5S is an effective way to manage workplace organization in almost any environment. The philosophy is part of the Lean manufacturing methodology and relies on simplicity and making everything work the way it should. The 5S concept was developed and pioneered by the Toyota Motor Company in Japan, with much of the innovation coming from Hiroyuki Hirano.
The concepts behind the 5S system can be used in any workplace environment including manufacturing, medical, technical, repair facilities and more. With some simple adjustments, any company can successfully implement and benefit from the 5S concepts.
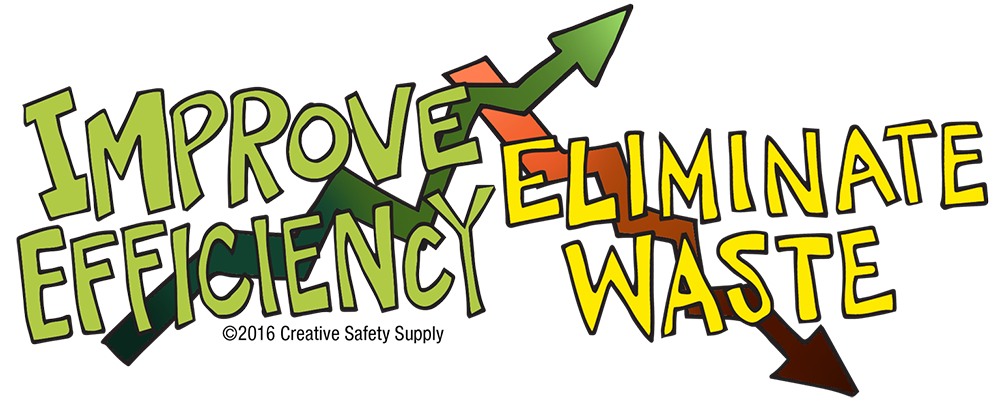
The 5S's that Lead to Success
This system gets its name from the five main concepts, or pillars, of the system. Each of these pillars starts with the letter S.
- Seiri (Sort in English) - This concept encourages a facility to eliminate all unnecessary items in the work environment so only useful things are present. Anything that is not immediately needed should be properly stored away.
- Seiton (Set in Order) - Here you will need to arrange things properly so each item that is needed can be accessed quickly and easily.
- Seiso (Shine) - Shine implies that things are kept clean. Included in this pillar of 5S is making sure all equipment is in proper working order.
- Seiketsu (Standardize) - Creating routines for accomplishing tasks can ensure things are done properly and efficiently every time.
- Shitsuke (Sustain) - Making an effort to develop a culture that follows the 5S steps both today and long into the future.
Looking Deeper into the 5 S's
When implementing 5S into any environment it is essential to have a deep understanding of each of the five main pillars. Look at the following examples of each to help you begin the journey of mastering the 5S methodology.
- Sorting - Go through your working environment and carefully review every item you come across. Ask yourself what purpose it is serving. If you find that it is not directly needed in that area, find the proper storage area and put it away. If there is no set storage area, create one that makes sense based on the use of that specific item.
- Set in Order - All the items or equipment required for a job should be placed in the ideal location so they can be accessed as quickly and easily as possible. A hammer, for example, should always be within arm's length of the person who will be using it. Similarly, someone loading parts into a machine should not have to walk any distance to get the necessary parts.
- Shine - This is the easiest to understand, and most often overlooked, of the 5S pillars. Keeping things clean and in proper working order go hand in hand. Maintaining all the tools and equipment used in any facility will eliminate downtime and keep things moving efficiently. Properly cleaned and maintained things also last longer without requiring repair or replacement.
- Standardizing - Whenever performing any type of task multiple times, identify the most efficient way to complete that task and create a standard. Facilities often have different processes on different shifts. This means that at least two of the shifts are performing the work in a less than optimal manor. Standardizing the processes will help avoid mistakes and improve efficiency.
- Sustain - It is easy to have a facility buy into the 5S concepts at first, but over time people and departments develop bad habits. In order to maintain the benefits of the first four pillars listed above, it is essential to think about how to sustain the improvements that are made. Performing audits of the new systems, for example, can be very effective.
