Frederick Taylor, the creator of what we know as scientific management, or more popularly known as Taylorism, became a notable figure in the twentieth century because of his studies involving efficiency. By altering the way people work in industrial environments, Taylor was able to optimize productivity in the workplace.
Despite the improvements he made to facilities in terms of increased production, Taylor’s method was often met with resentment from employees. This was partly due to the high expectation of producing more product than before as well as the nature of the simplified and repetitive work. The dissatisfaction with Taylor’s scientific management method at the time of its creation is multifaceted, of which will be discussed later in this article.
Who Was Frederick Taylor?
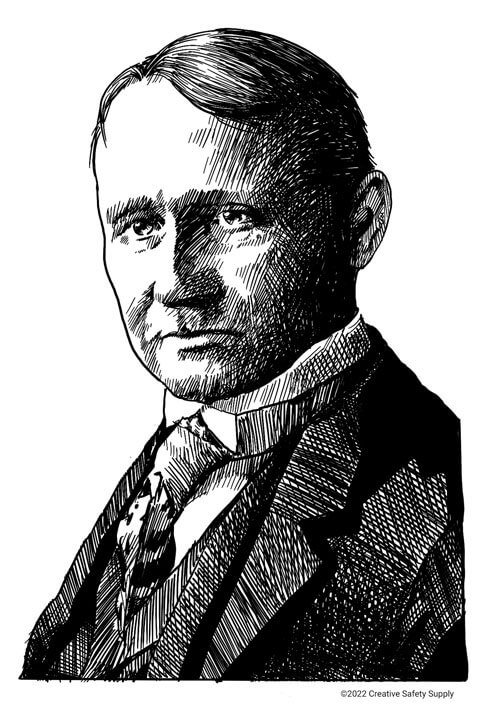
Frederick Winslow Taylor was born in 1856 in Philadelphia, Pennsylvania into a wealthy Quaker family. His father Franklin Taylor was a lawyer who made his fortune off mortgages and his mother Emily Annette Taylor was an active abolitionist. Growing up in a household like this, Taylor was able to pursue quality education from both his mother early on and institutions in Germany and France later in his life. Taylor came of age around the Progressive Era, later becoming one of the most influential minds from the late 1890 to the early 1900’s.
With the goal of one day becoming a lawyer like his father, Frederick had the goal of attending Harvard University. However, even after Taylor was able to pass the Harvard entrance exam with flying colors, he ended up choosing a wildly different path by becoming an apprentice as a patternmaker and machinist. Once he finished his apprenticeship at Enterprise Hydraulic Works four years later, he went to work at the Midvale Steel Works factory as a machine-shop laborer.
During his time at Midvale, Taylor ascended the ranks within the organization incredibly quickly, partly due to his exceptional talent with machines. To elaborate, from 1878 to around 1890 he began as a laborer and was promoted to time clerk, then journeyman machinist, then gang boss over the lathe workers, then to machine shop foreman, next a research director, and then finally chief engineer. Throughout all this, Taylor was also working to get his mechanical engineering degree from Stevens Institute of Technology, achieving that goal in 1883.
Aside from his talent in engineering, Taylor’s family was friends with one of the owners at Midvale Steel, Edward Clark, which may be another reason why Taylor was able to move up within the ranks so quickly.
As the machine shop foreman at Midvale, Taylor noticed that his workers and the machines they were operating were not performing as best as they could. At the time, this practice was called soldiering. Management believed this act resulted in higher labor costs. Once Taylor came to this realization, he began to expect more from the workers and began to study the optimum output of both man and machine.
Taylor’s obsession with productivity took off from there. He was led on a path that not only was supposed to improve workplace production, but also led him to creating a new business for himself as a management consultant, the first job of its kind.
Taylor’s Thoughts on the Cause of Soldiering
Taylor believed there was a particular cause for why employees were working well below their abilities, an action referred to as soldiering. The three causes that he contributed this behavior to were:
- The belief that if they were more productive, workers would lose their jobs since fewer of them would be needed to complete the job.
- The fear of a faster paced process becoming the new workplace standard along with the worry that they will not be paid for the greater amount of work they do. Taylor believed that workers were incentivized by money.
