Working as an engineer at Motorola, Bill Smith was the first to conceptualize Six Sigma back in 1986. The name “Six Sigma” originates from statistics, directly referring to the Greek letter “σ” that represents the standard deviation, which is the amount something deviates from what it should be ideally. With that being said, Six Sigma aims to have six standard deviations between the mean and the nearest specification limit. To be specific, this methodology aims to have fewer than 3.4 defects per million opportunities.
While Six Sigma began in manufacturing, today it can be used in virtually any industry across the world. Various techniques and tools that are used for process improvement and eliminating defects sit at the core of Six Sigma since the methodology puts its primary focus on measuring quality and aiming for absolute perfection. The methodology puts systems in place to primarily collect data and measure the business’ success so they can try to reduce defects and variations in processes through quality improvement projects. Doing so improves quality and customer experience, ultimately making a business more successful.
What is Six Sigma?
There are five laws that Six Sigma operates on. Those who understand the definition and principles of each and know follow them correctly have the opportunity to not only attain consistency, but also obtain an amount of quality that was not present before the implementation of Six Sigma. The main body of those five laws include the following:
- The market law– Six Sigma stresses that the business needs to focus on customer satisfaction to be able to procure quality products. One way that this strategy does this is by using Voice of the Customer to gather information referred to as Critical to Quality, or CTQ. CTQ is what determines the rate of success a company has with their product/process.
- The flexibility law – Businesses must become flexible when using Six Sigma. This increases the success in meeting delivery requirements and the expectations of the customer. Demands are constantly changing within manufacturing facilities which often creates downtime if the right precautions are not taken.
- The focus law- The focus here is to reduce the amount of resource expenditure on activities that do not add value to the product. Remedying this problem will theoretically improve the cost to efficiency ratio in a way that benefits the user.
- The velocity law – The key ideas for this rule are to keep works in progress numbers low within Six Sigma programs. This way the product is able to be finished faster which directly translates into getting to the customer sooner. Six Sigma can help reduce bottlenecks in the production line by working closely in tandem with Kanban.
- The complexity and cost law - Too much complexity in a service translates to too much money and too much time. By finding the happy medium between cost and complexity, the business will not only have a variety of choices to meet customer requirements, but they will also have a much easier time keeping up with demand and saving on the cost of resources by choosing to make an investment into the right areas.
Six Sigma is not just one new idea used to drive process improvements. Instead, it takes many other concepts and methods and combines them into a single comprehensive program. Some of the best-known philosophies included in the program are:
- 80-20 Principal
- Quality from Customer Perspective
- Quality Trilogy Model
- Plan – Do – Check – Act (PDCA)
- Cause & Effect
- Effects of External Disturbance
- Define, Measure, Analyze, Improve & Control (DMAIC)
Six Sigma is truly unique in this respect as the program can be tailored into something that has a purpose within different business models. The end goal of being as efficient and precise as possible is the same for all companies that use Six Sigma, but the pathway to those project goals are different for everyone and define the outcomes.
Six Sigma Project Methodologies
Six Sigma projects primarily follow two project methodologies inspired by Deming's renowned “Plan-Do-Check-Act” Cycle. Each methodology is made up of five phases and is represented by the acronyms DMAIC and DMADV. It may help to know that DMAIC is used mainly for projects aimed at improving existing manufacturing processes while the difference between DMADV, on the other hand, is used for projects aimed at creating new product or process designs.
Each of the acronyms are described briefly below:
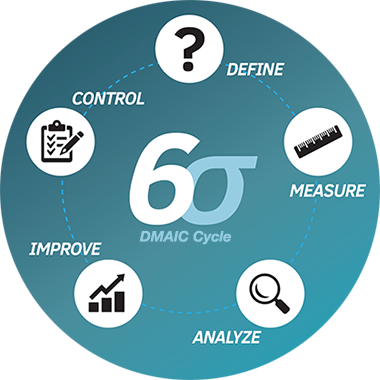
DMAIC
- Define – Define the problem at hand from both customer and process perspective.
- Measure – Measure the current process and collect relevant data.
- Analyze – Turn the data collected into knowledge in an attempt to determine the relationship between the problem and a solution.
- Improve – Based on the data collected and the data analysis, decisions should be made surrounding how the problem should then be tackled so as to improve the whole process.
- Control – Controlling the future state of the process to prevent any deviation from the target will ensure the process control remains on course.
DMADV
- Define –Define the design goal to meet the customers’ needs and manufacturing process.
- Measure – This involves identifying risks, production process capability, and product capabilities.
- Analyze - After creating the designs, each of them is to be analyzed. The best possible one is to be picked for implementation.
- Design - Once a design is chosen, it is necessary to optimize it while planning for the next phase. This step may require simulations using certain software or prototypse.
