6S is the additional sixth pillar to the 5S methodology, a Lean concept that focuses on improving organization and efficiency in the workplace.
First developed by Hiroyuki Hirano of the Toyota Motor Company, the steps of 5S are defined as:

- Sort (Seiri in Japanese), eliminating unnecessary tools and items, and properly storing items that are used only every once in a while.
- Set in Order (Seiton), ensuring that tools and equipment are arranged so that workers can access what they need in the order they need, quickly and easily.
- Shine (Seiso), a thorough cleaning of an entire area or workspace. “Seiso” means to sweep or sanitize.
- Standardize (Seiketsu), implementing a universal and comprehendible system that workers can follow so that all organizational and efficiency efforts can be sustained for the long term.
- Sustain (Shitsuke), taking all of the previous steps and incorporating them into the work process as daily tasks or habits to ensure continuous improvement.
The sixth S stands for Safety and has recently become a new aspect to the 5S method. Issues with safety can be very wasteful and cause delays or defects in the production process, so implementing a safety program can enhance an organization’s 5S success. To do this, many companies regard safety as having an integral role within each of the five steps; although it is listed at the bottom, Safety is not often regarded as its own individual step at the very end and instead is commonly applied throughout 5S.
6S can be beneficial to a wide variety of industries. Although it is mainly used in manufacturing, it has helped health care facilities, offices, and repair facilities increase their overall efficiency and reduce waste. The concept is not just about cleaning your workspace; it’s an entire framework that emphasizes specific tools and cultivates a certain mindset in order to achieve efficiency, while practicing safety at every step along the way. Using this methodology requires the participation and ongoing effort of each worker, no matter what their role is within the business. Once 6S becomes a daily habit for everyone, your facility is well on its way to becoming more efficient, productive, and safe.
Tips for Implementing Safety into the 5S Framework
Safety plays an essential role in 5S, since it’s a key component to a variety of work practices. By cleaning regularly, organizing materials, and implementing standardized procedure, you make it safer for workers to navigate the worksite and perform their jobs.
Here are a few tips to emphasize safety in each of the five steps:
- Sort: Cluttered worksites not only interfere with performance, they also present a variety of hazards. Items on the ground can cause slips, trips, and falls, while things stored out of reach can further endanger workers. Organizing the workspace encourages efficiency and creates a much cleaner and safer environment.
- As you determine what is unnecessary, you may come across tools or equipment that pose a danger due to the fact that they have gone unused for a long time. For example, old machines may have exposed wires or no protection against pinch points. Keep an eye out for those unnecessary items that may be more than just taking up space—they could potentially pose a threat to safety as well.
- Set in Order: As you set equipment and tools in their logical place, keep safety in mind. Will a worker have to dangerously work their way around something to reach a tool? Is there a situation in which they have to leave equipment unsupervised as they search for the items they need? Sometimes a matter of safety is the biggest factor in determining an item’s proper place.
- This step also involves labeling, which provides an excellent opportunity to evaluate and label potentially unsafe spaces, hazards, or dangerous chemicals in the area. Visual communication is an important aspect to both safety and efficiency. As they Set in Order, many facilities implement new signs and labels or update their existing communication system.
- Shine: Once a workspace has been sorted and set in order, it needs to be fully cleaned and sanitized. This involves vacuuming, scrubbing, and other types of sanitation to completely remove accumulated dirt and grime. This keeps equipment in working order and reduces the risk of illness or injury from occupational exposure. It is especially important in environments that deal with hazardous substances or chemicals, to ensure that the area is completely clean.
- An important aspect to the Shine step is to conduct machine and equipment inspections, and make sure they are functioning safely and properly. Consistent maintenance keeps machines in working order. Not only does this save the company money in the long run by preventing break downs and defects, it also prevents personal injuries that may be caused by equipment malfunctions.
- Standardize: When you incorporate a consistent 5S system into your workplace, this allows 5S to become an aspect to daily operations. Standardizing your Sort, Set in Order, and Shine procedures ensures that all efforts to increase efficiency can be practiced for the long term. As you reach the Standardize step, now is the time to implement a universal system so employees understand what they need to do. Audit sheets and checklists make sure that daily 5S processes are carried out as they should be.
- By implementing a company-wide standard for safety, you can make sure that workers stay safe no matter what shift they’re on or what type of tasks they perform. Standardizing means that everyone does things the same way—and enforcing universal guidelines is one of the best methods available to ensure that people are not harmed within your facility. It also makes it easier to stay OSHA compliant, and reduces the risk of violations and financial penalties.
- Sustain: Improvement that is sustained over time leads to a more efficient and safer workplace. The final 5S step attempts to take each pillar and transform them into continual habits that workers incorporate into their daily tasks. While this is not going to happen overnight, it is well worth the effort. There are a wide variety of tools available that you can use to support your Sustain efforts: remind workers of each step with 5S banners, and keep a steady supply of 5S red tags on hand. This emphasizes the fact that your workplace values organization and efficiency as it continues to implement 5S, and keeps workers informed as they attempt to uphold the five pillars each day.
- Safety is also an ongoing practice that should be incorporated into both a workplace’s culture and people’s mindsets. Practicing safety is a daily effort. Remind workers to stay safe and protect themselves through 6S visual cues like wall signs that remind workers to clean up after themselves, or floor tape that indicates a hazardous area.
6S Lean Requirements
To successfully implement the 6S lean approach in your workplace, you'll need:
- A deep understanding of and experience with the 5S methodology, which involves organizing and maintaining a clean environment.
