FOD is an important quality control and safety concept that refers to loose objects and small debris that have the potential to cause damage and injury in work environments. The term “FOD” is mainly used in the aviation and aerospace industries, but is important in any industry where quality and safety are a concern. For example, FOD is a serious matter in manufacturing environments, where quality assurance mandates that everything is in its proper place and staff are kept safe.
Depending on the context, the acronym FOD has two different meanings; it either indicates Foreign Object Debris, or, as a result of the presence of this debris, Foreign Object Damage. Consequences of an FOD incident can include:
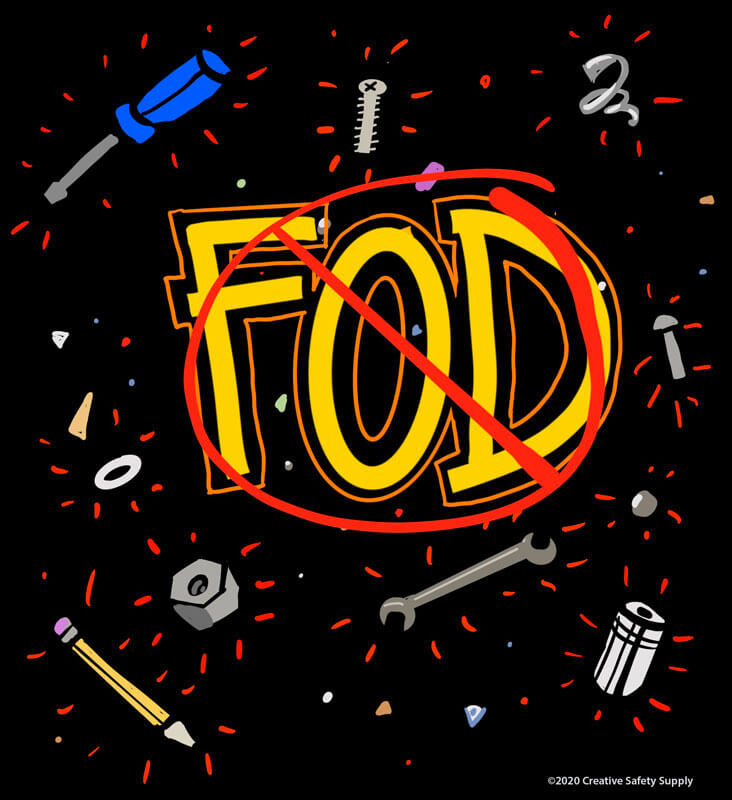
- Damage to airplanes, equipment, and devices
- Injury to staff, visitors, or passengers
- Safety violations
- Production delays
- Reduced quality in finished products
- Overall reduced efficiency
- In military circumstances, national security and mission capability may be compromised
Foreign Object Debris vs. Foreign Object Damage
Foreign Object Debris is any item in an occupational environment that is not in the location where it should be, or is not supposed to be there in the first place. This includes loose hardware, tools, small metal items such as nails and screws, baggage items, loose parts, rocks, weather conditions such as ash, hail, or snow, and even small animals like birds. In aviation, this debris presents a hazard to cargo, equipment, and aircraft and has a potential for injury to personnel. In manufacturing, this debris contaminates products or otherwise compromises standards of quality control, on top of threatening the safety of staff.
Foreign Object Damage occurs when debris compromises safety, quality, or functionality. This may be to an aircraft carrier, or a manufactured product. In the best case scenario, this type of damage only impacts overall quality; in the worst case, it leads to serious or deadly accidents, such as a plane crashing on the runway due to Foreign Object Damage to an engine.
