Lean methodologies have been used in a variety of industries for a long time. The way Lean is implemented varies from industry to industry. However, the primary goal of maximizing customer value while minimizing waste remains the same no matter where the method is used. For example, one popular area where Lean is used extensively is in the healthcare industry.
While much of Lean healthcare is similar to Lean manufacturing, Lean offices, etc., much of it is also quite unique. The reason being because medical facilities don't operate the same way other facilities do. Wrong decisions, bad scheduling, and a general sense of inorganization can result in patient death within an already incredibly complicated and busy environment. This is why Lean healthcare is widely seen to be its own stand-alone set of concepts. It’s most commonly used in hospitals, outpatient facilities, surgical centers, family doctor offices, and even dentist offices.
Learn all about the principles of Lean healthcare in this article so you can take the next step in using it yourself. Actively working to improve your environment little by little with Lean healthcare will eventually result in a complete turnaround regarding productivity and efficiency later down the road.
What is Lean Healthcare?
Suddenly deciding to implement a Lean healthcare model is not recommended without knowing exactly how it works. With that being said, having a deep understanding of what the facility needs and how normal day to day processes go is critical for being able to move towards a leaner goal. This basic understanding of how healthcare facilities work needs to go beyond just the administrative team at a hospital, and should extend to all the doctors, nurses, maintenance teams, and everyone else who works in the area.
Learning about the goals of Lean healthcare is a simple process but implementing those goals can be more difficult. Facilities will have to go through a constant cycle of monitoring the current situation, ensuring they are providing excellent patient care, and minimizing overall waste.
There are six words, it may help to think of them as a mantra, that work together to define Lean healthcare. They are as follows:
- Improvement – This isn’t just any improvement effort; improvement is meant to be continuous. Of course, perfection is pretty much unattainable, but that just means everyone must make an effort to get as close to perfection as possible. Every time a goal is met, or something has been improved upon, make the effort to raise the bar with the goal of creating an even better process. Managing the health of an organization is built upon this very idea.
- Value – This aspect of Lean healthcare is critical. Healthcare is defined by satisfying and providing potentially lifesaving procedures to patients. The whole industry is based on creating value for those that go to a hospital to receive treatment. By using Lean, value creation becomes clearer as wasteful practices are eliminated and replaced with better options.
- Unity – Bringing people together to achieve the goal of Lean healthcare is important for developing relationships between all departments. Not only does this bring people closer to the goal of continuous improvement, but it also prevents conflicts within the workplace for scheduling, protocol, and other important administrative and organizational objectives.
- Respect – Everyone within a hospital environment has an important job to do. This means the hospital custodian is just as important as the nurses and doctors. All of which deserve respect. That respect helps foster a trust between management and employees as well, creating more room for employees to take the reins regarding continuous improvement.
- Visual – While in school, teachers are prone to handing out tests that rely on student’s memories, when in reality jobs encourage employees to keep notes and use the provided resources to help them on the job. Apply that to the healthcare industry. There are visual cues all around a hospital and other health related facilities. Creating a visual workplace is Lean healthcare’s specialty. As a tool for conveying important information, visual cues keep a company organized and ready for day-to-day activities without any hiccups in the process.
- Flexibility – Situations change and can do so unexpectedly. With that being said, being able to deviate from standardized work smoothly, and with intention, is a must have skill for Lean healthcare centered facilities. This allows for more innovative solutions to be found and is added to the facility’s arsenal of strategic moves.
Remembering these six words for Lean healthcare is important for creating a new and improved standard that sticks around. Sadly, newly implemented Lean methods have a high fail rate due to a number of different factors. It may be because of a lack of buy in from the employees or the employer, quitting to return to familiarity, or sometimes concepts like Lean healthcare are completely misunderstood and subsequently dropped from the program because “it made operations worse.”
The fact of the matter is, when Lean healthcare fails it’s simply because there’s not enough of an understanding of what the program is supposed to do, and not enough drive from those trying to implement it to actually make productive changes.
The Five Principles of Lean
We’ve gone over the six-word mantra of Lean healthcare, but what about the entire basis of Lean thinking and the primary principles that make up the Lean manufacturing strategy? Whether that be for spotting and reducing bottlenecks, establishing a streamlined manufacturing process, and of course, eliminating those familiar eight wastes. Take a look at the following list of Lean manufacturing principles and see if you are following them already:
- Define Value – What is a customer willing to pay for a product? That alone is what value is defined as. This information can be gathered in numerous different ways, including asking the customer directly after a sale or performing a survey on the company’s website, if that is an option.
