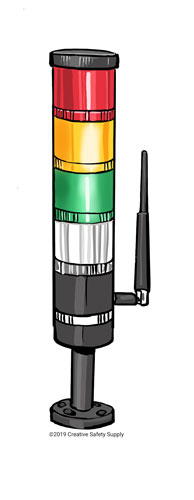
An Andon is a manufacturing term referring to a signal used to alert people to a problem with a process or an issue with quality. An Andon system is designed to stop production when a defect arises, and work is stopped until the issue is fixed. The use of an Andon is core element of Jidoka, the component of the Toyota Production System that means automation with a human touch. The goal of Jidoka is to improve quality, and an Andon is a signal that can identify quality problems right away. Toyota used the term Andon, a Japanese term meaning lantern, to describe the signal system they used to improve response time. Although Andon was originally developed by Toyota, the Andon system has become common in Lean manufacturing.
How does an Andon system work?
An Andon come in several forms but the goal of an Andon is to improve the flow of communication in case any problem arises. The original concept was called the Andon Cord and like the name suggests, it was a rope located above the manufacturing line that was pulled to activate the Andon. The Andon would alert workers to an abnormality in the production line, and all operations would cease until the issue is addressed. Modern versions of the Andon however, are typically activated automatically. For example, a light post with a green, yellow, and red light that changes color when a problem arises is an Andon.
Andon Light Colors
The color flashing on the Andon tower light represents the condition of the system and the action that needs to be taken. For example, if the Andon is:
- Green: Condition is normal; operations continue
- Yellow: A problem has appeared; the problem needs to be investigated and identified
- Red: Production has stopped; a supervisor or manager is needed
Electronic Andons can display the state of current processes on a screen, and images or text can change color. Some Andons can even have audio elements that play coded tones with different tunes used for different alerts.
Why is using an Andon important?
Any signal that is triggered by a process issue is some kind of Andon, common triggers include part shortage, defects, tool malfunctions, and safety problems. When workers hear or see the Andon alert, production is stopped before any other issues happen, and assistance is called over to address the problem. Using an Andon system will result in better quality products, an efficient production line, and reduced downtime. Additionally, Andon alerts can be recorded to help managers identify areas of improvement in their facility. Ideally, every workstation would have an Andon button or cord, so when a problem does happen it's easy to know exactly where the problem occured.
In daily life, many Andons exist outside the workplace, too. When the fuel warning light comes on in a car, that's a signal to refill the vehicle's gas tank so the process of driving can continue. If someone leaves the refrigerator door open in the kitchen, some fridges will start beeping to alert people to take action and close the door. Andons can make almost any job easier.
Additional Andon Light facts:
- Andon lights are a type of signal light that notify workers when there are problems with the production line. They can be activated manually by a worker using a pullcord or button or automatically by the production equipment itself. Source: https://en.wikipedia.org/wiki/Andon_%28manufacturing%29
- Andon lights are part of the Andon system, which is a visual management system used by operators and managers in lean manufacturing to easily determine and display the status of production lines. It originates from a Japanese term meaning “paper lantern” with a more accurate English translation as “sign” or “signal”. Source: https://safetyculture.com/topics/andon/
- Andon lights typically display three main colors: green, yellow or amber, and red. Green means production is normal or running smoothly, yellow or amber means a problem has been identified and needs to be fixed, and red means production has been stopped and requires immediate attention. Source: https://www.erp-information.com/andon-lights
- Andon lights are one of the principal elements of the Jidoka quality control method pioneered by Toyota as part of the Toyota Production System and therefore now part of the lean production approach. It gives workers the ability, and moreover the empowerment, to stop production when a defect is found, and immediately call for assistance. Source: https://www.lean.org/lexicon-terms/andon/
- Andon lights can be integrated with other types of signals, such as audio alarms, text, or graphics, to provide more information or guidance to the workers and managers. Some modern Andon systems can also be connected to a database or a software application to log and analyze the data on production issues and performance. Source: https://signalguys.com/Andon_c_178.html
Similar Glossary Terms
- Jidoka
- Lean Production
- Kanban – Defined
- Toyota Production System
- Poka Yoke
- Just-in-Time Production
- The Genchi Genbutsu Concept
- Countermeasure
- Waste of Overproduction