- He claimed that workers were slow because the process hadn’t been standardized. This practice referred to the fact that everyone was doing the same job differently.
With these assumptions in mind, Taylor began his work on optimizing factory processes that essentially equated workers to machines. A process he called scientific management.
The Principles of Scientific Management
During his studies involving the utilization of stopwatches on the factory floor as well as one of his most memorable experiments with shovel size, Taylor developed what he called the method of scientific management. It consisted of the following four main principles:
- The replacement of rule-of-thumb work methods with methods based on a scientific study of the required tasks.
- Scientifically select, train, and develop each employee rather than passively leaving them to train themselves.
- Work with the employees to make sure the defined methods are being used properly.
- Divide work nearly equally between managers and workers, so that the managers apply scientific management principles to planning the work and the workers perform the tasks.
Taylor believed that any flaws within a process can be fixed with improvements made to the management methods used by the facility. Furthermore, on the subject of improving worker productivity, it was conceived that management must optimize the way work was done down to the second.
Criticism Of Taylor’s Scientific Management
Briefly mentioned earlier, Taylor’s strategy for scientific management was excellent for businesses in terms of production. However, it was met with scorn from not only workers but unions as well. Let’s dive into why these feelings were present in this type of new working environment:
- Scientific management unfortunately invited the exploitation of workers. Due to the focus solely on producing product faster and performing tasks faster, not only the quality of work suffered, but the value of the product suffered as well since workers were being rushed. That exploitation also led workers to join unions for protection, causing a serious trust problem between both management and their employees.
- There was a problem with the chain of command. What came to be known as the eight-boss method wreaked havoc on workplace organization and the chain of command. This was done by dividing the management tasks into subtasks, essentially creating a series of different management positions that workers had to report to.
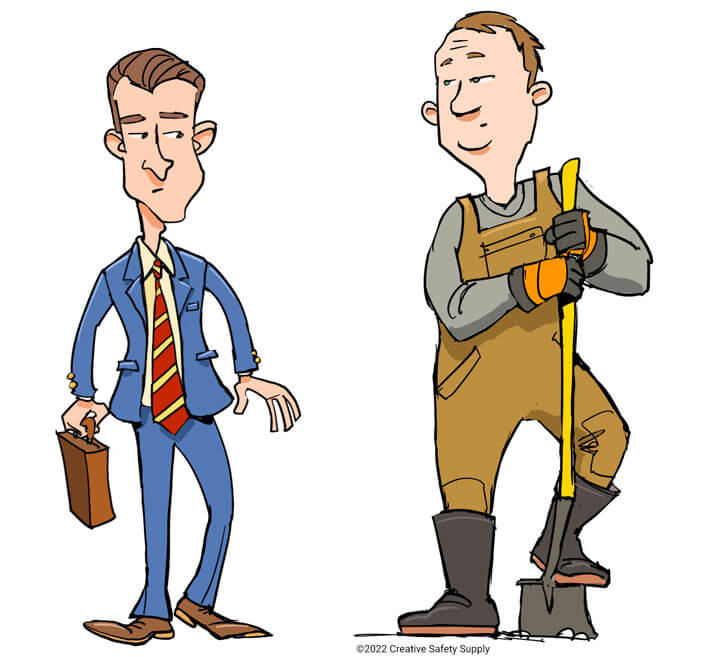
- Workers were equated to robots. In Taylor’s mind, workers in a factory were more akin to mechanical assets. This meant that they were replaceable and had to perform repetitive tasks for their entire shift. The nature of this type of work took a toll on worker morale.
- There was a clear divide between management and employees. There were the “planners” and those that performed the task. While this seemed efficient at the time, it must be realized that the planners must also participate in tasks, so they know how much work is manageable.
- It was only ever about the individual workers, never the whole workplace community. The success of a workplace depends on both the individuals and the entire workplace. This was not a factor in Taylor’s teachings.
- Motivation through higher pay. While higher pay increases quality of life, it’s not necessarily a fix all as people also have social needs that must be met to feel fulfilled. Taylor did increase pay for those that did the most work, but at the cost of their morale.
- Scientific management takes a very narrow approach in application. At the time, scientific management was only applicable to manufacturing facilities where there were a lot of small steps that needed to occur to create a physical product.