- Map the Value Stream – Mapping out the value stream allows the user to spot any inefficiencies within any given process. This allows for the company to receive more value out of the product they are offering to customers, as the cost prohibiting inefficiencies have been removed.
- Create Flow – After the 8 wastes have been removed from the process, the users of the Lean manufacturing method must work to smooth out the new process. That can include actions such as in-depth training, reconfiguring production steps or breaking them down into smaller steps, and lessening workloads.
- Establish Pull –This strategy is also known as a Just-in-Time production process. It aims to have the minimum amount of raw stock and finished product to meet demand and keep efficiency high.
- Aim for Perfection – Striving to perfect the above four principles is the most important objective of all. This drives employees and management to continually improve their workplace.
As can be seen here, the five principles of Lean manufacturing work together to achieve the goal of continuous improvement. There’s never going to be a perfect workplace because humans are built to always think of better ways to complete a goal. For that reason, finding the right avenue to reach those goals is one of the most important steps a facility can make for their future.
Lean Management
Just like with any other type of facility, implementing Lean healthcare will require effort from every employee. The management team is going to be where all of this begins. Having everyone on board, trained to understand how lean healthcare works, and the benefits Lean methods offer, will help ensure full participation.
Having a small number of senior leaders take on the role of Lean manager can help to ensure adoption by the rest of the staff. Depending on the type of facility that is implementing these lean strategies, the Lean managers will primarily be focusing on the types of changes to be made and getting them implemented.
The actual choosing of lean projects will be handled by small teams that include members from all impacted departments. In a hospital setting, this could include management, doctors, nurses, legal teams, maintenance teams, and more. Discussing the goals of any change, and identifying if there are any potential risks, will help to ensure everyone is on the same page.
Any change that is going to be implemented will start off by identifying a potential waste that can be reduced or eliminated and seeing how the change will impact the customers of the facility. Lean methods are often explored through the PDCA cycle, which stands for Plan, Do, Check, Act.
Identifying the 8 Wastes
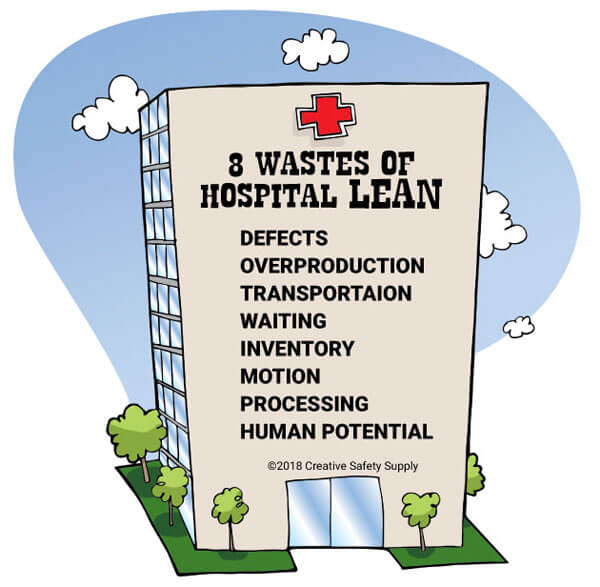
One of the first places to start with Lean healthcare is identifying waste. In the healthcare industry, a lot of tangible waste is produced in order to help protect the health and wellbeing of patients and staff. For example, needles can't be reused, everything needs to be washed or disposed of properly after each use, and so on.
However, wasted time is another matter that is often hidden within these physical objects that are thrown in the trash. Because of that, finding internal problems with the process can make become much more difficult to find. Once a facility understands what to look for, it can be a lot easier.
Let’s go over the generalized 8 wastes of Lean manufacturing but within the scope of Lean healthcare.
- Defects in Lean healthcare can include anything from distributing the wrong information by mistake, to missing items on surgical carts, to even administering the wrong dose of medicine. The best way to describe this waste is in terms of time. Wasted time fixing mistakes can be life-threatening in this occupation.
- Overproduction, just like in normal Lean manufacturing, is defined as doing more than what is needed by the customer. In the healthcare industry an excellent example of this waste is performing unnecessary diagnostic procedures on the patient.