- Verify - The design, setup pilot runs, and implementation of the production process should be handed over to the process owners.
Both of these options do well in environments that place focus on Six Sigma. With that being said, it is important to have plans such as these that incrementally work on reaching the company’s goals for them to not only come to fruition, but also to be successful through the implementation of improved business processes. Quality management is everything, and reaching that status takes meticulous planning.
Six Sigma Guide: Improve efficiency with effective quality control
When corporations are plagued with defects, processes slow down. Six Sigma aims to decrease the chances of deviations to 3.4 defects per million production cycles. This Six Sigma Guide explains the steps of a Six Sigma, how to get Six-Sigma certified, and what tools you’ll need to make Six Sigma a success.
Six Sigma Certification
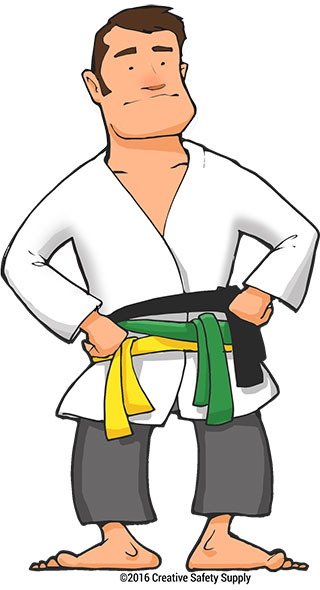
The Six Sigma program recognizes individuals based on their education and experience using the aforementioned methodologies. Similar to martial arts, there are formal levels within the program that are identified by different colored belts. Students must attain certain certifications in order to attain these belts which reflect on their development. The different colored belts include white, yellow, green, black, and master black belts.
Six Sigma White Belt
The Six Sigma white belt is given to an entry level individual. This person needs to have a good understanding of the methodology and possibly have some experience acting as support in a Six Sigma environment as a team member. In a traditional Six Sigma organization, a white belt will have an understanding of all of the following aspects of Six Sigma:
- An understanding of what the company’s customers need
- How to go about defining a project
- How to measure the performance of an ongoing project
- How to identify successful solutions
- How to reduce waste to increase the rate of customer approval
- Have an understanding of the DAMIC and DMADV processes
- How to sustain recently made improvements
This belt is most appropriate for individuals that are either interested in implementing Six Sigma into their facility program and also want to learn more about each productivity tool and performance improvement.
Six Sigma Yellow Belt
Yellow belts are front line employees who have been properly trained in the concepts behind Six Sigma. They will not lead any projects but will be involved with them as workers or contributors. Many people will seek the yellow belt as a way to determine if they would like to continue their studies to pursue a green belt or higher.
A yellow belt certification requires that the individual have one full year of work experience in a full time and paid role within a company. Unfortunately, paid internships or education waivers cannot be applied to complete this requirement as Six Sigma certification revolves around hands-on experience.
Six Sigma Green Belt
Six Sigma green belts are certified individuals that work on projects for up to 25% of their typical workday. They usually function as team members on projects being run by black belts, though they can operate as a project leader on small or simple projects. Green belt certified employees typically get most of the work done on a given project.
When working as a team member, the green belts coordinate with the leader to ensure the entire team is functioning and the project is progressing. They may also collect data about projects and potential projects to supply to black belts or champions.
When a green belt functions as a project leader, he or she will also have the following responsibilities:
- Refine the project’s goals
- Work with the project’s champion to create & refine the charter
- Choose team members
- Communicate with the champion and other leaders
- Facilitate communication within the team
- Analyze data
- Coordinate meetings and other logistical tasks
- Train team members when necessary
To achieve a green belt status, the individual must hold excellent leadership skills, have a knack for being logical and analytical, be constantly working on improvement, and show perseverance when faced with difficult problems; often having earnt a higher salary for their responsibilities.
Six Sigma Black Belt
Black belts spend 100% of their day working on improvements and project implentation for their companies and are an expert in their field. Only a select number of green belts will ever make it to the black belt level due to the high standards and level of commitment entailed, and those who do should meet the following criteria:
- Managerial skills
- A love for statistics
- Excellent leadership skills
- Understanding of process improvement methods
- Excellentwriting skills
- Works well as part of a team
- Able to facilitate meetings
- Comfortable working with upper management
Each facility should evaluate its needs and determine whether someone can meet the requirements of a black belt. In some organizations there is just one black belt certified individual, and in these cases he or she must be an expert in all areas in order to make a return. In other companies, there may be multiple black belts, so the excellence can be spread around.
When leading a project, a black belt needs to be able to perform the following tasks:
- Create a project charter
- Work closely with the project champion
- Work closely with process owners
- Lead the team infrastructure
- Schedule and lead meetings
- Assist team members where needed
- Offer training where needed
- Recommend Six Sigma projects
- Coach green belts, only if there is no master black belt
Black belts should have a mentor who has obtained a master black belt. Ideally this will be someone within the same organization. If that is not possible, they can work with people from other companies.