FOD in Aviation
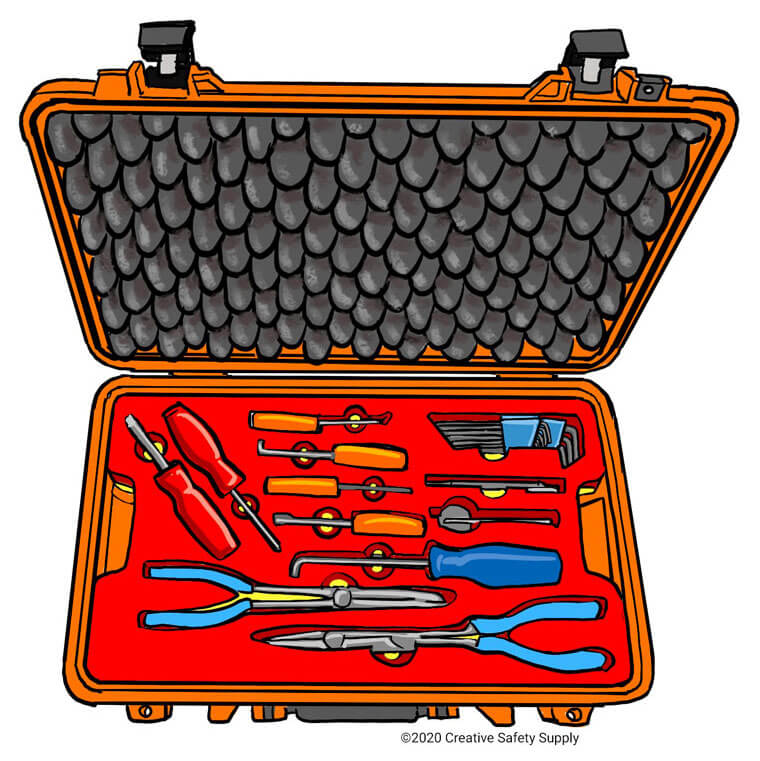
FOD is particularly prominent within the aviation due to the amount of risk it poses; even a small scrap of metal left on the runway can become lodged in engines or slash aircraft tires, and if the damage occurs while planes are attempting to take off or land, the results can be catastrophic. Jet engines also create a blast that throws debris everywhere and creates a dangerous situation for airline personnel on the ground, who might be hit by stones, broken pavement, broken luggage parts, mechanic’s tools, or tire fragments. FOD events typically peak during the early spring, as airports conduct construction, and during the winter due to snow and ice.
FOD causes extensive damage to airlines, aircrafts, and airports every year. Foreign Object Damage statistics are difficult to determine exactly, but Boeing estimates that FOD causes $4 billion in damages annually. The Federal Aviation Administration (FAA) provides specifications and guidance for using a number of tools to find and remove Foreign Object Debris, including visual inspections, sweepers and magnet bars, and automated systems. The FAA also enforces Advisory Circulars that provide guidelines for detection equipment, maintaining airport pavements, self-inspection for airport safety, and more.
FOD is also highly concerning to the military; not only are their planes subject to the same type of risks and consequences, but the military must also deal with FOD caused by missile strikes and strive to ensure mission capability and national security. A study by the US Air Force shows that the service paid $240 million from 1995-2004 for incidents involving Foreign Object Debris. During this period of time, the Air Force was involved in almost 800 FOD events, the average cost of which was about $300,000.
What is FOD in Manufacturing?