- Waiting is one of the largest complaints within the healthcare industry, however, it’s not just the patient that is having that issue. Healthcare employees may have to wait for room to be disinfected, tests to come back, and anything else that may be a normal procedure in a health care setting. This is mainly the result of an unbalanced workload, which also happens to lead to more stressed workers.
- Non-utilized talent is detrimental to Lean programs as it directly works to discourage employees from contributing their ideas. This gives way to a high possibility of health care workers becoming dissatisfied with their jobs.
- Transportation is the unnecessary movement of items. Speaking in terms of healthcare facilities, this can be not only pieces of equipment and specimens, but also patients! Try and remedy this by improving the layout of the facility, move things around to where there is less of a distance to walk.
- Inventory is defined as the excess supplies a facility doesn’t need. Not only does it cause a storage issue, but in hospital settings excess inventory also means medications and supplies have a higher chance of expiring.
- Motion is the unnecessary movement of people. In warehouses, this refers to a lack in ergonomic safety as they may be lifting too many objects or needing to move from station to station frequently. The same goes for a hospital setting, but in this case, nurses, doctors, and other staff members may be walking miles by the time they get to leave work. A poor layout only tires out employees, consequently reducing efficiency.
- Extra-processing is when work is being done that doesn’t directly add value to the customer’s experience. For example, taking the time to fill out forms that are never used.
Some common examples of waste in healthcare facilities include the following. Can you pick out which waste they pertain to?
- Staff often walk long distances to get what they need. Repositioning supplies, and ensuring patients are situated in ways that minimize the need for doctors to walk around can be very helpful. Reference 5S here as that Lean manufacturing method has a lot to do with organization and placement of equipment for maximum efficiency.
- If you guessed Motion you were correct! If employees are having to walk miles in a day, something is very wrong.
- When working quickly in a medical situation, it is easy to contaminate unused instruments, gowns, or other items. These objects then either need to be disposed of or washed, which can be wasteful in terms of cost and time. Finding ways to protect these items without delaying care can be very helpful.
- If you guessed Defects you were right! Waiting is also a direct result of defects occurring in the workplace.
- Going to the hospital for something as simple as shingles should be diagnosable pretty quickly as it’s a common illness for those who contracted chicken pox as a child, and for its recognizable blistering rash and pain occurring on one side of the body. However, when the doctor unnecessarily demands blood tests rather than taking a simple tissue scraping or a sample from one of the patients blisters, it incurs unnecessary cost for the patient to get that test done and it takes longer for the patient to receive the care they need.
- If you guessed Overproduction you were right! Performing unnecessary diagnostics on a patient is time consuming and more than what the patient is in need of.
There are many other types of waste that can be identified in medical environments. Finding out which ones can be reduced, and which ones can be eliminated requires a lot of trial and error. It’s important to make sure the facility works together to predict what type of impact waste reduction will have on the patient and other customers of the facility. Making a mistake in how things are implemented can literally be a life-or-death decision, which is why it is so important to get it right the first time.
Improving Patient Safety
As surprising as it is, medical error accounts for the third leading cause of death in the U.S, right behind heart disease and cancer, respectively. According to Johns Hopkins, that’s more than 250,000 people, or 9.5% of hospitalizations, per year. Medical error related deaths have the potential to be completely preventable with the right resources, AKA Lean healthcare practices.
Improving patient safety can be a done a number of different ways in respect to Lean healthcare. The three strategies that stand out the most include:
- Quality Checks help minimize human error in both manufacturing as well as healthcare settings. This type of Lean process improvement will work to ensure nurses, doctors, and other staff are double checking themselves in regard to the patient’s needs in conjunction with the required process. Once that is complete, they are able to pass that correct knowledge onto the next person involved in the patient’s care. It’s a long game of phone tag that cannot be misinterpreted in the end.
- Standardization of Protocol is another extremely helpful Lean process. Keep in mind that standardization doesn’t mean rigidness! Flexibility is the name of the game in Lean healthcare because of all the scenarios that employees face every day. When we mention standardization, we are specifically talking about medical procedures such as how to insert an IV needle, how to disinfect a room, etc. Not, “every patient only has an allotted time to speak with a specialist about their symptoms.” That is specifically how some medical errors occur, when doctors and nurses are rushed into diagnosis because they have to keep up with a time slot.