Choosing the 5S System
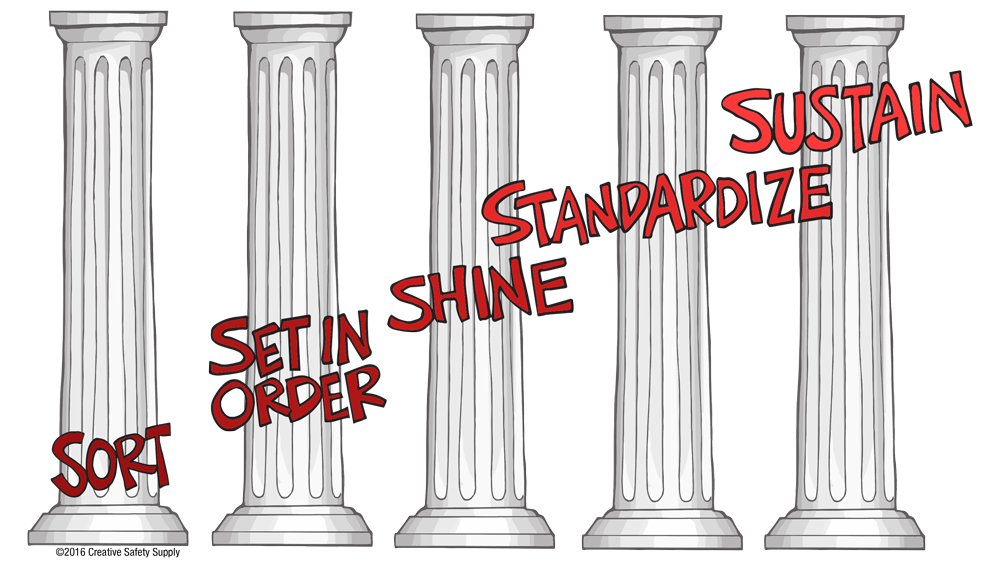
The 5S system has been developed and evaluated by companies around the world. It is a proven way to improve efficiency and eliminate waste in almost any work environment. Learning as much as you can about this system will help to ensure your workplace gets all the benefits of this system without any trouble.
How to Implement the 5S System
Some people will have trouble getting approval for the time or money needed to fully implement a 5S system. One nice thing about this methodology is that you can implement it one step at a time. Using a generic manufacturing facility as an example, let's look at some simple examples of how you can implement each of the 5S's into your daily work environment.
- Sorting - Choose one department in your facility and identify every item that is not physically bolted down or otherwise unmovable. Every one of these items should be identified and put into the place where it belongs. If it is not immediately needed for daily tasks, put it away in a storage closet or other area.
- Set in Order - Once any items that are not going to be used are put away in the storage areas, it is time to take all the remaining things and find where they should go. Find the location where it will be easiest to get by the workers exactly when it is needed. Another thing to accomplish during this step is to locate items that are needed but not currently found in that work area. Bring these things closer so they are available when required.
- Shine - Obviously this step involves cleaning work areas and keeping equipment in good working order. To do this, set up a schedule for how often each item or each area should be fully cleaned. In addition, set a policy to make sure that the workplace is neat and tidy at the end of each shift.
- Standardize - Gather information about the productivity of each shift on a given job. Once this information is available, figure out which shift's processes are most efficient. This is the process that should be used across all shifts.
- Sustain - Go back through each of the previous steps and make written notes of what is being done. Take that information and put it into an inspection schedule that occurs weekly (or however often is necessary in your facility) to ensure everyone is using the 5S system properly well into the future.
Resources
- https://www.essltd.ie/what-we-do/maintenance-asset-management-training/5s-the-five-pillars-of-an-effective-workplace/
- https://www.listaintl.com/resources-and-support/white-papers/5s-in-your-workplace/
Similar Articles
- The 5S System [Lean Manufacturing Methodology]
- 6S: Safety
- Toyota Production System (TPS & Lean Manufacturing)
- Understanding The 5S Methodology Implementation
- What is a CMMS? (Computerized Maintenance Management System)
- How to Implement 5S in an Organization
- Perpetual Inventory System
- Lean Safety | Understanding the Lean 6S Methodology
- Floor Marking For 5S