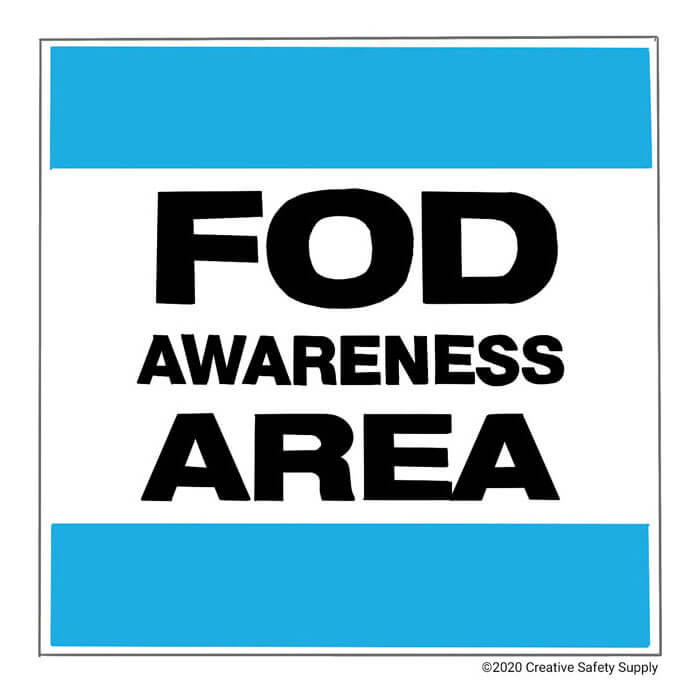
Non-aviation workplaces should also be concerned about FOD, as debris can present a safety and quality risk. Production processes and assembly lines involve a variety of tools and materials that must move quickly through the facility. Any space where products are received, shipped, stored, repaired, inspected, or manufactured can be designated as an area that may contain Foreign Object Debris. Many businesses utilize a standard three-layered system of signage for designating these storage or work areas and asking staff to be mindful of identifying and eliminating debris:
FOD Awareness Area
If you see this sign, you’re in an area where debris has a very low potential for impact, but is still a responsibility and staff must adhere to basic inspection procedures; all items should be accounted for and general housekeeping should be practiced. Examples of these areas include shipping docks and receiving docks.
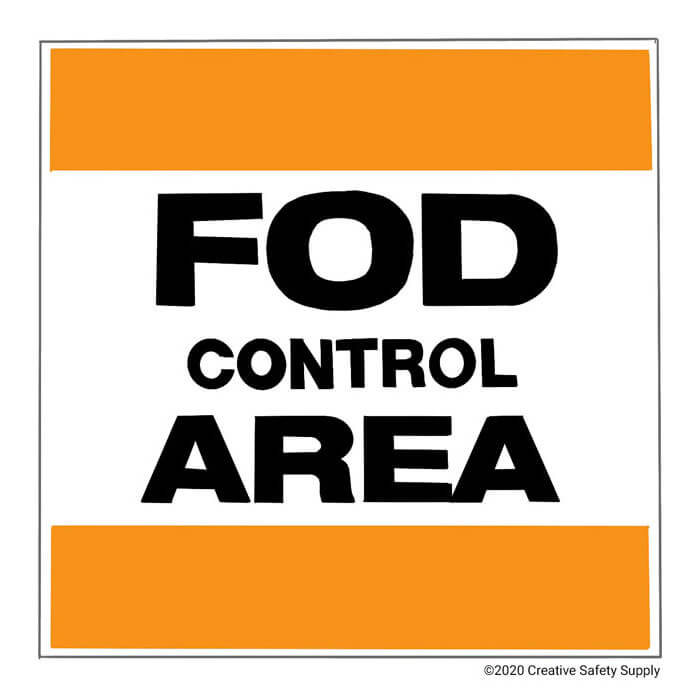
FOD Control Area
If you see a sign for this, you are in an area where debris has a higher, yet not severe, potential for impact. On top of basic inspection procedures, there will be additional Foreign Object Debris tasks and staff should have a higher sense of item awareness. Examples of these areas include modification processes, a packing area, and a parts warehouse.
