts, which are a statistical tool used to determine if a process is in a “state of control”. These charts detect and fix discrepancies in a timely manner, as high variation results in higher quality costs. Many businesses use control charts during DMAIC, as it helps them decide whether they need to start a process improvement project.
- Pareto charts, which help businesses prioritize the core causes behind quality problems and focus on a few select changes that will truly make a difference. These charts are based on Pareto’s 80-20 principle: 80% of problems arise as a result of just 20% of causes.
- Kaizen events, also known as a “Kaizen Blitz.” During these short-term events, employees focus on evaluating and implementing an improvement for a specific issue, typically within one work week.
- Failure Modes and Effects Analysis (FMEA). FMEA is particularly helpful for Six Sigma. Failure modes are the ways a process may go wrong, and an effects analysis involves analyzing the consequences of these failures. FMEA predicts risks by evaluating their severity, occurrence, and detection, and producing a risk priority number (RPN).
- Gage R&R, a measurement system used to ensure that data is accurate and determines the amount of variation that is considered to be acceptable. The goal is to have a variance of the lowest number possible, typically less than 10%.
- SIPOC diagrams, which are most helpful with the “Define” stage. These diagrams are a process improvement tool that identifies all the elements of a process, including suppliers, inputs, outputs, and customers, before an improvement project begins. It ensures everyone has a fundamental understanding of the process.
How to Implement DFSS
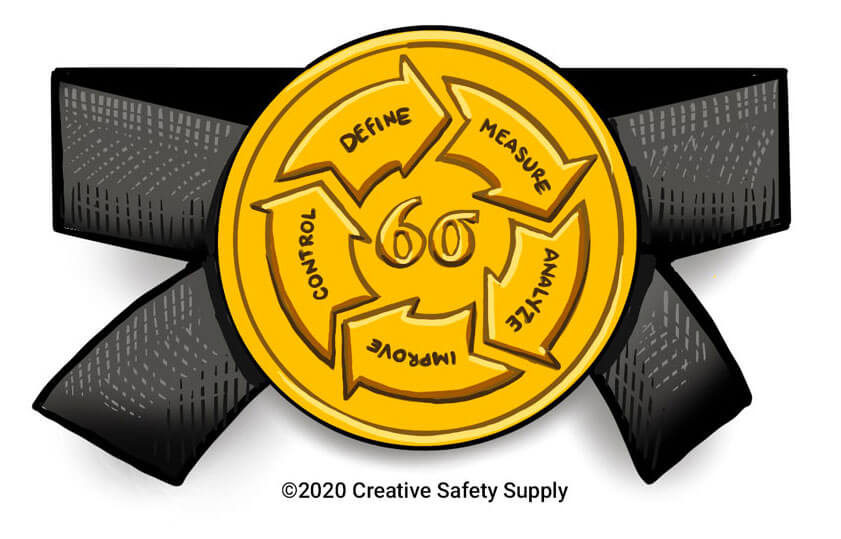
Design for Six Sigma is incorporated into operations by individuals who have been certified through a specific Six Sigma training program and regarded as experts on the matter. These individuals may be internal employees or hired externally. Six Sigma programs award certifications for different levels of training, which are identified by colored belts: White, Yellow, Green, Black, and Master Black Belt. It takes years to achieve a Master Black Belt. Design for Six Sigma is typically executed by employees who have obtained a Green Belt or Black Belt, and overseen by someone who has a Master Black Belt.
Design for Six Sigma Training
DFSS certification focuses on specifically teaching the DMADV approach rather than the traditional framework of DMAIC, which improves existing processes. If a new product needs to be designed for quality and the situation requires more than just a simple improvement, this is when individuals with DFSS certification come into play.
These individuals understand when you would implement a DFSS methodology versus a DMAIC approach. They also have a comprehensive understanding of how to use various Design for Six Sigma tools. On top of defining, measuring, and analyzing, they help guide a company through the Design and Verify stages to introduce high quality products. Overall, an individual with Design for Six Sigma training can ensure that this beneficial methodology ultimately becomes part of the company’s culture.
Additional DFSS facts:
- Design for Six Sigma (DFSS) is a collection of best-practices for the development of new products and processes. It is sometimes deployed as an engineering design process or business process management method. Source: https://en.wikipedia.org/wiki/Design_for_Six_Sigma
- DFSS originated at General Electric to build on the success they had with traditional Six Sigma; but instead of process improvement, DFSS was made to target new product development. It is used in many industries, like finance, marketing, basic engineering, process industries, waste management, and electronics. Source: https://en.wikipedia.org/wiki/Design_for_Six_Sigma
- DFSS has multiple methodologies that can be utilized, such as DMADV, IDOV, DCCDI, etc. What all the methodologies have in common is that they all focus on fully understanding the needs of the customer and applying this information to the product and process design. Source: https://quality-one.com/dfss/
- The goal of DFSS is to design products and processes while minimizing defects and variations at their roots. The expectation for a process developed using DFSS is reportedly 4.5 sigma or greater. Source: https://en.wikipedia.org/wiki/Design_for_Six_Sigma
- DFSS helps businesses design products, processes and services that are safe, reliable and competitive. Design teams can use DFSS to develop innovative solutions that meet or exceed customer expectations. Source: https://www.villanovau.com/articles/six-sigma/design-for-six-sigma/