- Mistake-Proofing is another excellent example of Lean in healthcare. Imagine the scenario of being in an operating room and an assistant hands the doctor a wrong tool or instrument. Not only can this compromise the safety of the patient being operated on, but it also points to the fact that there needs to be some sort of visual reminder for the correct tool. The solution to this problem would be to mistake-proof the equipment with labels, or even color code pieces that fit together so the wrong item isn’t being used.
Aside from Lean operations when it comes to patient safety in a healthcare setting, there are also other options. Those objects can include patient monitoring systems, making sure patients understand what their treatment entails, verifying all medical procedures, and promoting a team atmosphere between employees. Nothing will get better if people don’t work together.
There are countless solutions to improving patient safety within a health care setting. Using Lean in healthcare, while only starting to be implemented in the early 2000’s, is exceeding expectations for improving patient value and hospital efficiency.
What is a Lean Management System?
We’ve already established the fact that Lean is centered around value and efficiency, as well as the fact that eliminating waste is a big contributor to overall patient and employee safety. Yet, we haven’t made the connection that waste is the opposite of what is considered to be value-added. There are three parts that further define what a Lean management system is, and has to have, to be considered as such:
- The consumer must be willing to pay for the time it takes to produce an item or service.
- To be value-added, the product, service, or activity must be changed in a way that the customer is still willing to consume.
- It must be done right the very first time.
Only if these three requirements are met, does the new product mean it is value-added. However, this is in the scope of manufacturing or business practices. Healthcare is a whole different area where the customer is experiencing value-added services on the spot. This can mean anything from diagnosing their health issues, preventing future ailments, to even comforting the patient while they are in the hospital.
Lean management systems rely pretty heavily on the PDCA cycle. For healthcare specifically, they came up with the acronym FOCUS PDCA. There are two components of this Lean method that help further develop Lean management systems. The two acronyms stand for:
- Find a process to improve
- Organize the effort for improvement
- Clarify the current knowledge of that process
- Understand variation and capability
- Select an improvement strategy for continuous improvement
PDCA for specifically implementing the chosen solution determined in the previous steps of FOCUS stand for:
- Plan
- Do
- Check
- Act
These Lean management tools can be eye opening for the staff at a health care facility. With the newfound ability to find the root cause of a slowdown or other safety related problem, the possibilities for improvement soar in terms of long-term success and retention.
Lean Healthcare Tools
Lean healthcare strategies are implemented in a variety of ways. Aside from the methods that we’ve already discussed above, there are some physical tools that can be used to improve Lean in healthcare settings. These items can help to make it easier to follow Lean principles and ensure the standards in a facility are followed.
Some examples of lean healthcare tools include the following:
- Lean Healthcare Floor Marking Signs - Using floor marking signs can help provide information, keep things organized, and much more. There are many types of floor marking signs that can be used based on the needs of a medical facility.
- Floor Marking Tape - Floor marking tape can be used for clearly marking aisleways, giving people a path to follow toward specific areas, and more.
- Educational Resources - Having Lean healthcare books, presentations, or other resources available can help ensure everyone is on the same page when it comes to how a facility will use Lean strategies.
The most important tool for Lean healthcare is going to be training. This training can take place in seminars, meetings, flyers, supervisor discussions, written materials, etc. In addition to the initial training that team members will need, ongoing training is a must for keeping everyone on the same page.

Benefits of Lean in Healthcare Organizations
When discussing the benefits of healthcare systems that have implemented Lean methods, we have to address the primary outcomes that those programs offer. There are three different categories that Lean principles success in, if implemented properly:
- Healthcare system improvements. These mostly revolve around time.
- Improved admission, turnaround, examination, and dispensing times.
- The length of stay coupled with discharge rate, and scheduling times.
- Outcomes pertaining to patients.
- Patient satisfaction, a lower rate of re-admission, as well as a decrease in mortality rate.
- Outcomes pertaining to employees.
- A higher rate of employee satisfaction.
Implementing Lean principles into the lives of our front-line workers has the potential to be nothing but good if done correctly. There are some dissenters that claim Lean inhibits hospital function, but they often mistake Lean for cutting staff members and shortening visits with patients to “stay efficient” rather than the goal of being effective.
Similar Articles
- Applying Lean Principles in Healthcare
- 5 Lean Principles for Process Improvement
- Kaizen (Lean Continuous Improvement)
- Understanding the Principles of Lean Construction
- Continuous Improvement (A Kaizen Model)
- What is Toyota Lean Management?
- Kaizen and Lean Manufacturing
- What is Lean Logistics?
- Six Sigma Principles