- A well-established system to identify and report any potential risks and dangers in the work area.
- Comprehensive safety awareness training relevant to the requirements of your industry.
- Regular discussions about 5s or 6s with your team to keep the workplace organized and efficient.
- The full support and approval from your upper management, along with dedicated resources.
The Importance of 6S for Workplace Optimization
Adopting the key principles of six S - which involve Sort, Set in Order, Shine, Standardize, Sustain, and Safety - can bring substantial benefits to organizations, and these include increased efficiency, improved safety of employees, reduced waste, and better communication among the workforce.
These steps help create a workplace that is neater, cleaner, and better-taken care of, which makes people work better and reduces the chance of accidents and injuries.
Implementing safety measures also helps protect the wellbeing of workers, which is absolutely crucial. Beyond the initial benefits of better efficiency and protection, the 6S also enables continuous improvement in the long run.
By setting clear ways of doing processes and encouraging everyone to take responsibility, companies can make sure that these vital principles become a regular part of daily operations and workflows in the workplace.
Benefits of 6S
Using the 6S approach at work can bring many great benefits, positively impacting overall operations and productivity. Here are some of the main advantages of implementing this system:
Higher Efficiency and More Productivity
The main goal of using the 6S method is to simplify work processes and get rid of wasteful activities. This is done by sorting out items that aren't needed, arranging necessary ones, and setting up standards for procedures, which create a more effective work environment. When employees can easily find the necessary tools, they won't waste time searching. This lets them focus more on tasks that add value to the company, resulting in improved overall productivity.
Cost Savings and Better Waste Management
This methodology helps people recognize and get rid of things that aren't needed (waste), whether it’s unnecessary inventory, slow processes, or resources that aren't being used well. When companies do this, they can save money by managing their materials better and reducing waste, leading to lower costs.
When a workplace becomes more organized and efficient, it's easier to manage supplies and reduce your storage requirements. This means they can use their materials and equipment, all of which contribute to lower expenses in daily operations.
Increased Production Quality
When a workspace is neat and organized, it's safer and easier to reach the components you need, and this makes it easier for manufacturers to focus on making high-quality products. If they use inspection softwares to check if they're following the 6S approach, they can also use it for quality checks. This helps them keep their customers happy and their business successful.
Reduced Workplace Risks
Safety is a key part of the 6S. When organizations follow this rule, they can find and address any dangers in the workplace. This could mean storing harmful materials safely, keeping walkways clear, and giving workers the personal protective equipment (PPE) gear. By doing this, they can reduce accidents, injuries, and time lost at work. They can also create a culture where safety is important, which helps keep their employees healthy.
Improved Communication and Teamwork
When employees work together to apply the 6S method, they can improve their communication and teamwork. As they sort, organize, and establish rules for their work area, they develop a shared understanding of their jobs and what they need to do. This helps them work together better, solve problems, and feel more connected to their work, which leads to better morale, job satisfaction, and overall unity in the team.
The 6S Argument: Should It be an Individual Pillar?
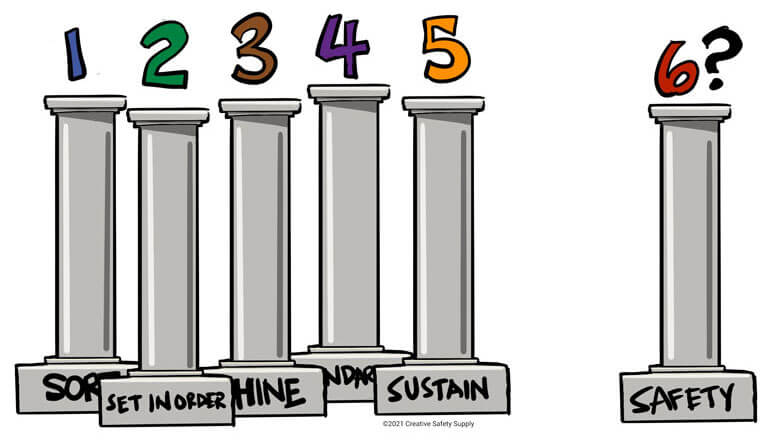
Some Lean professionals choose to leave out Safety when they implement 5S programs into their workplaces, mainly because they do not wish to cause confusion and make workers think that Safety is a separate step that doesn’t need to be considered until all the other 5S pillars are addressed, due to the fact that Safety is often listed last. Others believe that 5S and safety are most effective when they are kept simple and separate, with the purpose of each clearly distinct.
To determine whether implementing 6S in your workplace and adding that sixth pillar is the right call for your facility specifically, take into consideration the work culture you currently have and the culture you are attempting to create. While practicing safety can indeed promote efficiency and reduce waste, it may also lead to lost time and reduced efficiency, if, for example, you work in an office environment or other type of workplace that does not typically experience a high occurrence of hazards.
Could your workplace benefit from 6S? Are there ways you could use Safety to not only protect workers, but increase productivity and performance within your facility overall? Safety can be an essential component to the 5S methodology, but since every workplace is different, it may take some trial and error before you find the best way to implement this concept in your situation.
Similar Articles
- Lean Safety | Understanding the Lean 6S Methodology
- 5S System
- Floor Marking For 5S
- The 5S System [Lean Manufacturing Methodology]
- Understanding The 5S Methodology Implementation
- How to Implement 5S in an Organization
- Workplace Safety Inspections & Audits
- 5S Lean Training
- Quality, Health, Safety, Environment (QHSE) Management Systems