FOD Critical Area
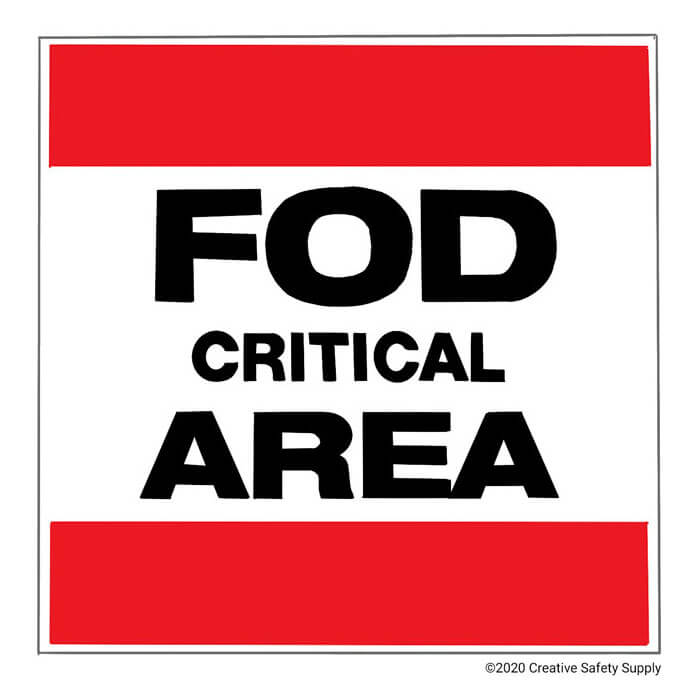
Signs for this indicate that you are in an area where debris has a very high impact potential and operations should be conducted with caution. Here, staff should adhere to strict inspection procedures and maintain the highest sense of awareness possible. These areas include assembly operations and open product housing.
Many facilities practice a “Clean As You Go” mindset, an ongoing method of removing debris during operations to ensure that the space and any products are free of FOD. This awareness should be enforced in all environments.
Controlling Foreign Object Debris in Manufacturing
In order to address and maintain awareness of the dangers of Foreign Object Debris, facilities should establish a comprehensive program that incorporates training, inspection, maintenance, and communication. Awareness and communication are at the forefront of FOD programs; controlling this dangerous debris begins with implementing wall signs and floor tape that make clear what type of FOD area workers are currently in and remind them to clean as they go. Whether staff should proceed with caution or simply maintain basic housekeeping practices, labels, floor tape, wall signs, and barricades are essential tools to make people aware that FOD has the potential to cause problems.
Another component to controlling foreign object debris is to keep your facility clean and organized by decluttering with 5S. This methodology enhances organization and efficiency through five phases: Sort, Set in Order, Shine, Standardize, and Sustain, which help eliminate unnecessary items and importantly, remove any debris. In addition, Implementing 5S can help workers incorporate a constant mindset of housekeeping, making “clean as you go” second nature during daily operations.
FOD Prevention Program Requirements
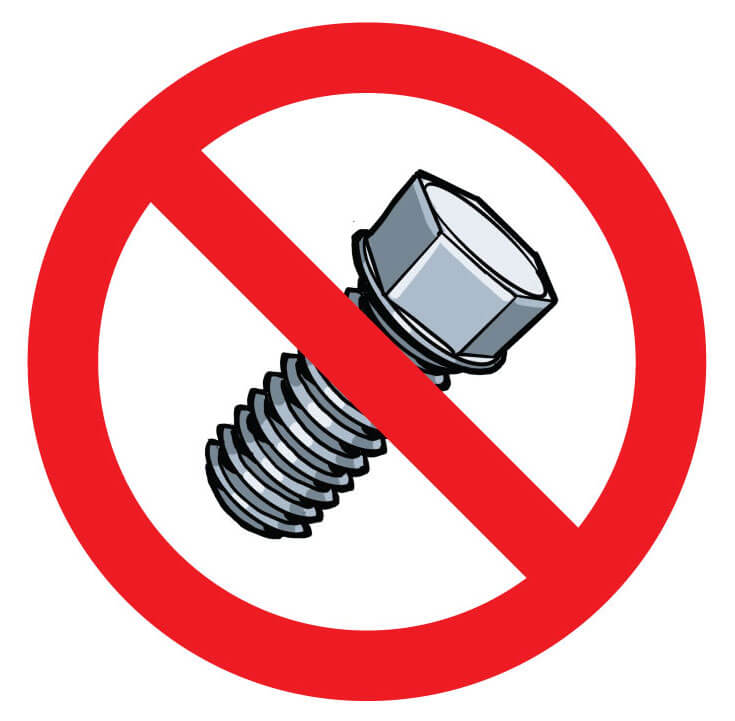
A business can develop an FOD Prevention Program to eliminate debris as much as possible, reduce its consequences, and prevent debris from contaminating work areas in the first place. Typically, a program is based on guidelines and standards that are issued by authorities such as the FAA. Major considerations of a prevention program are using area designations (awareness, control, or critical area) to achieve risk mitigation through different levels of control, and helping staff understand which preventative actions to take depending on the area.