Now, as with every manufacturing method, there are pros and cons. Especially the older methods that were being experimented with at the time. The fact of the matter is scientific management was specifically made to benefit the company in terms of productivity. However, at the time there needed to be a lot more work put in for the human aspect of working. By that we mean respecting workers and seeing them as not just tools, but creative potential for improving the workplace.
Taylor’s Relationship with ASME
Taylor wrote several papers that he presented to the American Society of Mechanical Engineers beginning as soon as 1894. Those works included:
- Notes on Belting (1894)
- A Piece Rate System (1895)
- Shop Management (1903)
- Art of Cutting Metals (1906)
- The Principles of Scientific Management (1911)
His relationship with ASME extended even further in that he was president of the organization from 1906-1907.
Taylor’s Contribution to Lean Manufacturing
While Taylor did manage to revolutionize the way people worked during the early twentieth century, scientific management and Lean are quite different. In fact, Lean and scientific management differ on all levels regarding purpose, practice, and outcomes. Let’s run through the basics of each.
The purpose of Lean is to achieve less waste in working conditions by working together to improve and produce quality product. It is practiced by respecting people and always seeking improvement. The outcome is a more efficient workplace where employees feel fulfilled in their contributions as well as respected by all levels of management and employees.
On the other hand, Taylor’s vision of scientific management takes on a role that more accurately wants people to perform tasks as machines would. The purpose of Taylorism is to increase production and do so as efficiently possible. Tasks are optimized to the point where a single laborer is assembling one component and handing it off to the next worker in line.
Scientific management is practiced primarily by separating two types of workers, the managers “those who know” and the laborers, “those who do.” The outcome was supposed to be a completely optimized system that performed in a way that was perfect in terms of output. Unfortunately, this method wasn’t well received by employees because they were being treated less than humans and more like machines. Fully replaceable if they did not meet the expectations of management.
Now, this flawed method didn’t exist to just be forgotten. Other bright minds in the world of industrial engineering were heavily influenced by scientific management. In fact, you could say that the flaws and uproar that Taylorism towed behind it, paved the way to other methods that resulted in a more respectful workplace.
That being said, you have to start somewhere to find what exactly works the best. And while Taylor thought he had created the best system, people realized that it could change into something better and more beneficial to both the worker and the business, as well as the consumer.
The Influence of Scientific Management Globally
Taylor’s scientific management method influenced several different well-known figures in history during the twentieth century. Those people are as follows:
- Henry Ford hired Frederick Taylor to observe his production line and workers to improve production times. It worked! The system that Ford implemented shaved off a whopping 10 hours off manufacturing time from 12 hours and 8 minutes all the way down to 93 minutes total.
- Frank and Lillian Gilbreth developed what were known as the motion studies once they learned of Taylor’s method for studying production timing. Eventually the two methods were put together to create the Time and Motion Study that became intrinsic for the efficiency improvement movement. Lillian specifically introduced psychology to management studies.
- Joseph Juran worked in a world where Taylor’s methods were popular. He is credited with adding the human element to the concept of quality management.
- Henry Gantt worked to develop scientific management further with his specialized work management chart referred to as the Gantt chart.
- Morris Cooke worked closely with Frederick Taylor on scientific management concepts. In fact, he ended up writing his own book titled Industrial Management.
On the global scale, several countries took to Taylor’s method. France used scientific management methods post-war, Canada employed the method, and several other countries adapted scientific management to their own unique needs.
Overall, scientific management is what set the ball rolling in terms of improving workplace efficiency and as the theory changed over the century, it has led to other more productive and healthy workplace management methods like Lean.
Similar Articles
- Henry Ford and Development of Assembly Lines
- Frank and Lillian Gilbreth: Standardization, Ergonomics, and Lean Manufacturing
- William Edwards Deming: The Father of Quality Management
- Eli Whitney: A Key Player in the Development of Early Lean Manufacturing
- A Look at Training Within Industry (TWI)
- Peter Drucker: The Founder of Modern Management Studies
- What is Toyota Lean Management?
- What is a CMMS? (Computerized Maintenance Management System)
- Calculating Overall Equipment Effectiveness (OEE)