Six Sigma Master Black Belt
Becoming a Six Sigma master black belt takes several years of courses, study, exams, experience, practice, project work, and more. Master black belts also need to be mentored by existing master black belts in order to attain this level. In most companies, a master black belt fulfills the following roles:
- Provides advice to senior executives concerning Six Sigma
- Prioritizes projects based on company initiatives
- Execution, analysis, innovation, and improvements of the Six Sigma process
- Provides mentorship to black belts and green belts
- Offers training to those pursuing Six Sigma certifications
Organizations that have Six Sigma master black belts usually have them manage all the Six Sigma processes within the company. These individuals work closely with the CEO, executive management and area leadership to develop and implement projects, which are typically led by a black belt.
Key Process Improvement Terms
Everyone in a Six Sigma facility should have at least a basic understanding of common words and terms used in this system. While it is ideal to have everyone at least yellow belt certified, it could suffice to provide very simple training to get things started. The following are some key Six Sigma process improvement terms that everyone across the teams should put emphasis on:
- Critical to Quality – This is a term that describes attributes that are most important to the customer.
- Defect – Any errors resulting in failure to deliver what the customers desire.
- Process capability – The maximum that your processes can deliver.
- Process Variation – Any change felt or seen by customers.
- Stable operations – The ability to deliver consistent, predictable results and follow standard processes to achieve a high level of accuracy.
- Design for Six Sigma – The concept of designing items or services specifically to meet customer expectations and the company’s process capability.
Having a basic understanding of these disciplines will help everyone on the Six Sigma team have a clear understanding of the company’s objectives and help to pave a pathway to facility an improvement result.
What is Lean Six Sigma?
Lean Six Sigma is a combination of both Lean manufacturing and the standard Six Sigma method. By combining both methodologies, the user will be able to reduce variation in product while also working to eliminate the eight wastes of Lean. The eight wastes of Lean include defects, over-production, waiting, non-utilized talent, transportation, inventory, motion, and extra processing.
Companies that implement Lean Six Sigma will benefit from the following:
- Saving on production costs
- Improving the quality of the product
- Becoming more efficient and consistent with production
- An increase in customer value
- An increase in profits
The choice to make the shift over to Lean Six Sigma is an easy one, but implementation and overall success depends on factors such as if the company has done their due diligence regarding designing, planning, and organization approach to get the program up and running and sustaining the new program into the future. To get that done, they need to have a plethora of tools at their feet to get things done.
Lean manufacturing – Here the company’s arsenal of organizational tools can include, but is not limited to, Kaizen, Value Stream Mapping, 5S, Kanban, PM, and Visual management.
Six Sigma – Some of the more prominent tools that companies use for Six Sigma include PDCA, DAMIC, DMADV. There are others listed above in this article as well.
The nice thing about Lean Six Sigma is that it combines two completely different methodologies that end up working well to keep each other in check while also involving some of the most useful strategies a company can use to continually improve their facility productions.
Six Sigma Facts
The Six Sigma method is well established across the globe and has proven to be effective in many industries, offering competitve advantage. Learning a key fact or two about the system and its history can help people see just how powerful this methodology can be for a company and how helpful certification can be for an individual if they are looking to get higher up the hierarchy.
- Management-level business experts choose Six Sigma professionals over those with MBAs or Project Management certifications alone.
- By 2005, Motorola had credited Six Sigma with more than $17 billion in savings in the U.S. alone.
- Today many companies are combining Six Sigma with Lean methodologies, creating Lean Six Sigma. Lean tries to eliminate waste and increase efficiencies, while Six Sigma tries to eliminate defects and reduce variability. These methodologies often work well together for many businesses.
Whether a company already uses Six Sigma or is hoping to implement its features for the first time, one of the best things any individual can do is get a Six Sigma certification. These certifications not only benefit the company that employs these individuals, but also provide major career benefits to the individuals themselves on a long term basis.
When a facility begins using the application of Six Sigma seriously, it is a good idea to bring in a master black belt, or at least a black belt, to ensure the system is managed properly. As with any type of process improvement program, if it is not run properly from the top down, it could cause more harm than good. While it will take some effort, proper implementation can revolutionize a company.
Similar Articles
- Six Sigma Belt Levels [Hierarchy of Certification]
- Six Sigma Certification
- What is DFSS (Six Sigma)?
- Six Sigma Black Belt
- Six Sigma Green Belt
- Six Sigma Principles
- Lean versus Six Sigma: Which is better for your business?
- Understanding the SIPOC Diagram in Six Sigma
- Control Charts: A Basic Component of Six Sigma