Programs heavily focus on training and the following elements should be included:
- A description of the methods and housekeeping practices used to control Foreign Object Debris
- Designation of the personnel who are responsible for implementing and managing the FOD program
- A method of accountability for tools and other items at the beginning and end of a work shift
- A visitor protocol; visitors in FOD critical areas must be escorted at all times
- Reporting procedures for any missing or lost items
Foreign Object Debris Prevention Programs provide the information and procedures that staff need to eliminate debris successfully. An effective program greatly reduces the cost of Foreign Object Damage and helps keep workers safe by maintaining a mindset of keeping areas clean.
The Importance of FOD Awareness
No matter the environment, FOD will concern either safety, or quality. Foreign Object Debris isn’t just about equipment getting dented by a rock; damage from foreign objects can happen in a number of ways and often is a constant threat. Many businesses can benefit from implementing an FOD Prevention Program, and the most effective way to eliminate debris is to ensure awareness among staff. With conscientious housekeeping, adequate signage, and cleaning as you go, it is possible to control and prevent Foreign Object Debris.
Additional FOD facts:
- FOD stands for Foreign Object Damage or Foreign Object Debris, and it refers to any substance, debris, loose hardware, or article that is alien to a vehicle or system and can cause damage. FOD can result in minor repairs or catastrophic events, and it is a major cause of aircraft damage and unscheduled maintenance. Source: https://www.lockheedmartin.com/content/dam/lockheed-martin/aero/documents/scm/tandc/FOD/fod.pdf
- FOD prevention is the responsibility of everyone who works in or around aircraft, engines, parts, components, assemblies, or sub-assemblies. FOD prevention requires regular inspections, proper storage and handling, employee training, and awareness. Source: https://www.fodcontrol.com/what-is-fod/
- FOD prevention areas (FPAs) are designated zones where different levels of FOD prevention measures are applied. FPAs can be classified as FOD Awareness, FOD Control, or FOD Critical, depending on the type and stage of the manufacturing, modification, or operation process. Source: https://www.lockheedmartin.com/content/dam/lockheed-martin/aero/documents/scm/tandc/FOD/fod.pdf
- FOD walks and FOD sweeps are common methods of detecting and removing FOD from the ground or work areas. FOD walks are performed by personnel on foot, while FOD sweeps are performed by ground equipment such as vacuums, magnets, or sweepers. Source: https://www.flyingmag.com/5-things-you-can-do-to-help-prevent-foreign-object-debris/
- FOD barriers and FOD detection systems are tools that can help prevent FOD migration or entrapment. FOD barriers are physical or visual devices that block or mark the boundaries of FPAs, such as fences, signs, cones, or tape. FOD detection systems are sensors or cameras that monitor the presence of FOD on runways, taxiways, or ramps. Source: https://fodprevention.com/understanding-foreign-object-debris-and-damage-prevention/
- FOD can also be caused by wildlife, such as birds, rodents, or insects, that can enter or damage the aircraft or engine. Wildlife FOD can be prevented by using wildlife management techniques, such as habitat modification, exclusion, repellents, or removal. Source: https://www.grypmat.com/blogs/aviation/what-is-fod
Similar Articles
- Lockout/Tagout Program (How To Control Hazardous Energy)
- Quality Control in Manufacturing
- OSHA’s Guidelines to Protecting Employees from Coronavirus
- Workplace Safety Inspections & Audits
- 6S: Safety
- Quality, Health, Safety, Environment (QHSE) Management Systems
- How to Implement 5S in an Organization
- Lean Safety | Understanding the Lean 6S Methodology
- Quality Control